Not so comfortable when you read this account! Also a pic of the Tank Museum Bovington car
Memories of times spent as a young Lance Corporal (fitter) in a Rolls-Royce armoured car company in India 1929-36
By J R Chapman
All cars were 1911-14 vintage with exception of one named ‘Wedding Bells', which was a 1908 Rolls-Royce.
Armament . One Vickers .303, belt feed, water-cooled, mounted in front face of turret.
Driving position . First and second drivers sat on a cushion on the floor of the car, with supporting back straps. Second drivers' duties included that of being responsible for the air pressure in the petrol tank; in event of mechanical air pump failure he operated the hand air pump.
Lighting . Low-pressure carbide lighting system. Second driver responsible for cleaning carbide container, filling container with fresh carbide and water, pricking of lights, jets, burners holes and serviceability of the lighting system feed hose. As a rule the lighting system worked perfectly when tested in daylight, but became defective as soon as the sun set.
Batteries . Removed from cars and charged in the workshop. No dynamo or starter motor fitted.
Starting . Drivers would complain if the cars would not start by simply turning the switch on top of the steering column to MAG or BATT. All drivers considered the starting handle should only be used for charging the combustion chambers and for maintenance. When priming the combustion chambers, to get a very rich mixture a penny was placed under the control arm which was clamped to the mixture jet. The jet was thus lifted out of its tube by the thickness of the penny, giving the richness required.
The high-speed jet was adjusted on the road at speed. The fitter used to lie on the front mudguard with legs on running board and lash himself with rope to the armoured body stay. Tools required were hanging from the engine by lengths of string.
Clutch . When required the clutch pedal was depressed and propped out with a piece of wood in order to soak the cone clutch lining with castor oil. The clutch pedal was usually left depressed all night.
Piston Rings . Standard type rings were too small. OS rings had to be ordered from UK.
Brakes . Hand brake shoe linings were of cast iron secured to shoes by copper rivets.
Tyres . Inflated by hand pump.
Steering . The steering geometry, or as much as was known about it in those days, had to be really accurate. If not the car developed the most alarming ‘wobble' and I have known the turret to be thrown off due to such wobble. I have known a slight bump on a dumb iron to cause a steering defect.
Jobs most disliked in workshop:
- When the mass of controls on the bottom of the steering column and on the carburettor and ignition became worn, all holes in the yokes of the joints had to be reamed oversize and new clevis pins made and fitted.
- Dismantling the rear axle. Bolts were so close it was not possible to use an open-jaw spanner. Sockets had not been thought of, the only thing to use was a tubular box spanner, and were those nuts tight? The unfortunate fitter always ended with no skin on his knuckles.
- Having to spend hours adjusting the wheel spokes to true the wheel rim. We had a rig made with a dummy mounting using the wheels own mounting and locking device.
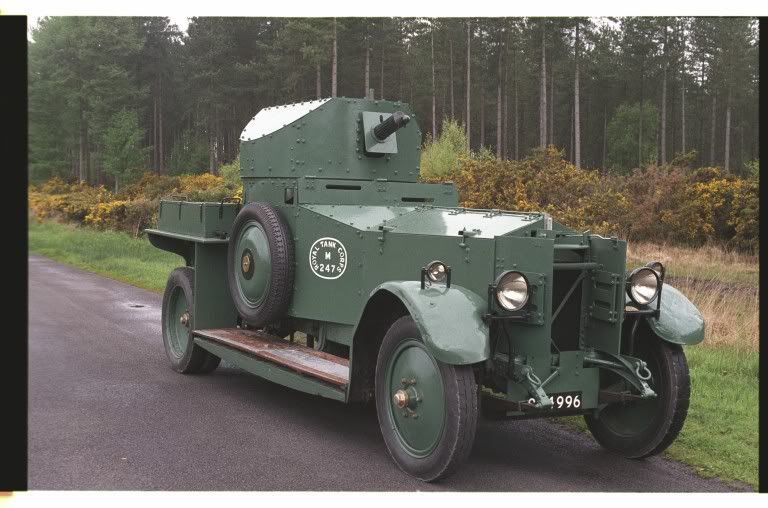