|
Posted by gleason
on Friday, July 22, 2005 11:28 PM
I am looking tusing Jewelry Cord that you can find in the bead making section of HobbyLobby. It is 1.4mm and with two strands, it should make for a nice anchor rope.
<Gleason>
Originally posted by vapochilled
Jtilley, thanks so much for the info and links on the rigging, I'll be ordering from there for sure. However I need to make up an anchor line 2mm Dia, the kit suggests braiding 0.03 line into a rope, I looked at the hand winding contraptions, but it seems a little extreme to me,lol
|
- Member since
May 2003
- From: Greenville, NC
|
Posted by jtilley
on Saturday, July 23, 2005 12:15 AM
Vapochilled - Braiding (if the word is to be taken literally) the anchor hawsers or any other piece of ship model rigging would be utterly ridiculous. With the exceptions of ornamental ropework, I can't think of a single instance of real eighteenth-century line being braided. It was twisted.
Somewhere along the line every builder of a big sailing ship model has to decide how interested he or she is in accuracy when it comes to rigging. In the case of a ship like the Victory, just about the only way to reproduce the rigging line with real accuracy is to make at least some of it yourself. There are two reasons for that. One - the rope on board the real ship is in a huge variety of sizes - considerably more than any manufacturer offers. Two - most of the standing rigging of an eighteenth-century British warship was cable-laid, whereas virtually all commercially available thread is hawser-laid.
The difference is obvious in a picture, but a little tricky to explain verbally. Imagine a drawing of a piece of rope, running vertically. The individual strands of the rope show up as diagonal lines. If those lines run upward to the right, the rope is hawser-laid. If they run upward to the left, it's cable-laid. (There's a third possibility: the lower shrouds generally were shroud-laid. Shroud-laid rope looks like cable-laid rope, but has four strands instead of three. That distinction isn't terribly relevant to model builders.)
Building a "rope-making machine" isn't as hard as it may sound; it can be done in an evening using gears, shafts, and bearings from a Lego set. But the act of making the rope does add a good deal to the time it takes to build the model - especially a model like this one. (The individual strands making up the main topgallant backstays probably would have to be about fifteen feet long, twisted into lengths of four or five feet.)
I don't blame anybody who thinks making his or her own rope is, as you put it, a little extreme - especially on your first attempt at a sailing ship model. If you use commercially-available thread, few people are likely to notice the difference. To those who are in the early stages of their models, I'd suggest putting off the decision till quite a bit later.
In the mean time, if your immediate concern is the anchor hawsers - they really don't pose much of a problem because they're so short. (I imagine six inches would be plenty.) You probably can make good-looking rope for them simply by twisting three strands of thinner thread together and putting a drop of white glue on each end. The strands will try to untwist (that's the inherent complication of rope-making), but if you soak them in water overnight and clamp each end while they dry I suspect they'll hold their shape.
Youth, talent, hard work, and enthusiasm are no match for old age and treachery.
|
- Member since
November 2005
|
Posted by Anonymous
on Saturday, July 23, 2005 12:35 AM
You have a habit of making it all sound so easy,lol
After I posted, I was looking more at the ship references I have and the model, given it's size and the fact that I am looking at possibly over a years build anyway, the added benefit of having correct rigging outways the cost in time(which of course in a hobby is free!)
The reason I need the anchor done sone(ish) is that as you know it runs between decks, so once I've got the hull painted and the second deck goes in, I won't be able to thread this rope.
I did find some reference sites on rope making. and indeed I do understand the difference you are talking of, but I suspect that very...VERY few people in this world could look at a model ship line and say"hang on a minute, that's laying the wrong way!" Just as very few people know which way to coil a rope!
I'm starting to be of the opinion that the plastic parts are just there to hang the rigging from! which is the actual challenge? I think we know the answer to this one. Yes it's some way off before the lines go on, but rather than panic at that time, if I try to get prepared now, it may just not come as such an overwhelming experiance?
|
- Member since
November 2005
|
Posted by Anonymous
on Saturday, July 23, 2005 11:36 AM
Well, I was up until 4am trying to figure out this rope business. I tryed my first one.
3 lots of 3 strands, each yarn wound right then the the 3 yarns wound together left. Not as pretty as using a ropewalk,(I could have done with about 4 extra hands,lol)
But not too bad for a first attempt.
Oh and thanks for the water tip! worked a treat JT
|
- Member since
November 2005
|
Posted by Anonymous
on Friday, July 29, 2005 12:21 AM
Trowlfaz, the rotring pen idea seems to have some merit!
After the enamal yellow had dried, I loaded up the pen with diluted Tamiya acrylic, and started playing. While I', not thrilled with the flat/no flat acrylic!! it does seem to be working, Once it's all cured for a week or so, I'll build up 2 or 3 thin layers of dullcoat and see how it looks.
Quite a lot of work to do, but you can see the basic idea of the pen is actually working, nice idea trowlfaz
|
- Member since
November 2005
|
Posted by Anonymous
on Saturday, July 30, 2005 2:24 PM
Vapo-I occasionally have ideas-but only occasionally. Get that shoulder shake going!
|
- Member since
November 2005
|
Posted by Anonymous
on Tuesday, August 23, 2005 6:11 PM
Well I have now stripped the stern end twice, as I was unhappy with the results, going to be looking at that again this weekend.
I had the bright idea of looking at the mast assemblies today, boy what a lesson in frustration they are! So much filler and sanding to be done.
Can I get 1/100th scale yard arms? the plastic ones, well even the mast tops are so flimsy that I can see a real "pita" brewing once I start rigging?
|
- Member since
May 2003
- From: Greenville, NC
|
Posted by jtilley
on Tuesday, August 23, 2005 10:24 PM
Ship model fitting companies don't make replacement yards with all the fittings attached. They do offer tapered birch dowels in various lengths and diameters; you might be lucky enough to find some in sizes that match. But the final shaping and the addition of the fittings would be up to you. It probably would be virtually as easy to start from scratch.
A yard on an eighteenth-century warship is more complicated than it looks. (Incidentally, the word yardarm refers to the outermost section of the yard - the part from the shoulder to the tip. The shoulder is the "step" near the end of the yard, where the earring of the sail is attached. Each yard has two yardarms - one at each end.) The center section of the yard is octagonal; the taper from that section to the ends is governed by rules. That sort of thing sounds pedantic, but nothing wrecks the appearance of this kind of model like a set of badly-proportioned spars. A yard also has a number of fittings attached to it (though not as many, or as complex, as a late-nineteenth-century yard).
As I remember (I don't have the kit in front of me), Heller got almost all that stuff right. The only criticism of the yards that I can recall making when I reviewed the kit (that was a long time ago; beware my senile memory) was that the representations of the studdingsail boom irons were sort of crude. If I were building the kit, my inclination would be to keep the plastic spars (with the possible exceptions of the very skinniest ones) and make new studdingsail boom irons from pieces of wire and brass tubing, soldered together.
I wasn't impressed with the design of the lower mastheads - the pieces that plug into the lower masts, supposedly after they (the mastheads) have had the shrouds rigged around them. That's part of Heller's ridiculous solution to the Great Ratline Problem. Each lower mast ought to be one solid unit.
I can't imagine that the plastic tops would give any trouble; they're plenty thick enough, and a lot of rigging supports them. Ditto for the lower masts and yards. I suspect the topmasts and topsail yards are hefty enough to handle the strain too. For the topgallant yards and topgallant masts, your options really are to use the kit parts or build replacements from scratch.
If I remember correctly, the lower masts and yards are hollow. (Maybe the topmasts and topsail yards are too; I don't remember for sure.) You might try gluing pieces of wood or piano wire inside to provide some stiffening, but I don't really think it's necessary. This is a large-scale model., and those plastic parts are pretty stiff. Most species of wood, turned down to the diameters of those topgallant masts and yards, would be either just as springy as the plastic or (worse) prone to break at the worst moments.
There's no way to avoid the fact that, even on a big model like this, it takes a good deal care and some practice to keep the rigging from pulling the thinner spars out of alignment. If the model is rigged to scale, though, the problem won't be nearly as severe as it may seem at first glance. Rigging isn't an arbitrary collection of ropes; it's a system, carefully designed to resist far greater forces than any that a model will ever encounter. Those old boys knew what they were doing.
Youth, talent, hard work, and enthusiasm are no match for old age and treachery.
|
- Member since
November 2005
|
Posted by Anonymous
on Tuesday, August 23, 2005 11:29 PM
Hi JT, yes , I was thinking that the rigging on this thing will be far from a model, it will be functional!
I had a look at modelexpo, the ones they have will require a great deal of work to get right.
I've glued brass tube into the two lower mast sections, and can do something similar with the yards.
You know, while I greatly appreciate your answers JT, your knowledge is great, I sometimes wish you would'nt answer,lol, You see every time you answer, I find out my question is only half the story. Your answer normally opens a whole other can of worms for me. Far from making the job easy, you force me to learn yet more and more with each answer
I fear my brain is going to explode before the end of this kit
You've built several of these beasts, and from your answer, am I to understand that I can't assemble the masts, fit them , then do the rigging? that was my plan, as it would make the job of putting them in easier(I thought), your asnwer suggests that I must install each mast section in stages as per the real thing, doing the rigging as I work up the mast?
|
- Member since
November 2005
|
Posted by Anonymous
on Tuesday, August 23, 2005 11:51 PM
The wife is now officialy starting to get worried!
She's just seen me putting the masts together to check how they fit etc.
Her response was "where on earth do you intend putting it once it's done?"
That's a 12" rule being dwarfed by the lower section of the mast
|
- Member since
November 2005
|
Posted by Anonymous
on Tuesday, August 23, 2005 11:57 PM
JT, excuse my ignorance, but is this the masthead? If so, then I'm not happy with it either! they will require a great deal of work to get them looking good, let alone any problems with rigging.
|
- Member since
December 2003
- From: 37deg 40.13' N 95deg 29.10'W
|
Posted by scottrc
on Wednesday, August 24, 2005 8:49 AM
I am enjoying your thread ![Big Smile [:D]](/FSM/CS/emoticons/icon_smile_big.gif) You seem to realize what a lot of scale modelers find out when tackling a plastic sailing ship, that in order to satisfy the requirements of looking as authentic as possible, the kit becomes a multi-media project.
In regards to paints for instance, I use all types of medias; enamels, acrylics, tempura, and oils to get the best results. Don't rule out any medium, because they all have their purpose.
Also, as you found out, we apply these medias with different techniques. I for one use the technical pen a lot. I also use India Ink for deck and side washes. I like oils for painting gilding and also as a wash, since oil seems to give depth and a patina that real wood represents. Pastels also are a must for shading and blending and light weathering. You find yourself more of an artist painting a 3 dimensional picture than a plastic model builder.
In regards to the masts and spars. I have built several Heller sailing ships, and have learned that the some of the kit masts, yards, and spars are only good for stirring paint and to use as patterns to make better ones out of wood, round styrene, and brass tube.
Same goes with any hardware Heller provides such as blocks and tackles. Most are too big, or are molded poorly that inhibit them to function properly. RTV and resin has become my best friend in being able to make a pattern, then a mold, and make a couple dozen resin fittings.
Building the masts in stages is the more sane approach. I tried eating the whole elephant by building the entire foremast and ended up in pure frustration when trying to install the stays, braces, footropes, futtocks, and reefers. The best solution is to build and rig each step before installing it on the model, with exception to the lower mains which are installed in the base of the hull, that way you have room to test and re-rig if possible each line in the segment and iron our any issues before finding them when the masts are secured on the model.
I hope you enjoy your build, I think it's looking fantastic so far, don't let it get to complicated though, for there are always more models to build in the future.
Scott
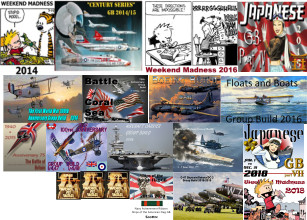
|
- Member since
May 2003
- From: Greenville, NC
|
Posted by jtilley
on Wednesday, August 24, 2005 12:11 PM
There are no "rules" about how to rig a ship model. In the case of the real thing, the near-invariable practice was to step the lower masts, rig them, use them as the mechanism for hoisting the topmasts, rig the topmasts, use them to hoist the topgallant masts, etc. That was about the only way to do it without inviting the masts to fall over.
Lots of modelers do it the same way - not because of strength considerations, but simply because setting things up in that order keeps things from being in the way. It's easier to rig the shrouds of the lower mast before the topmast is in position. That sequence also makes it less likely that anything will get broken.
It's entirely practicable to rig the model in stages like that. The whole network of spars and rigging is, in fact, designed for that purpose. If you set up the rigging of the lower mast and find that you can't fit the topmast into position, you've done something seriously wrong. On the prototype ship, it has to be possible to unship the topmast without disturbing the lower mast.
Many modelers set up the lower masts, then the topmasts, then the topgallant masts, and then move on to the yards. I like to rig the fore lower mast, then the fore yard, then the main lower mast, then the main yard, then the mizzen lower mast, then the crojack yard, then the fore topmast, then the fore topsail yard - etc. That system adds some variety to the job. It's all up to the individual modeler.
The object in your photo is indeed one of the lower mastheads. I imagine the brown paint on it is either a primer or a trick of lighting in the photo; the masthead, along with the top, the trestletrees, the cap, and the hounds, should of course be black.
Scottrc's comments about plastic spars probably are more applicable to smaller kits. As I said in my last post, the larger spars in the Heller kit probably are strong enough - though the smallest ones might benefit from replacement. I agree completely with scottrc's comments on the kit-supplied blocks and deadeyes. Heller made a gallant attempt at them, but was thwarted by the inherent characteristics of the injection molding process. One-piece injection-molded blocks and deadeyes, by definition, just don't work. A two-piece rigid mold physically cannot produce an object with a hole in it and a groove around it.
Wood replacement blocks and deadeyes are available from a variety of sources. My own personal preference, though, is the line of Britannia metal fittings from Bluejacket Shipcrafters ( www.bluejacketinc.com ). They aren't cheap (a full outfit of blocks and deadeyes for a 1/96 Victory might well cost more than the Heller kit did), but to my eye they're the most authentic-looking fittings available.
Youth, talent, hard work, and enthusiasm are no match for old age and treachery.
|
- Member since
November 2005
|
Posted by Anonymous
on Wednesday, August 24, 2005 7:43 PM
Actually, the mastheads are that colour out of the box, it's the nastiest plastic I've ever worked with. Very brittle.
The two halves did not go well together, so the grey you see, is me starting to build up the join lines, ready to spend happy hours sanding!
|
More great sites from Kalmbach Media
|
|