Development of the Moebius Models 1/72 SKIPJACK Model Kit and its Conversion to R/C Operation, part-2
By David Meriman
A Report to the Cabal:
The research I did in support of the Moebius Models 1/72 SKIPJACK kit resulted in a rather thick folder of plans (both BuShips based and private sources), photographs, tables, and news clippings.
Pull up a chair, boy's and girl's, it's Story-Time with Uncle Dave:
In the early-70's while working as an exhibit maker (and toilet-scrubber) at the Submarine Force Library and Museum I was tasked with the bagging for burn, filing cabinets full of American submarine plans; Booklet of General Plans and Docking plans dating back to the A-class up to and including the GUPPY converted TENCH class boats. Those hard copies, blueprints if you will, were being replaced by micro-film captures of the documents, and the museum wanted our old, bulky, dusty prints out of the way. It was all un-classified.
Hmmmm .... what to do?
As if by magic, most of that trash wound up at my home.
Unknown to me, at a different location on the upper base, some of the General Arrangement post war diesel and older nuclear submarine plans had also been de-classified and scheduled for disposal. Enter Jim Christly, fellow model builder, canvas artist, historian, and well-known author. Jim also worked at the upper base, and in his travels found where those plans were and -- knowing my keen interest in all things SKIPJACK -- one day stopped by my work-shop/dungeon and tossed a set of down-graded SKIPJACK documents in my lap. Wow!
Many years later...
Greg Sharpe -- one of the finest r/c model submarine fabricators and drivers on the planet -- had set up a business producing and selling builder's plans of modern submarines. He had always been very helpful with my various researches, so I reciprocated and shared with him the SKIPJACK file which contained good quality copies of the BuShip drawings. Eventually, Greg produced an excellent, well formatted set of drawings.
Long story short: Greg's drawings were the back-bone of the package sent to China to get the SKIPJACK kit tooling made. Accompanying the research package was a completed and well detailed D&E Miniatures 1/96 SKIPJACK model intended for scanning and a CAD file generated.
After Moebius committed to the project of producing a 1/72 SKIPJACK kit, I took on the assignment of lead-man. My job being to gather and send off to Dave Metzner, the Moebius Product Development guy, a package containing all the information the Chinese needed to render an accurate kit.
I'm pictured here surveying the mock-up they sent. That mock-up, 3D printed in accordance to the materials I sent them, had major problems! That list you see me compiling grew to an eventual three pages of things that had to be fixed.
One of the many faults found on the mock-up identified here: miss-location of the transitioning fillet between diesel exhaust fairing and sides of sail. Like all other anomalies found on the mock-up, I performed a re-contouring action to get the mock-up parts as close to documentation as I could. Note the pictures of a SKIPJACK sail under the work -- sometimes photos are the only way to go when the plans are not enough. Such was case here: The plans showed only the plan and profile of the fairing-sail interface, but no indication as to the radius and sweep of the fillet between the too structures. This is when you make use of your well-trained eyes and good old computer number-one.
In parallel with mock-up correction I set about the task of working up masters to enhance the look and function of the many retractable masts that fit within the SKIPJACK's sail. The proposed kit parts had masts only long enough to project atop the sail in their 'raised' positions, but only had enough material in they're bases to fit inserts built into the top of the sail. Not suitable for practical retraction/extension.
A linear screeding tool was used to form half-mast masters from a two-part automotive filler. The brass screeding blade between my hands has a fence that rests on the outer edge of this molding-board, I lay down some catalyzed filler on the board, under the opening cut into the blade of the screeding tool -- that opening representing 1/2 of the desired mast section. In operation, I pull the blade lengthwise across the mold board, the opening in the blade forcing the filler to adopt the shape of the half-mast. The mold board was pre-coated with mold-release wax to aid a clean break-away of the half-mast master off the mold-board after the work was done. The master was broken into two equal length pieces, and glued together, face-to-face, making a complete mast master.
This is how far I got with the retractable masts and bridge and lower platform masters before being informed that this work, if it were turned into tooling and kit parts would radically increase the price of the kit. So, this work sits in a box awaiting the day I have time to produce after-market sail mast, scope, antenna, and sail interior detailing kits. If no interest materializes, then this stuff will join two shed fulls of similar crap for my estate executor to haul to the local land-fill. (I don't like to think about it).
I don't know what the hell happened in China with the propeller, but, the mock-up they sent was horrible! No good reason for it: I sent them a 1/96 sample of the SKIPJACK wheel for scanning. What happened?!
Anyway...
After examination and rejection (at considerable velocity, against the far wall) of the mock-up propeller I made up my mind to build a physical 1/72 propeller for them to scan. It being my hope that they would produce a CAD file off the new propeller from which to eventually drive a CNC machine for tool fabrication.
Here's the build-up of that propeller master. It's my practice to make one propeller blade master; pull a high-temperature RTV tool from that; cast up the required number of blades; then assemble those blades about a RenShape hub mounted on a blade assembly jig, securing them with CA mixed with baking soda. Me much smart!
The amount of corrective work required on the hull necessitated creation of this securing-layout fixture. It would permit me to accurately lay down radial lines, longitudinal lines, and to loft -- directly off a scale drawing of the SKIPJACK -- engraved line locations. The pen loaded surface-gauge, running along the vertical, longitudinally running board, marks off longitudinal lines. The surface gauge mounted to the transverse vertical board lays down radial lines -- such as the station/section lines spaced evenly along the length of the hull.
Proper lay-out is everything in model making -- if you don't establish and follow your datum points, lines, and land-marks, you will never achieve reasonable symmetry. (Sounds like something Buddha would have said).
The securing-layout fixture partially disassembled to better access to the mock-up for re-contouring. Note the cardboard station templates in foreground -- used to check my work as I re-established the round to the erroneously flat portions of the mock-up.
I lay down some filler, let it cure, then work it, a bit at a time, with a course file, constantly checking the contour with the templates.
The only non-round portions of the SKIPJACK hull are two deck flats, one ahead, and one astern of the sail. Flat to give assured footing to line-handlers and other men on deck. I elected to first get the entire upper hull back to round with filler (no corrective actions required to the lower hull), and only then to build up the flats. The two flats were re-established by screwing down suitably shaped .030" thick aluminum deck flat forms upon the hull and building up filler between the hull and form edges.
See the long lines either side of the sail on the drawing taped to the vertical, longitudinally running board? Those lines simply identify the anti-skid outline. However, I failed to inform the Chinese of that and they interpreted the lines to denote a flat, so that's how the mock-up hull came out, one long flat to the deck, not two smaller ones. My mistake -- not properly explaining that issue in the cover-letter that accompanied the documentation I sent -- which cost Moebius both time and money. Lesson learned!
Note how I used different colored hardener in the filler mix to identify high and low points as I applied and filed back the filler as I restored the upper hull back to a round section.
Before I could scribe in all the detail lost when I re-built the top of the upper hull, I had to first lay out, in pen and pencil, the position and shape of the eventual engraved lines. The securing-layout fixture made that chore a quick and accurate one.
After layout I scribed in all the lines lost during the hull re-build. You can make out the forward flat very well in this shot. Some of the engraving to be performed represents the upper sonar dome window, upper torpedo tube shutter-doors, forward escape buoy, escape trunk hatch, torpedo loading hatch, reversible cleats, salvage plates, capstan head, etc.
I also failed to provide the Chinese with any information that identified the point of rotation of the full-flying control surfaces. So, they took they're best guess as to center-of-rotation for each control surface .... and got each and every one wrong. Not a big deal to static kit-assemblers, but for those who would go on to assemble the kit for r/c operation, control surface center-of-rotation position is a vital consideration. Both for scale looks and flutter avoidance.
So, I modified the mock-up control surfaces with properly located foundations to accept the control surface operating shafts. I should have been on top of this from the beginning of the project, but missed it. Bad.
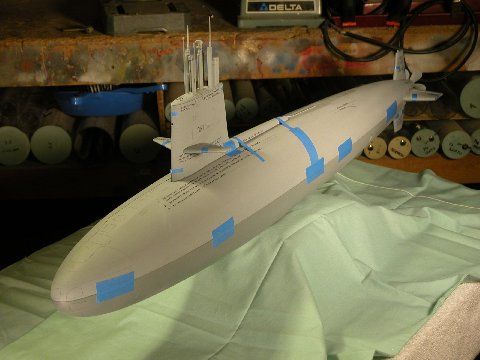
Finally, I got all the fixes I could identify incorporated into the Chinese mock-up. here it's been test-fit together, ready for shipment to Moebius who got it just in time to make the Chicago iHobby show last year for the first public showing of the Moebius Models 1/72 SKIPJACK. It was well received.
After the show, the corrected mock-up was shipped to China for laser scanning, which produced a file suitable for CNC cutting of the production tools. The writing you see on the mock-up are there to identify areas of change -- just to make sure my changes work would be identified and the re-contoured areas recorded into the software.
Shots of the mock-up, at the IHobby show, can be view here, along with comments:
http://www.rcgroups.com/forums/showthread.php?t=1526171
http://www.rcuniverse.com/forum/m_10776725/tm.htm