Things are quiet on the homefront. Due to the nature of my wife's cancer, even though the pathology was clear, will undergo a short cycle of Chemotherapy. All of this will be over in mid-March and we'll be happy when it's done.
During her recovery I didn't work in the shop much, but I did a ton of drawing and got a lot of printing done. This is an example of one load with lots of odds and ends for gun house details. This pile includes shaped junction pieces to help me glue the roof plates at the correct angles and those really neat "tractor seats" for the trainer and pointer positions. I had found a bar stool with the correctly shaped seat on the SketchUp 3D Warehouse and then modified it to print and conform to the ship's seat size and shape.
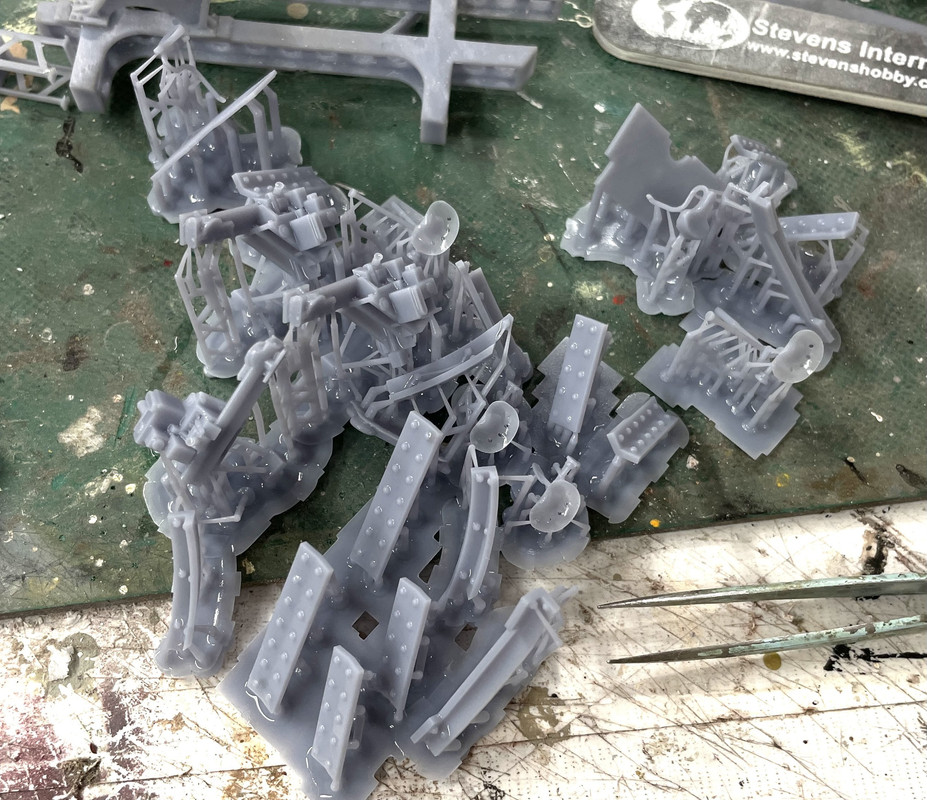
Here's a closer look at the seats. There's one more that's printing now. It's the bicycle-shaped seat for the sight setter position. It's in the pile above, but, the bottom mounting flange was a separately grouped drawing that I neglected to combine with the overall model. When I conveted to the STL and then the printer, that flange wasn't there so the seat pole was just dangling in open space.
This is the pointer seat:
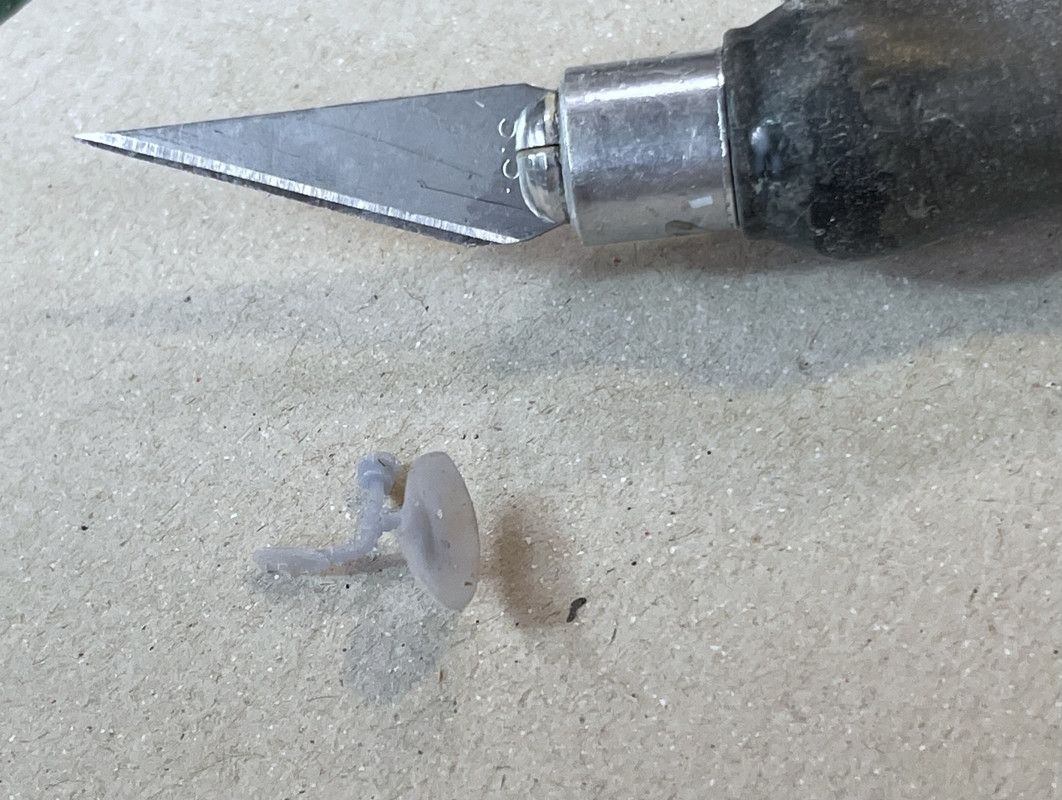
And this is trainer seat. Both are REALLY delicate, but well cured and formed.
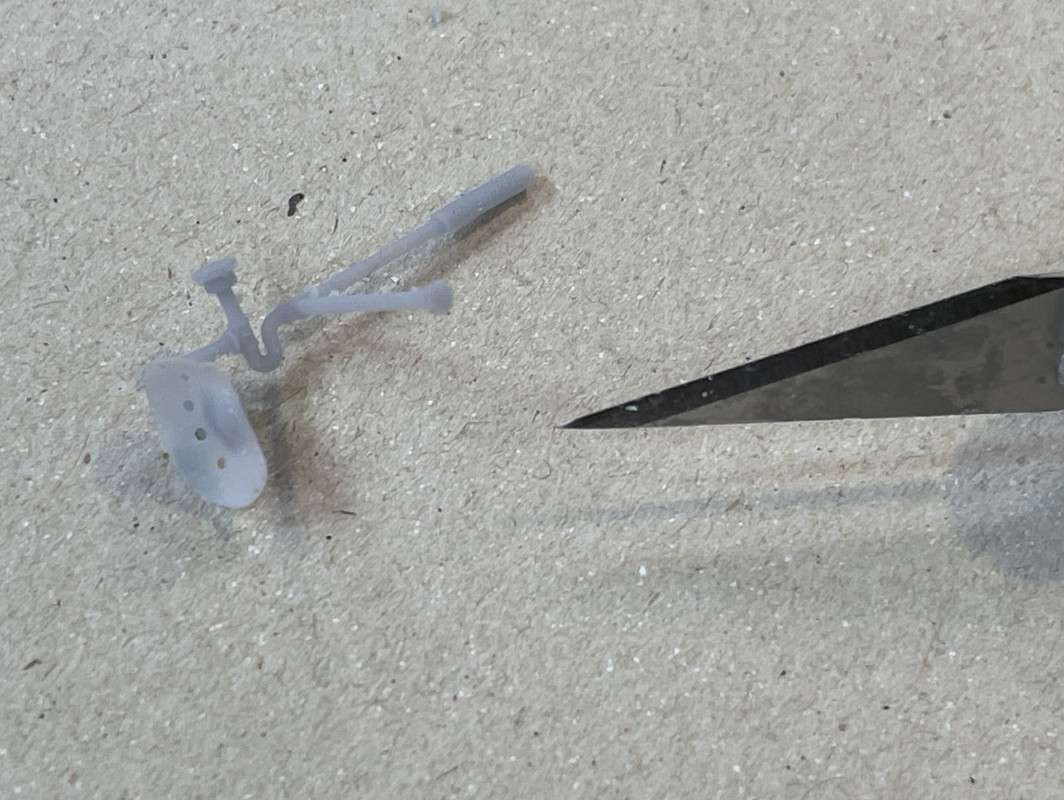
The assembly process has officially begun. I glued the gun house base plate to the underframe. Styrene to UV rensin? Only with CA or epoxy. UV resin is impervious to most common plastic solvent.
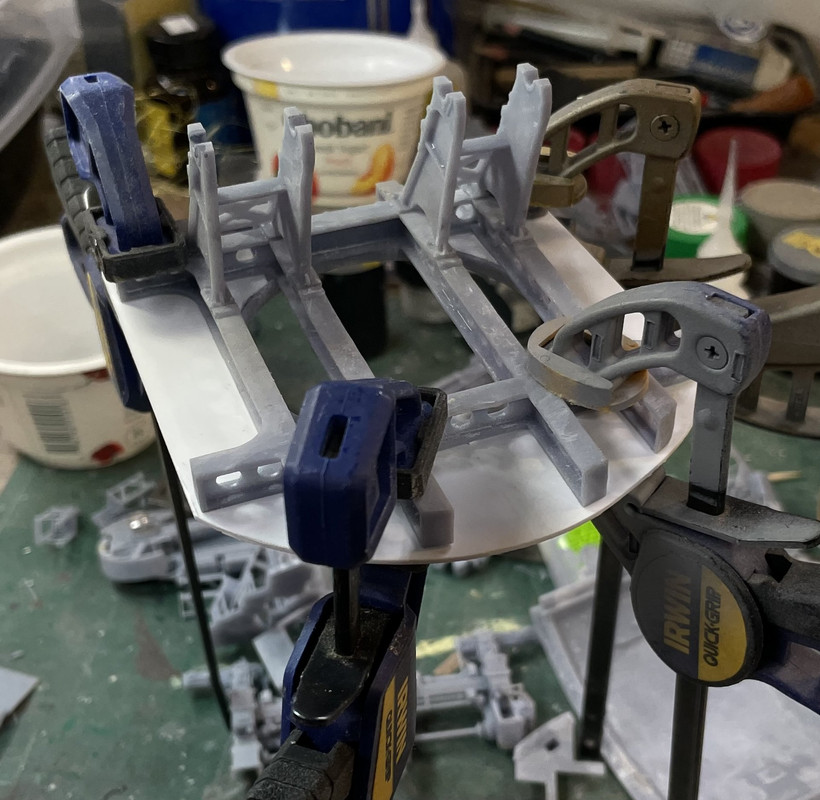
The print package was the flooring pieces. Ryan sent me photos of all the floor plates in the gun house and I was able to reproduce them with reasonable fidelity. I was struggling with the diamond plate. I had downloaded a piece of this from the 3D Warehouse. The artist didn't group the pattern separate from the substrate so when I attempted to trim or enlarge the sample to fit my various piece shapes, I had to deal with the substrate disappearing, reversing faces, or just being a pain in the butt. Finally, I decided to separate the diamond patterns and group them. This allowed me to shape the substrate, which is quite easy, and then drop the diamonds onto the surface. Since they are their own group, I was able to erase them in one tenth the time it was taking before.
I designed he little box steps at the rear hatch openings to assemble with the curved angle brackets.
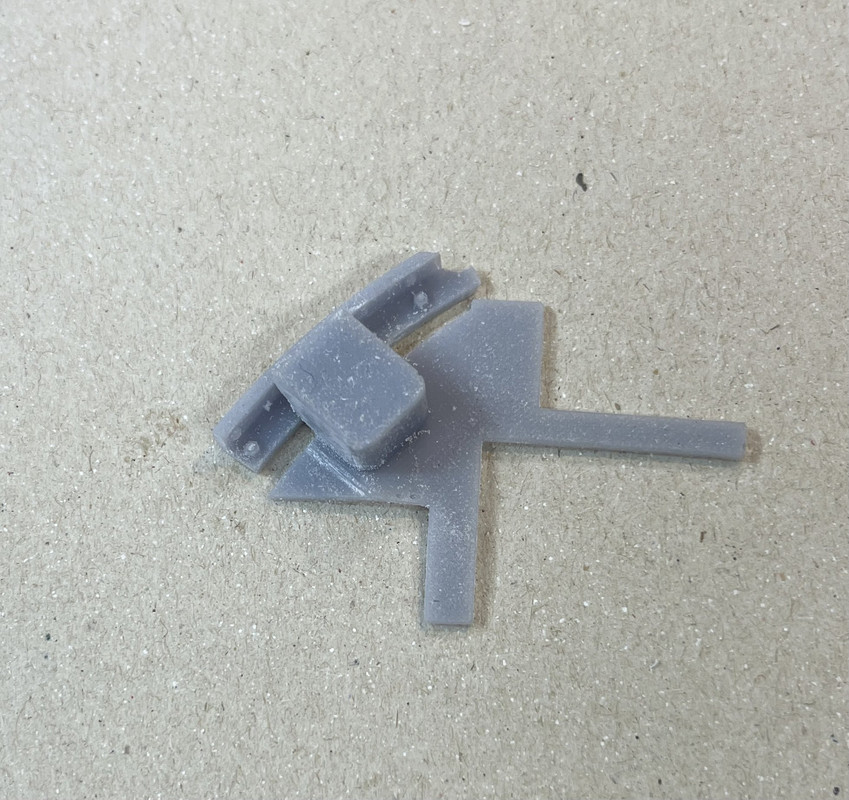
Here's where they fit nesltled into the rear curved wall.
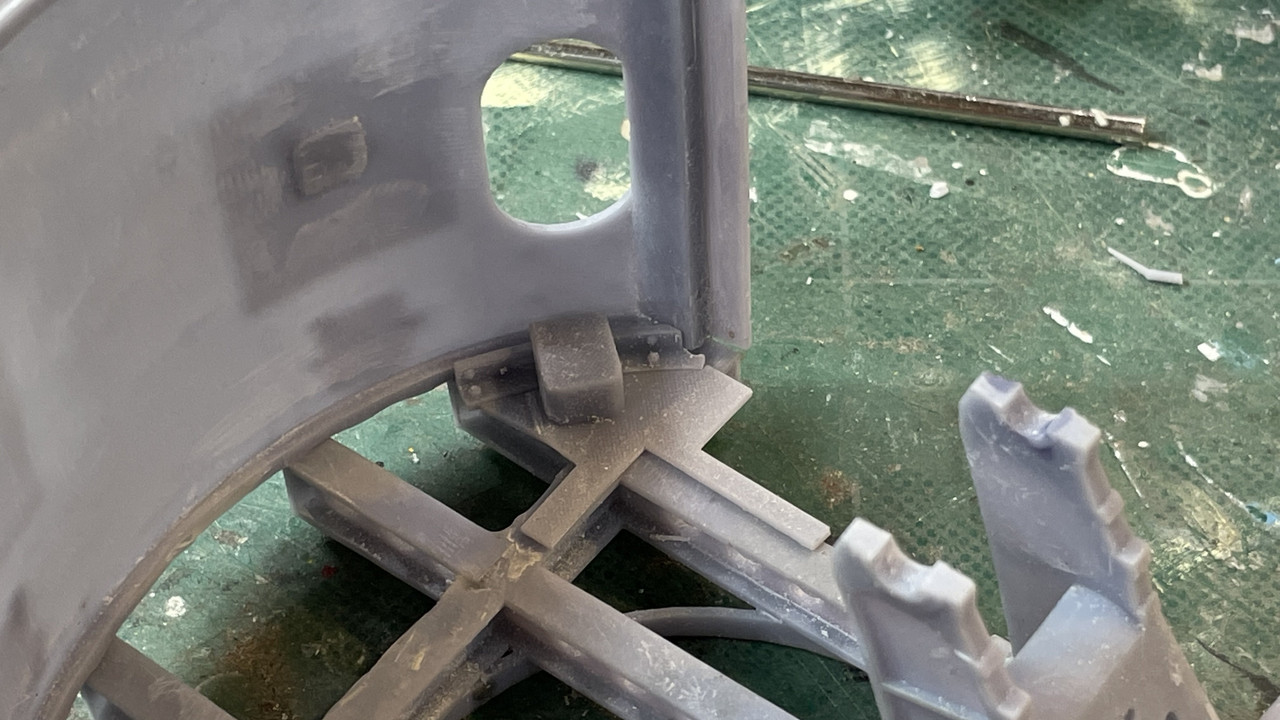
I assembled the floor pieces on the frame for fit and understnading the assembly process.
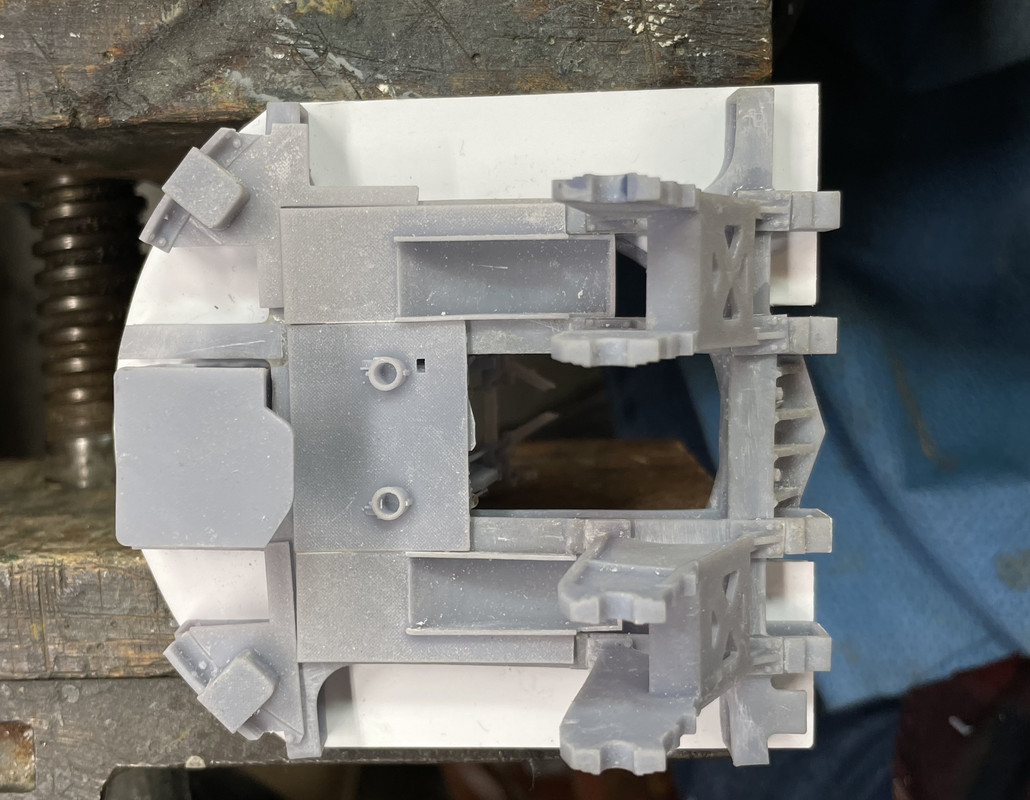
I'm going to post this now, and then re-open and finish. This site has the habit of exhibiting terrible lag time in typing.
I'm back...
With the base plate in I'm able to test fit and locate all the gun house details starting with the elevation and training pump systems. The training pump was easy since it just has to nestle up against the piping I printed that come out of the b-end hydraulic motor. I marked the base, but when this is painted, those will disappear so I'll probably go back and make some punch marks.
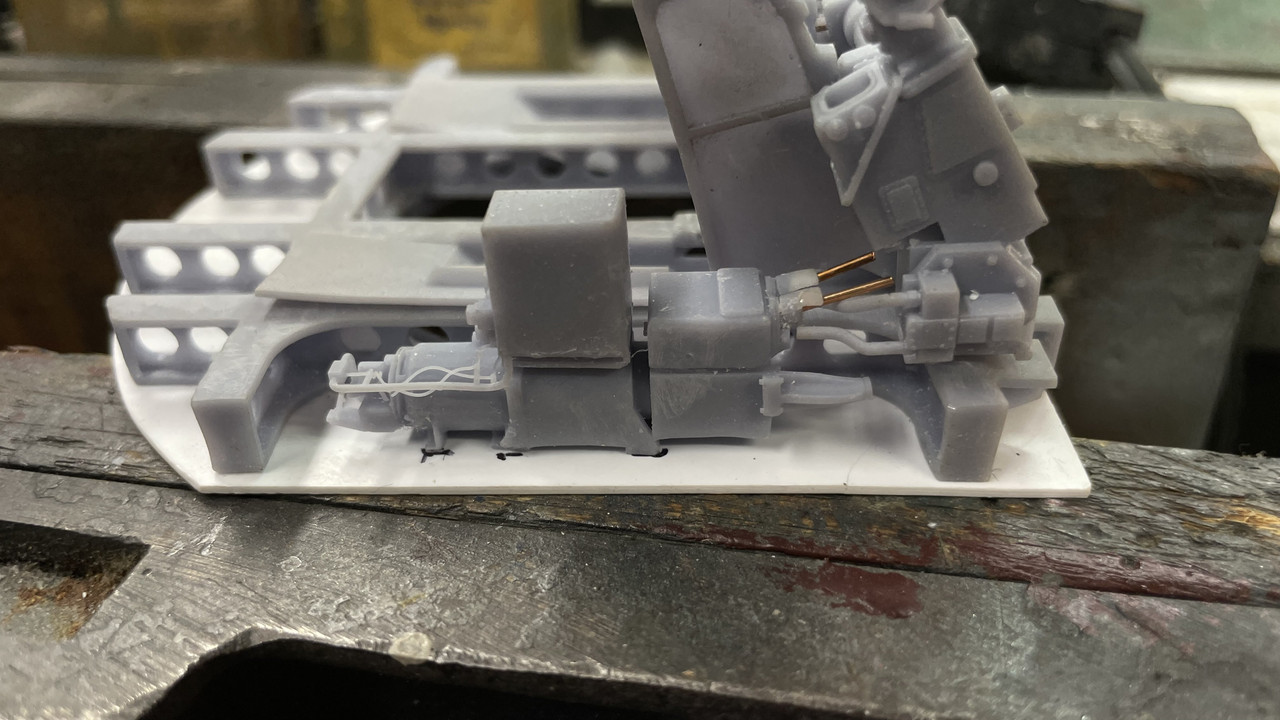
I then test fit the small, diamond-plated flooring pieces.
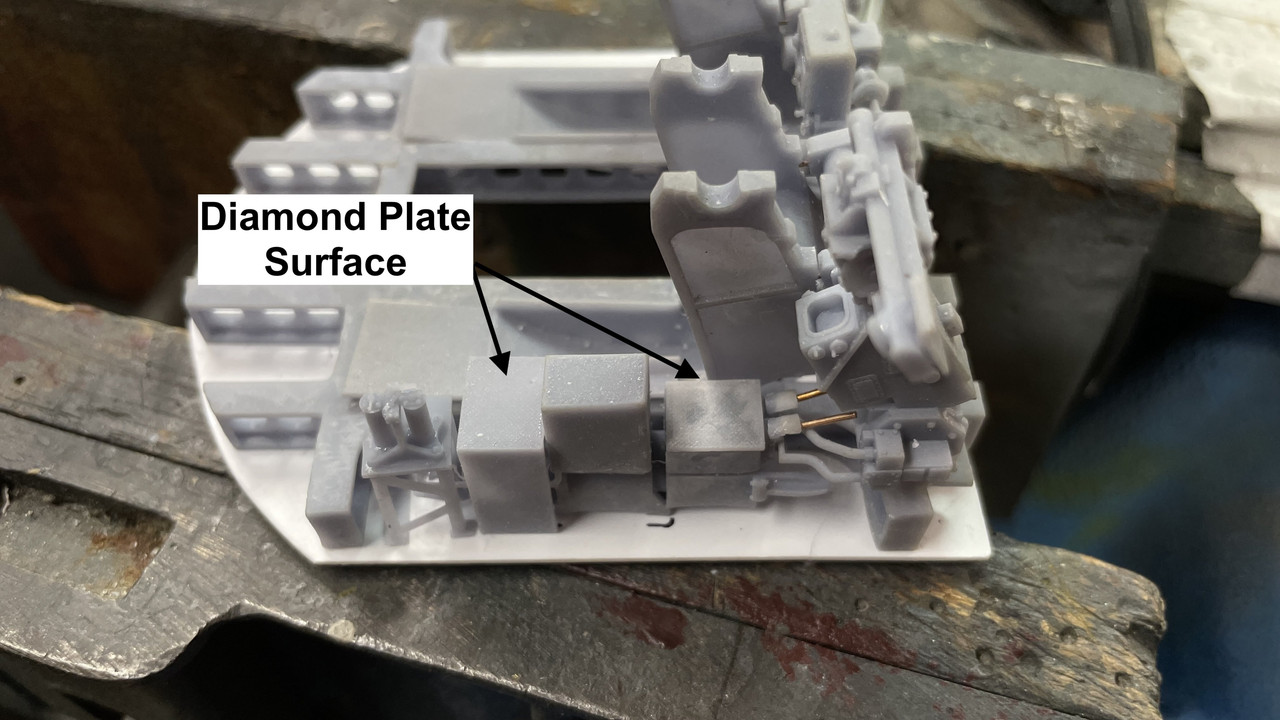
I did the same for the pointer's side. This was a bit more complicated since the spacing is fixed by the very small floor piece that spans between the pointer regulator, where it sits on a built-in ledge, and the a-end of the pump system. I had to add a small piece of angle to support the aft end of the floor.
The angle:
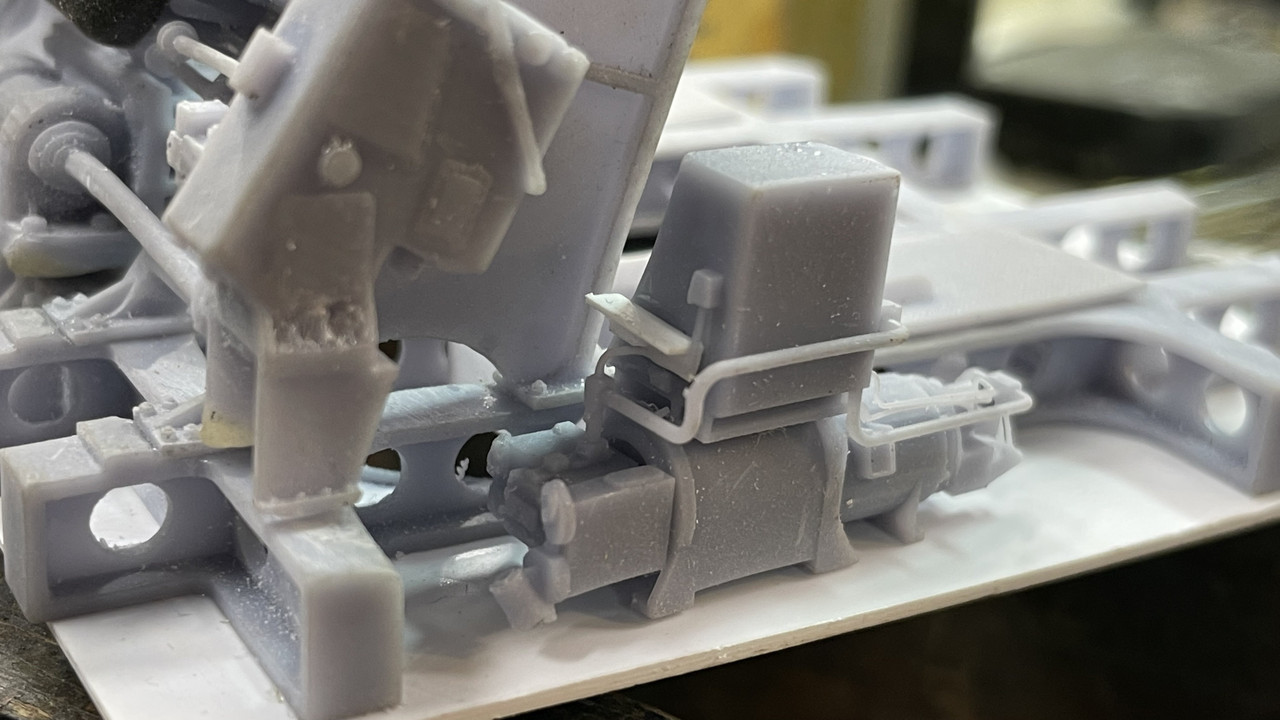
And the floor piece. It was very hard to see just how this little bit of floor was attached in the real thing. Ryan's photos only show it from above and all the drawings don't detail it sufficiently. I had to fake it.
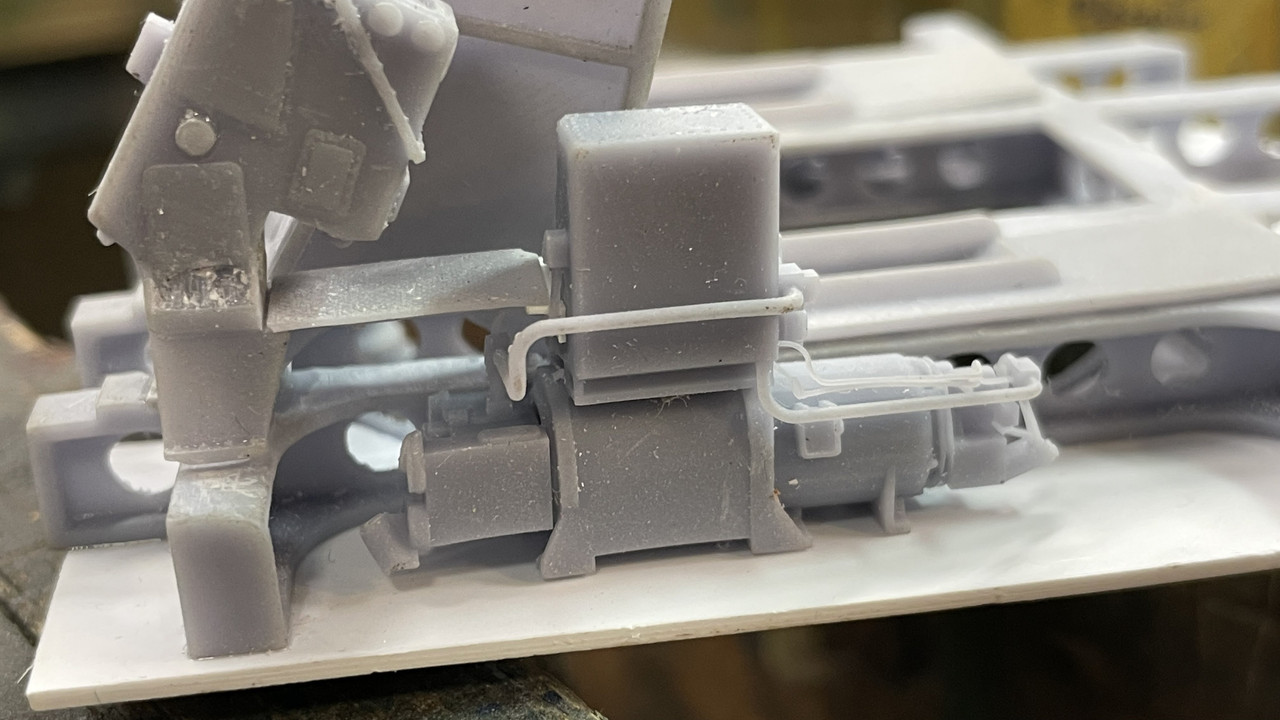
There are hydraulic lines eminating from the a-end of the pump which I will probably add old-school with solder wire.
The entire mechanism assembly needed some possible positioning on the gun mounts. i chose to use 0.022" phos-bronze wire. I broke way too many carbide drills doing this.
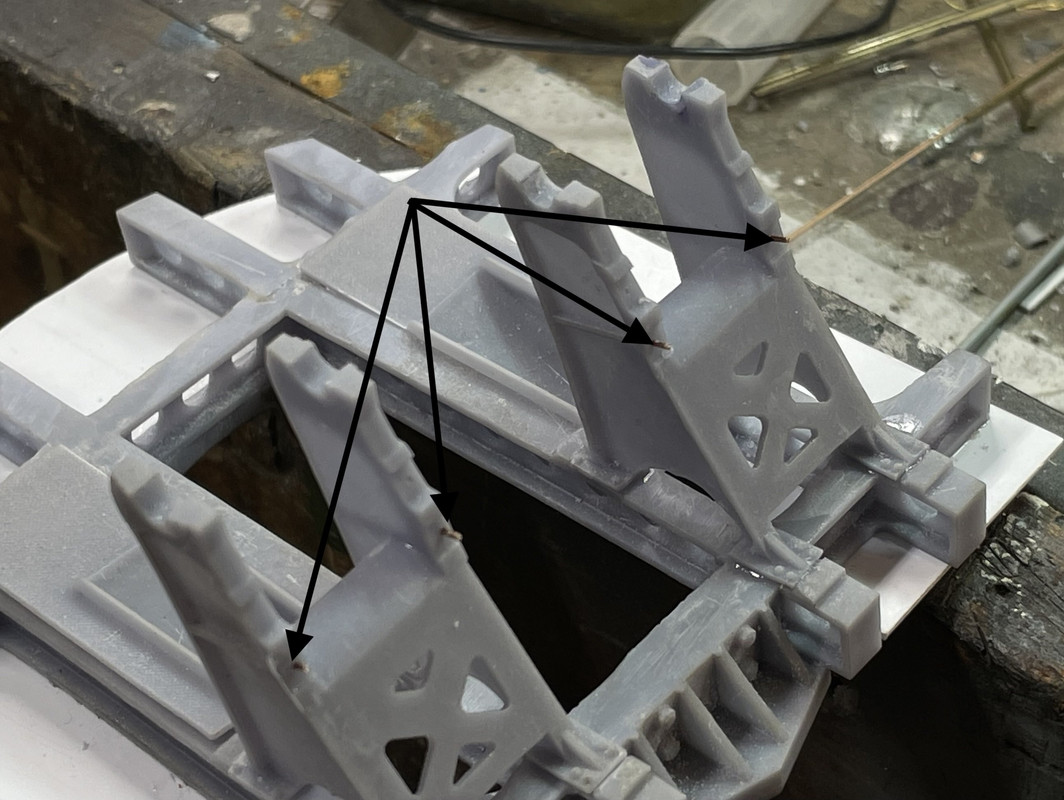
It took some trial and error to get the pin holes in the two pieces so they'd line up. I then drilled and pinned the mounting for the fuze setting regulator. This simple job almost went completely south. I kept breaking the 0.03 2" drills doing this simple operation. I ended up having to drill three diffferent holes to get one without a piece of broken carbide in it.
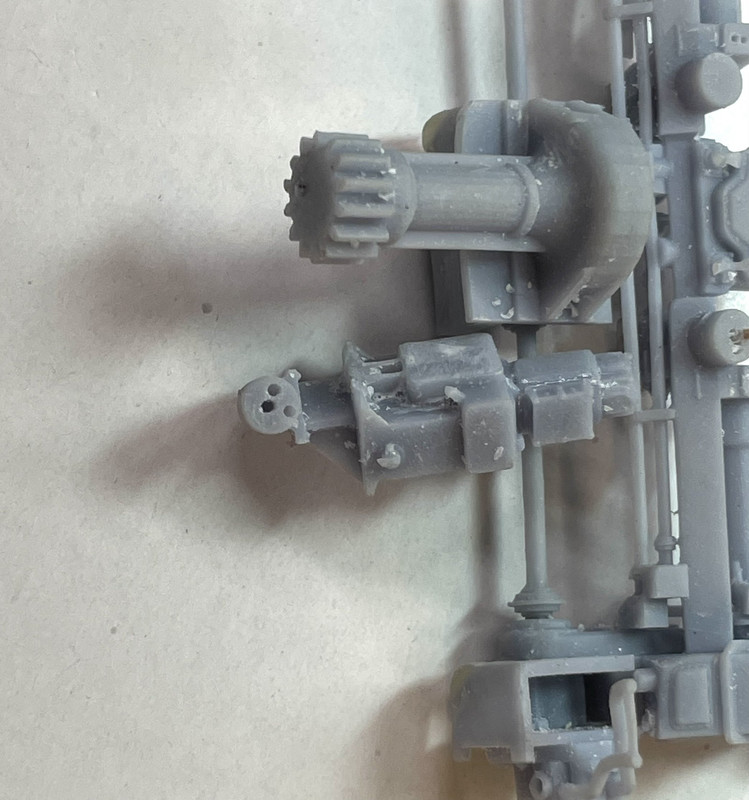
Fitted, but not glued. This will be glued after the gun trunnion cap is installed on that side.
I drew and printed the sight checker's telescope. This station is only used during trainining exercises to evaluate the trainer and pointer proficiency. I made a lug on the mounting point that serves as a trunnion pin on that side. This solved a problem for me.

While there's a just a couple of details left to do for the gun house, I'm starting on the upper handling room. I first tried to fit the entire wall structure as a single part, but as you can see, the setup on the printer was not ideal. Way too many supports for my liking.
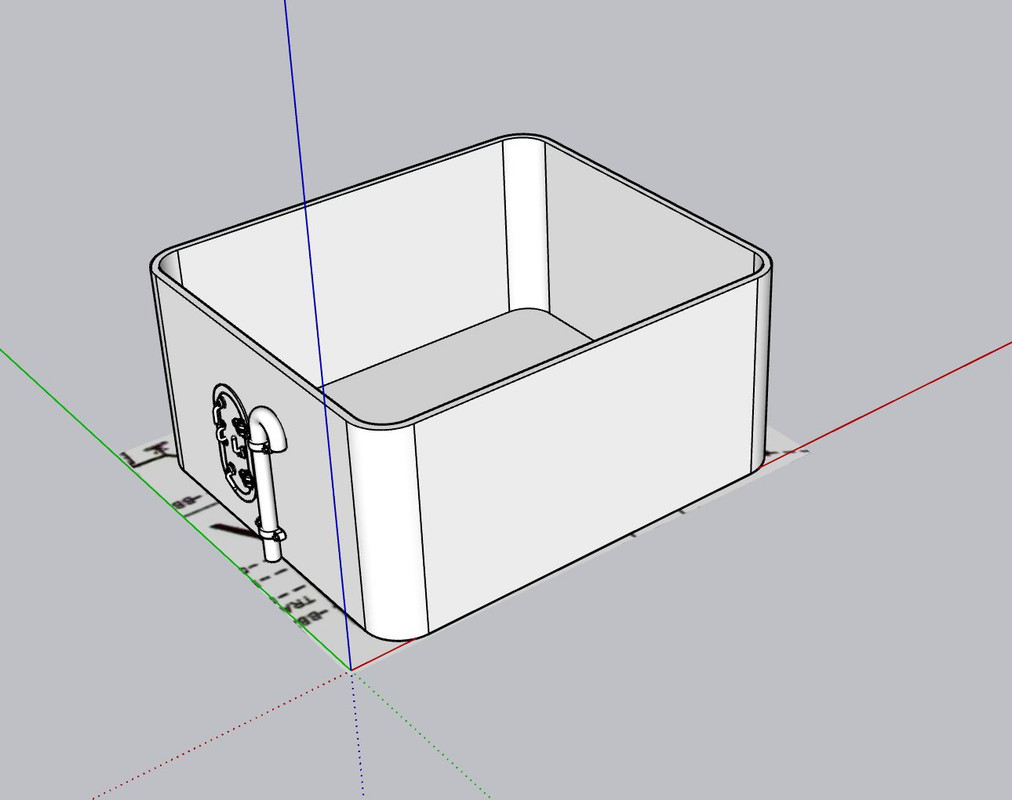
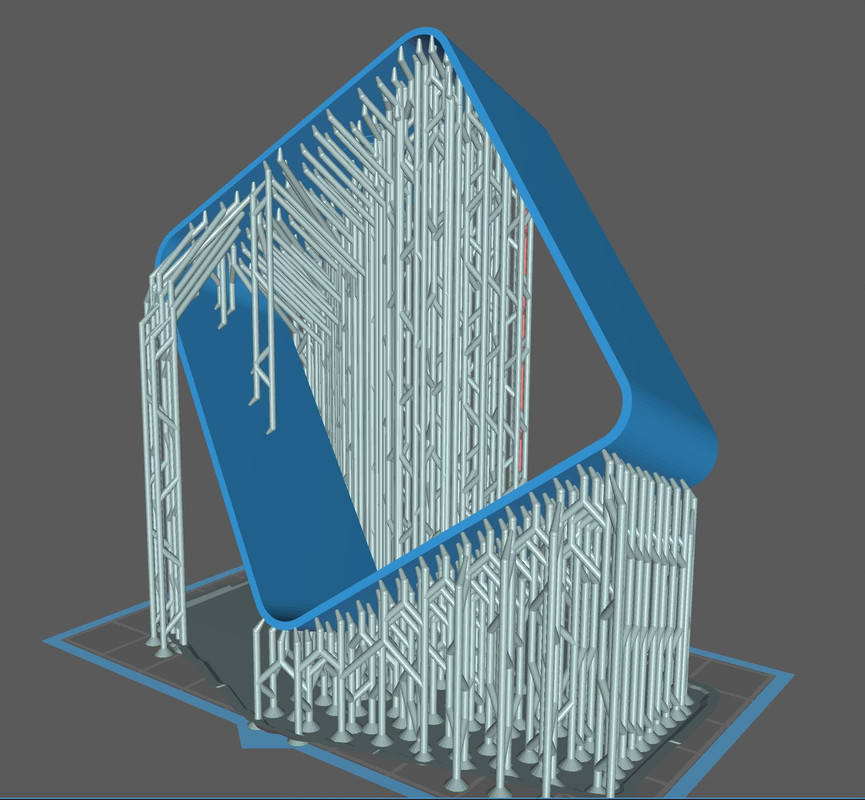
I have a friend with a bigger printer and talked to him about it, but I don't have his printer model available on my slicer. So I went to plan B. Separte the four wall maintaining the nice curved corners. It's those corners that dissuaded me from doing it out of styrene sheet. This permits me to leave on wall open if that's the way I want to approch the cutaway. I did this same scheme when producing the little n-gauge buildings for the exhibition layout. They're printing now and will finish in a couple of hours. Notice, no supports on cosmetic surfaces. Just the way I like it.
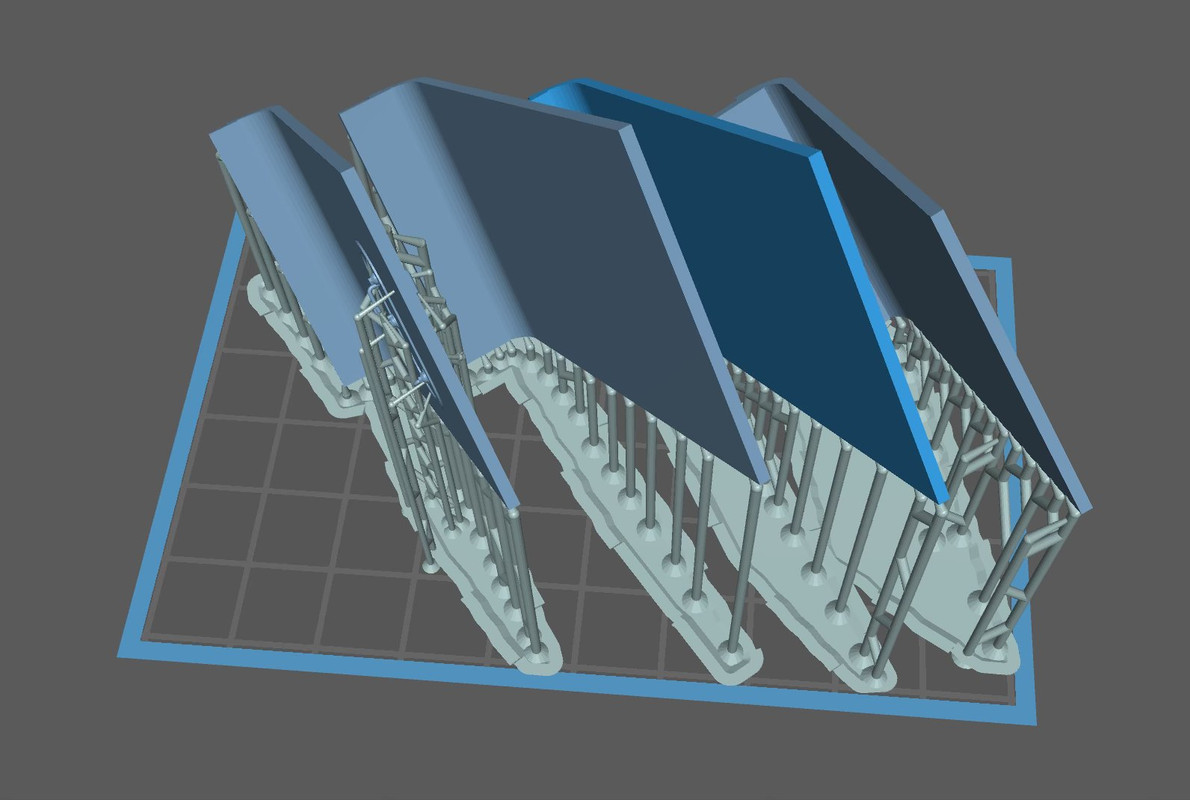
Happy to report that the print came out perfect, including the replacement bicycle seat assembly. It's in the ultrasonice cleaner now, and I'll finish them up tomorrow.