Happy Monday. First of all I want to tell everyone that Louisville was spared any damage from the monster storm that ran through KY. Unlike many, I do not either blame a diety or praise one regarding where a weather front decides to become malevolent or benign. It is almost the pure definition of random. it's that randomness that drives people to want to identify an actor, but there is none. With tornadoes, a house on one side of the street is reduced to molecules and the one on the other side of the street is untouched. Gods have nothing to do with this. What I would want a god to do would be to prevent the storm from happening in the first place.
On Friday afternoon, I listened to a broadcast from one of our local weather forecasters where he was discussing "Athmospheric Caps." I hadn't heard the term, but it was very interesting. It is the high pressure that exists high in the atmosphere that can limit the ability of a storm front to make tall super cells. It results from when low and high pressure areas collide and the high pressure rides up over the low.
It was strong over our area and weak in Western KY. He said depending on how long it hangs around, it could mitigate how strong the storms would be over Louisville. I feel this effect was the main reason the storms broke down as they reached our area. Tornadoes did form about 25 miles south of the city. Meanwhile, my trash totes didn't even move. Others in the Commonwealth did not fare so well and it was horrific in the extreme.
So I am extremely happy that my wife are I are alive and well... that our house is intact, and my workshop is here so I can build this model and write about it to you.
Today began with gluing the interior onto the right hand fuselage side. I used some Quickie clamps to hold it tightly in place. The fit was pretty good so far.
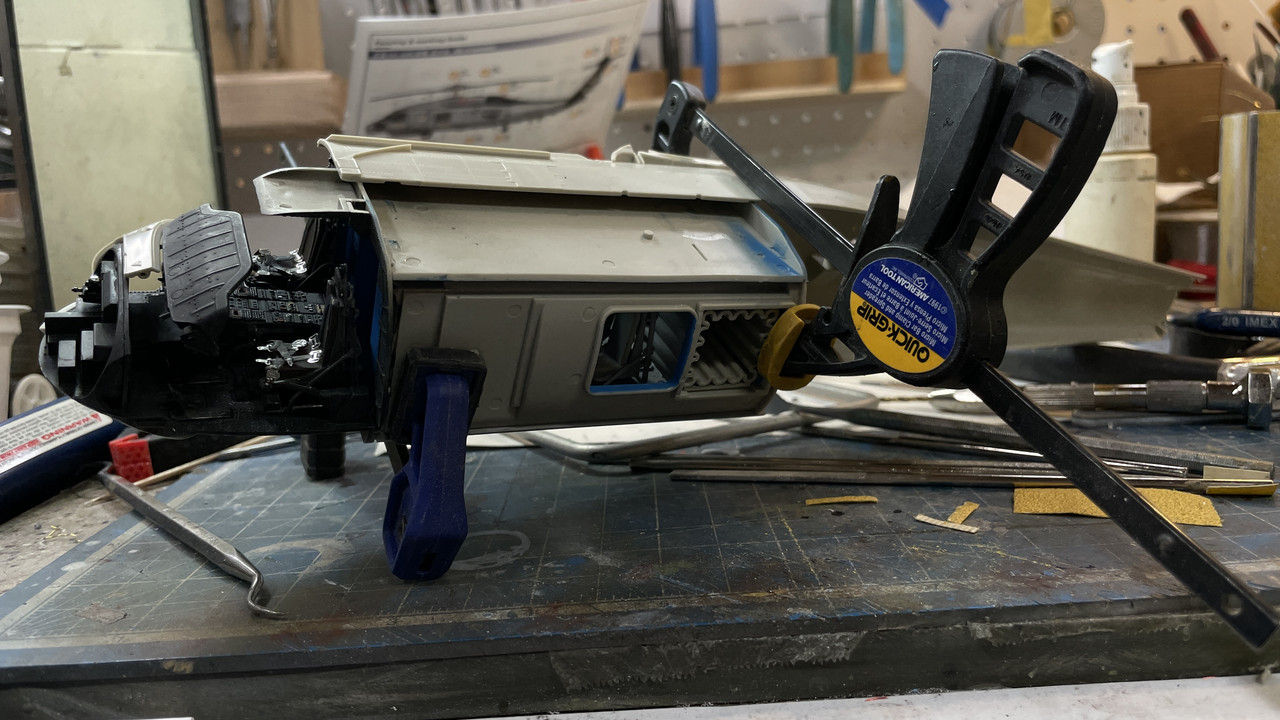
This view shows how nicely the rear of the cabin fit the fuze side. I forgot to put in a piece that lay inside the nose one each side. I had to stick it to a sticky picker and slide it into the narrow space, and glue it. No harm no foul. I did glue it to the other side that wasn't attached.
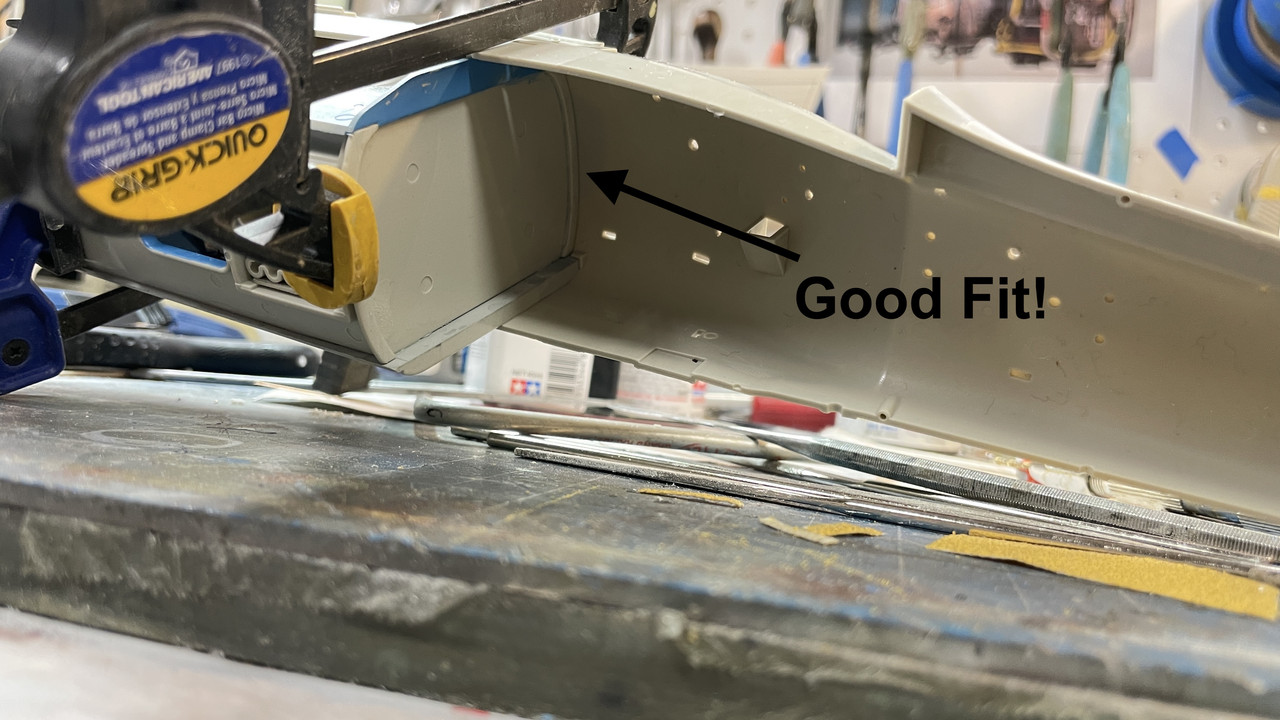
I then attempted to fit the left side in place and was greeted with terrible gaps. If I got the top to fit tightly, the bottom was wide open and vice versa. Two factors were at work. With the cabin being a completely enclosed structure, you can't look and see if it's aligned properly as you could when it was just on one side, and I suspected that the cabin bulkheads were just too wide in spots preventing closer.
Here was the bottom: Notice the bulb in the front. That was an option that I decided after it was all glued in that I didn't want to use it since I wanted the FLIR option on the front end.
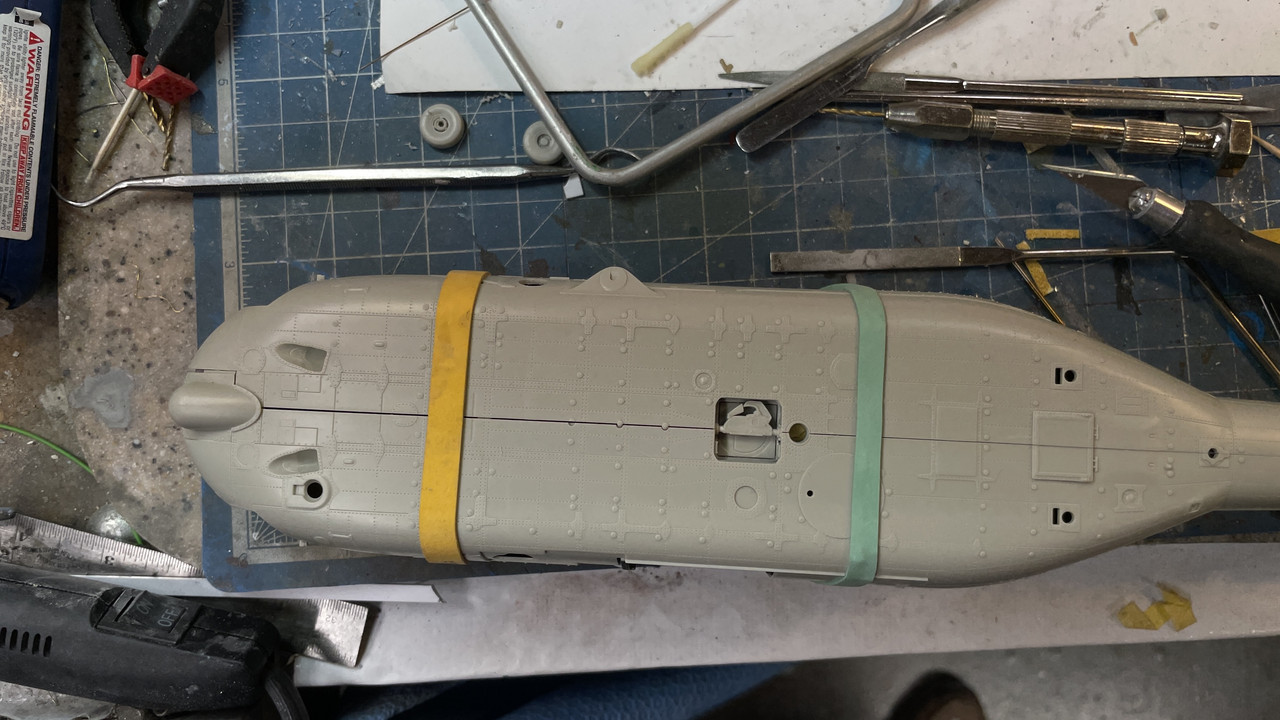
And this was the top! Ugh!
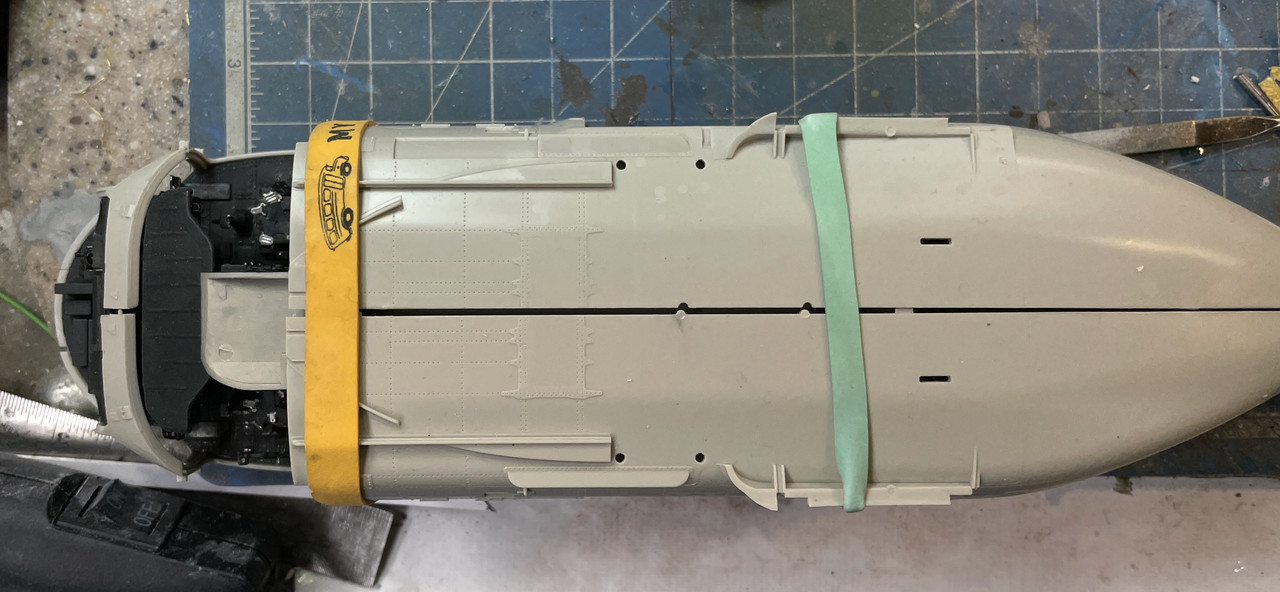
This was totally unacceptable and made for bad fits of the engine housing and the front fairing.
I selectively reduced the outer edges of the bulkheads and kept trying the fit. I finally got it as far as it would go, so it was time to glue. But first, the rear landing gear has to go in because it's trapped by the two fuze halves.
I painted the gear silver only to identiy that it was probably white. I first tried bare metal foil for the oleo strut, but scrapped that and used Molotow chrome brushed on. Meanwhile, the scissors link broke. I glued it together once, and it broke again when I was fussing with the foil. This time I drilled and pinned the scissors joint and glued it again. This time reinforced with thin CA.

But then, disaster struck again during all my manhandling when trying to close those pesky joints. Another piece of the scissors broke in another place and got lost.
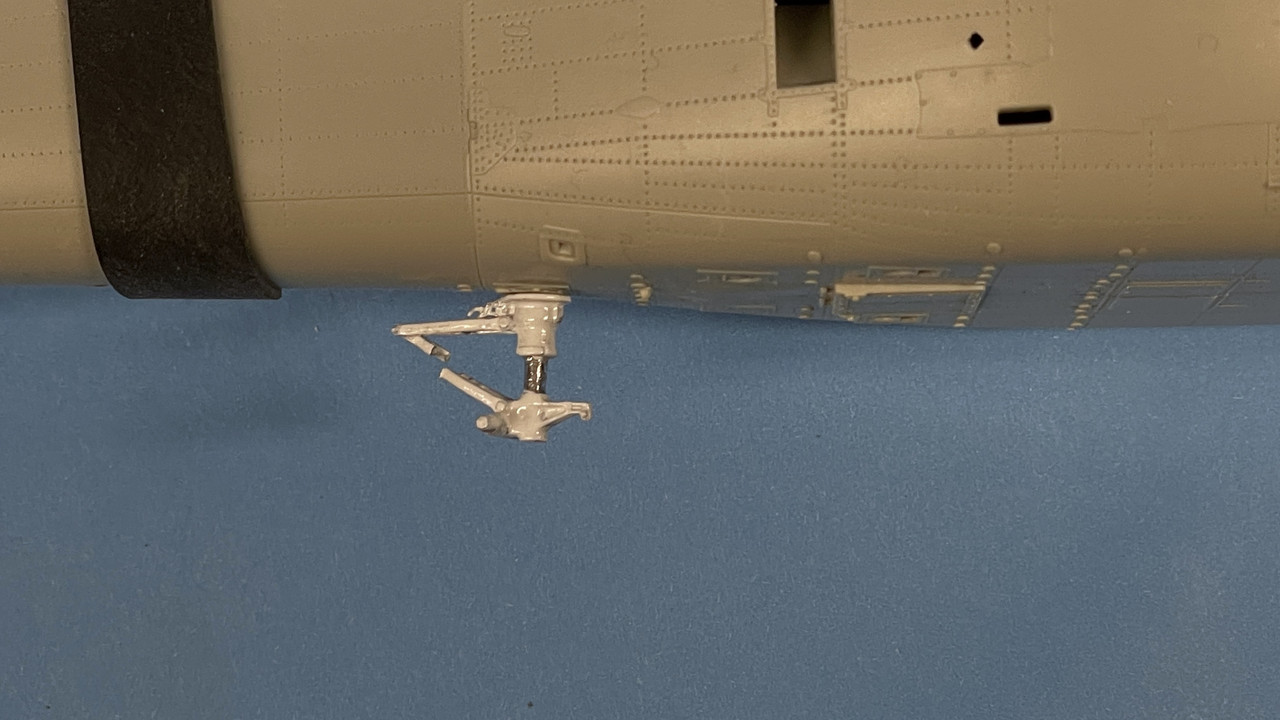
I'll have to scratch-build or 3D print another scissors. Annoying! My UV 3D printing resin is tougher than styrene... or at least the Kitty Hawk styrene.
I changed out that front piece before commencing the fuze gluing. This one has the mount for the FLIR in front.
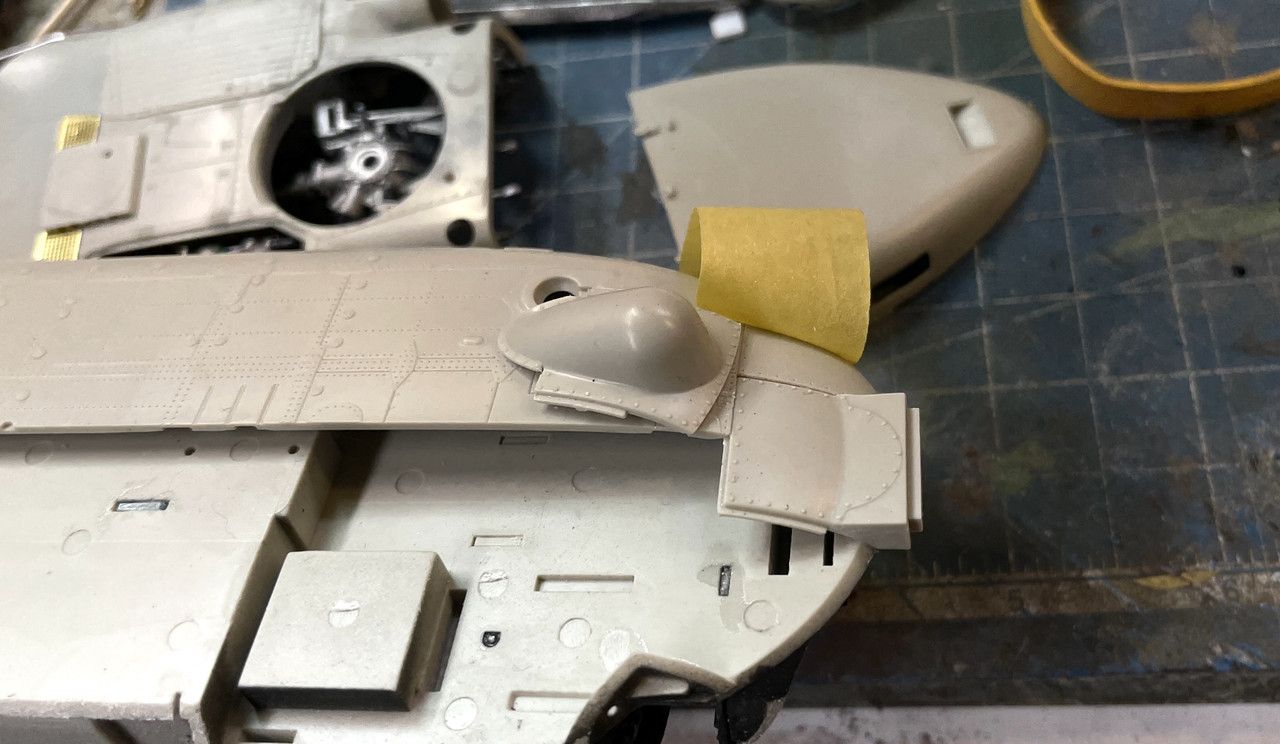
It was time to glue the fuze together trapping the landing gear and the front piece. I worked the bottom joint first since it's exposed more. I let the top joint go for a while. The bottom will get a little filling tomorrow after the joint is fully dry.
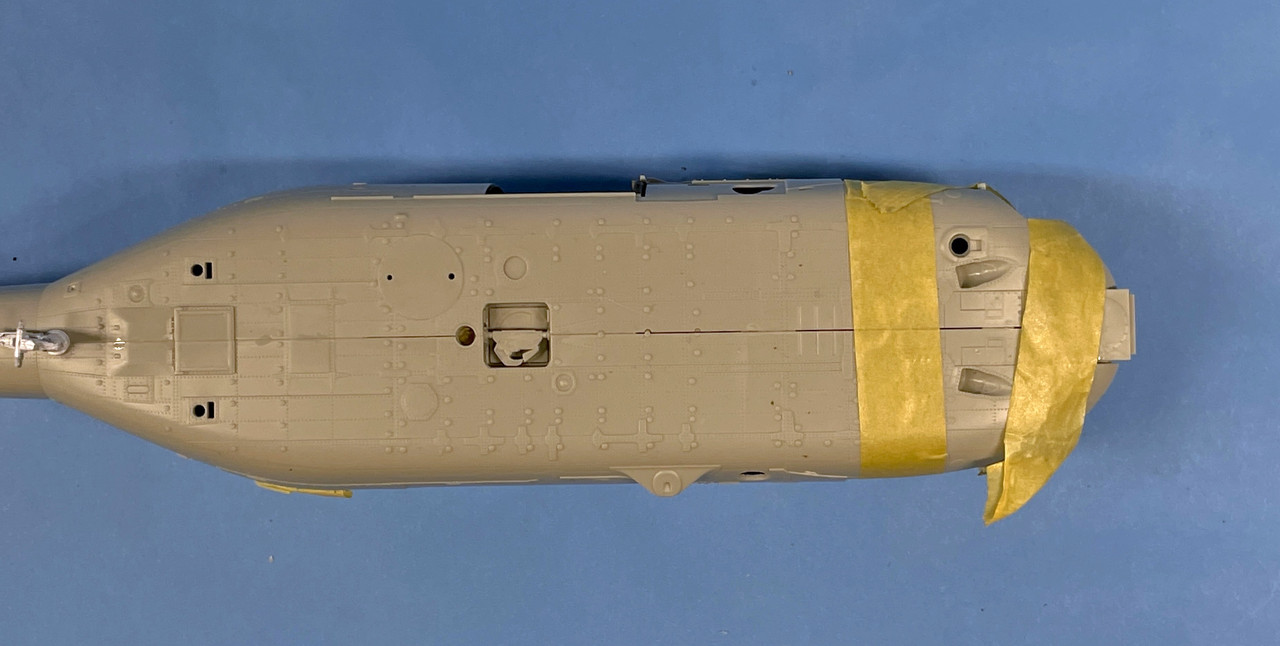
The top joint still ain't so hot, but it's hidden. It could cause fit problems with engine housing, fairing and the front glazing that I'll have to figure out as I go.
I'm going to fill this seam with styrene and then filler.
The tail seam was the best of the bunch and looks pretty good. I apply the liquid cement on the inside in as many areas as I can before wicking it in from the outside.
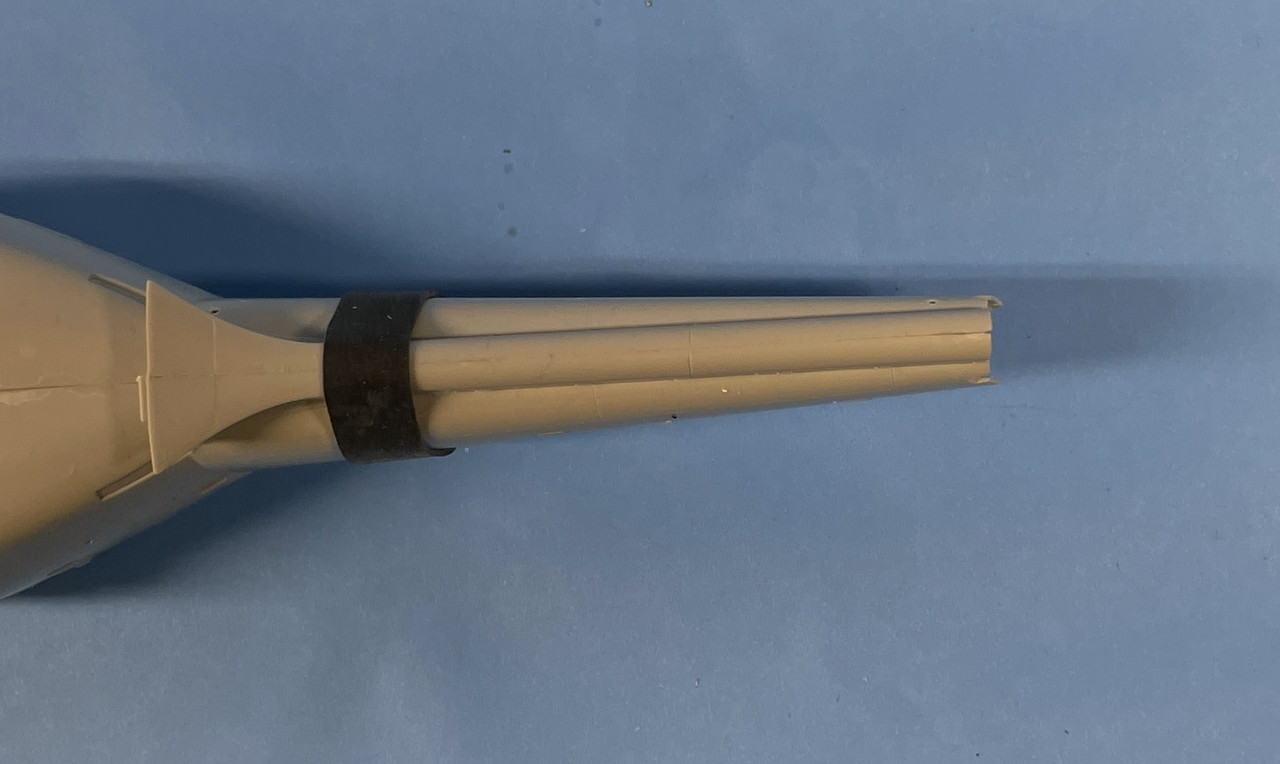
While the paint on the gear was drying I assembled the wheels and made some masks for the hubs. I use a small machinist dividers with one point ground to a sideways chisel edge. I measured the diameter with the digital calipers, divided it in half and used this setting to set the dividers. I added a dab of Molotow Liquid Mask to cover the tiny hole from the dividers' point.
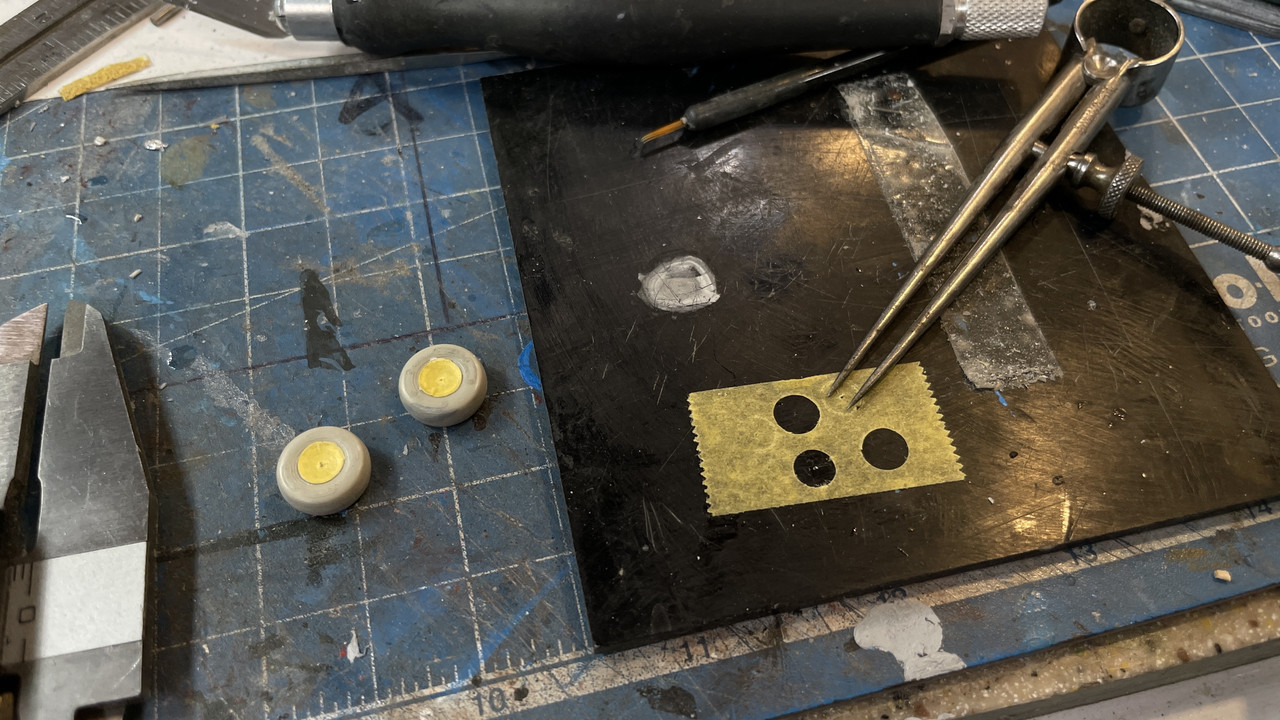
Fuze cleanup will start tomorrow.