And as they say, "just wait, there's more!"
Continued building the interior with the Driver and Asst. Driver's seats. As per Ryefield's M.O., each seat was a complex assembly in itself with multiple little and sometimes ambiguous partrs. Notice that I subsitituted some guitar string with a Bondic end for the tiny, thin plastic seat adjusting lever.
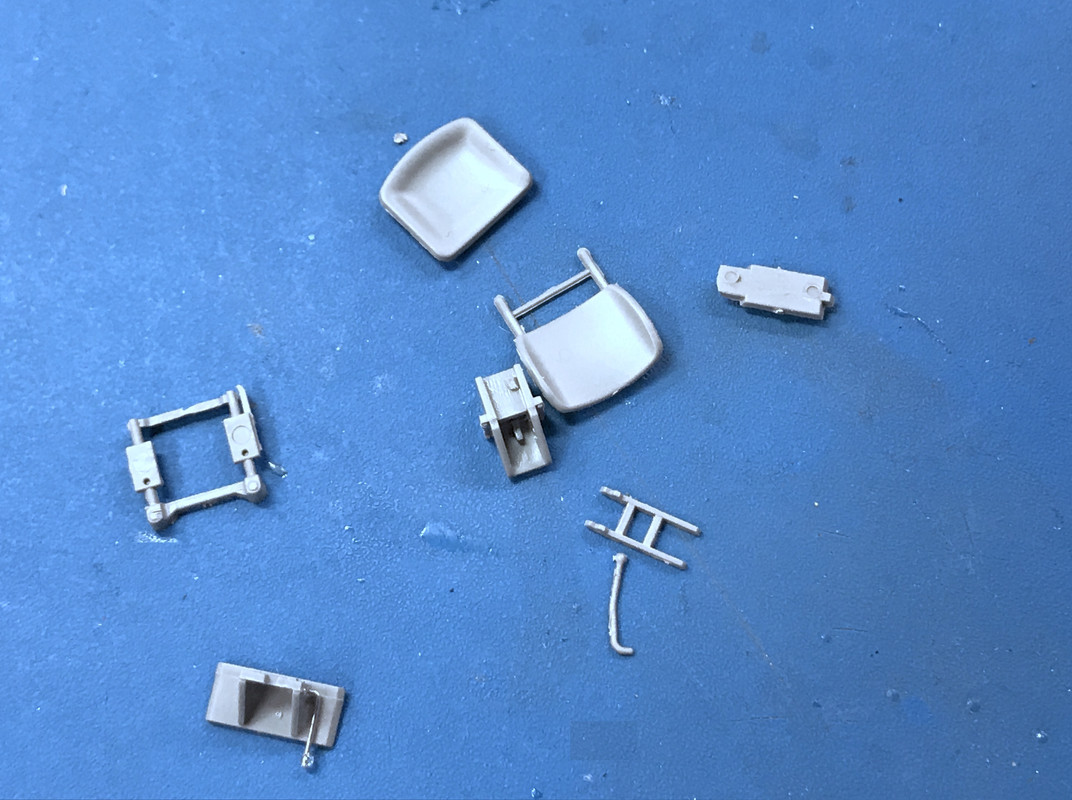
You assemble the parallelogram lift mechanism first which insludes some mock suspension springs molded into the plastic. And then you build the seat and connect the two. I drilled the mounting spots for the seat back to make the hole deeper and more pronounced. Remember when I commented about how small the alignment pins were? Just look at the two on the flat part on the right assembly that are supposed to engage in the two holes on the seat bottom. BTW: I had already opened those holes to ensure the pins find their mark. Gluing the scissor assembly to the base was a real hit-or-miss operation since there was not an apparent alignment guide.
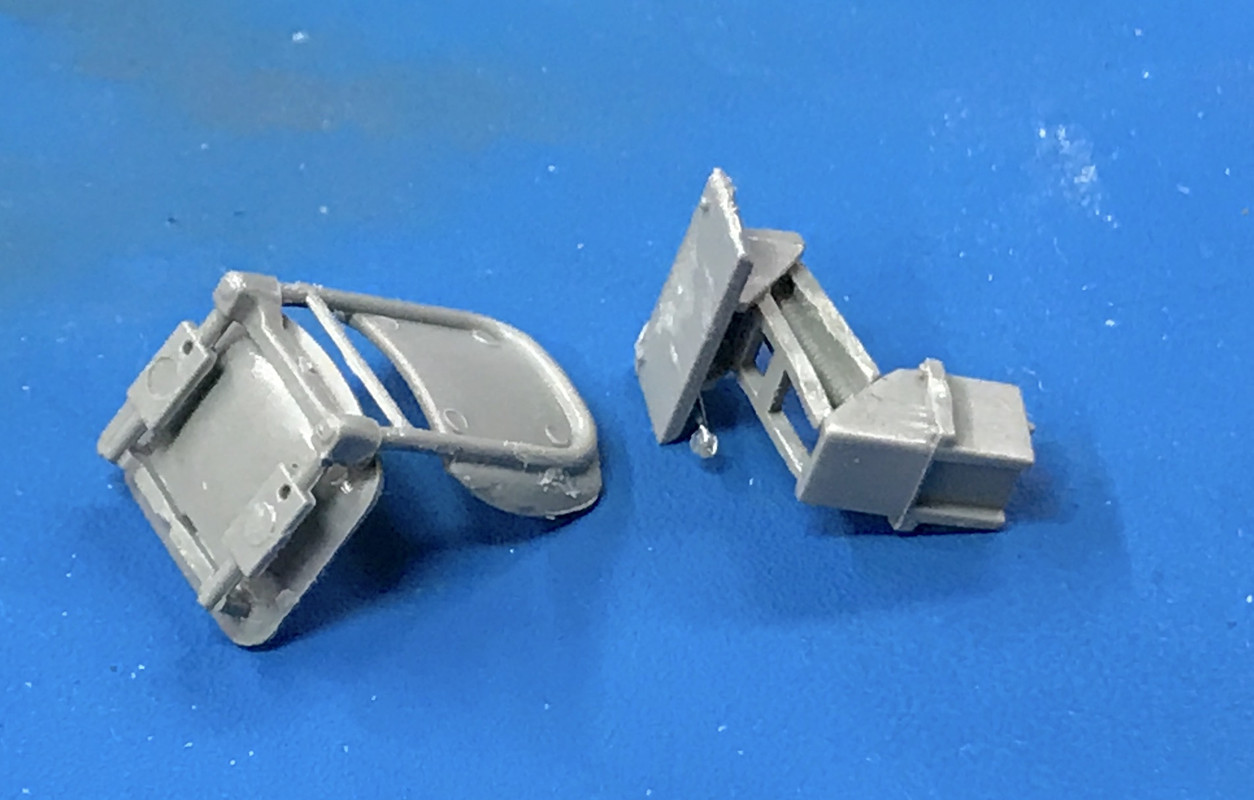
I glued the seat in place after they had a couple of hours to set up. They are very delicate.
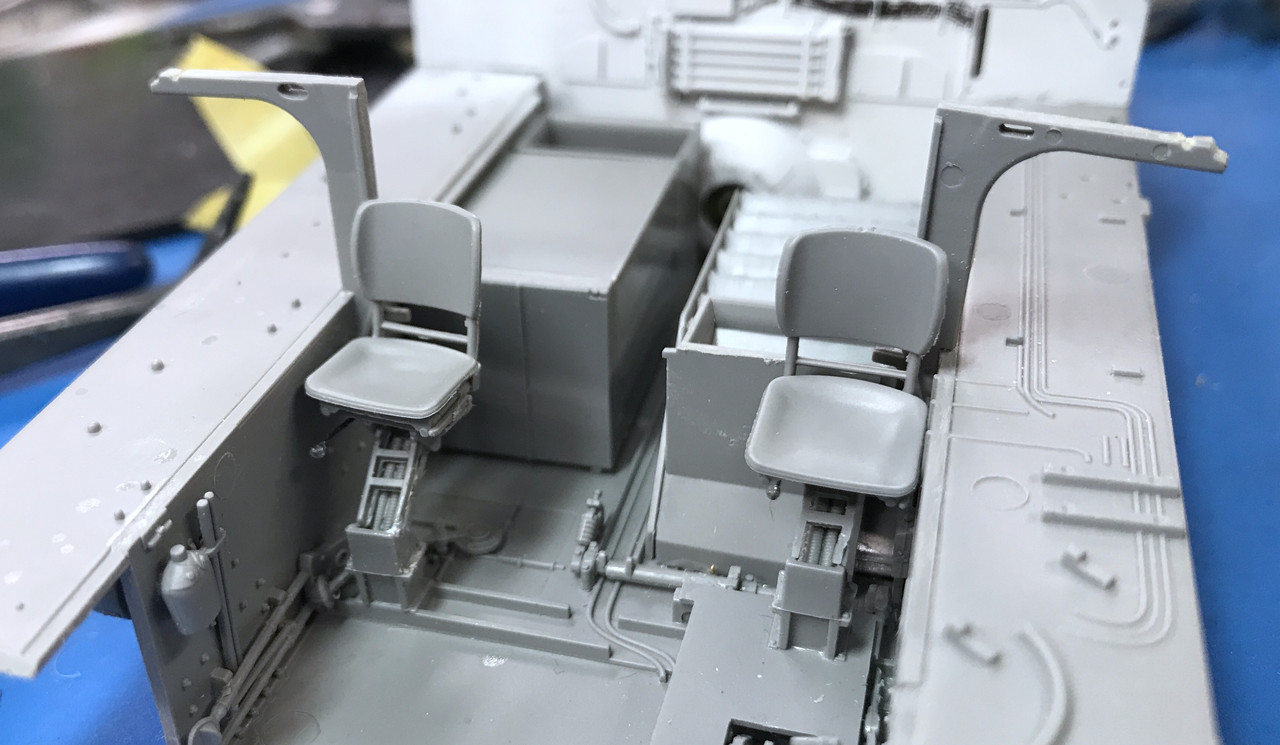
Behind the seats are other assemblies that go under the fighting floor, including the ready ammo rack, another ammo storage locker, an open-topped container, etc. Then there is a frame that supports the turret comparment subfloor. Only one of these things will be visible, the ready-ammo rack. These were sealed containers since this was the 76mm W for "wet" and they were filled with ethylene-glycol.
The frame was a very difficult piece to get settled in. One of the free ends in the back middle/right had a notch that was supposed to clip under the bar that was on the firewall, but just didn't want to go there so I clipped it off.
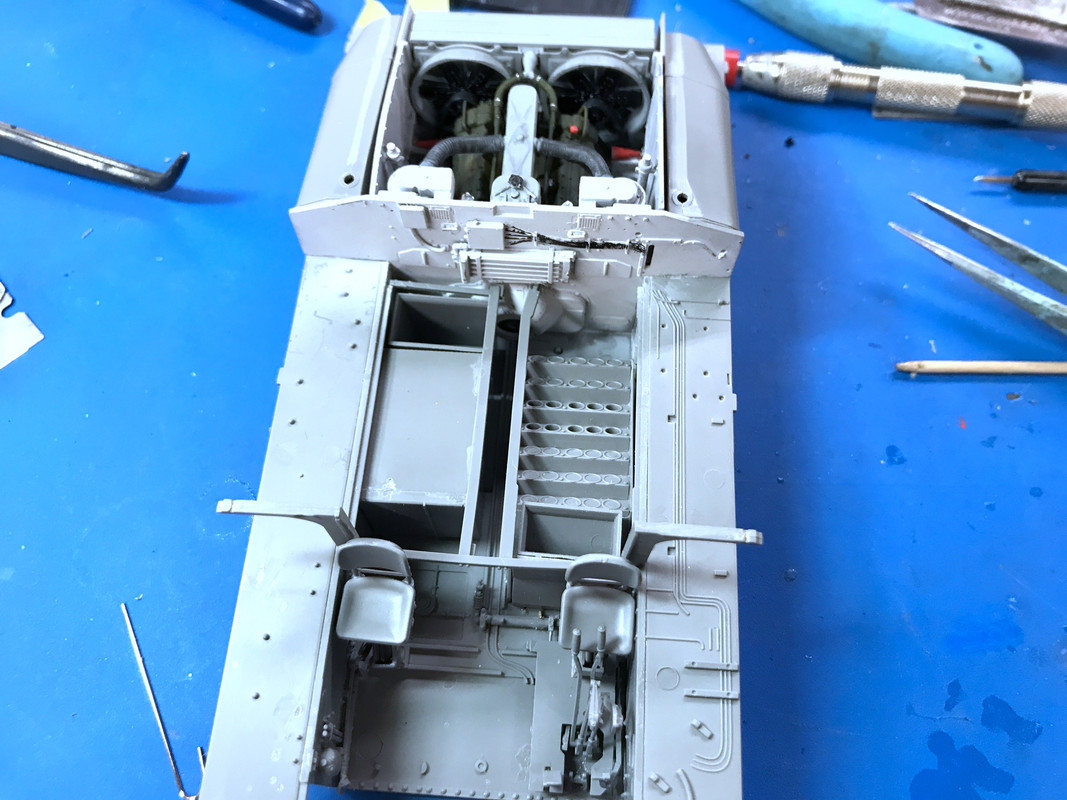
I re-installed the fire bottles in the back right corner.
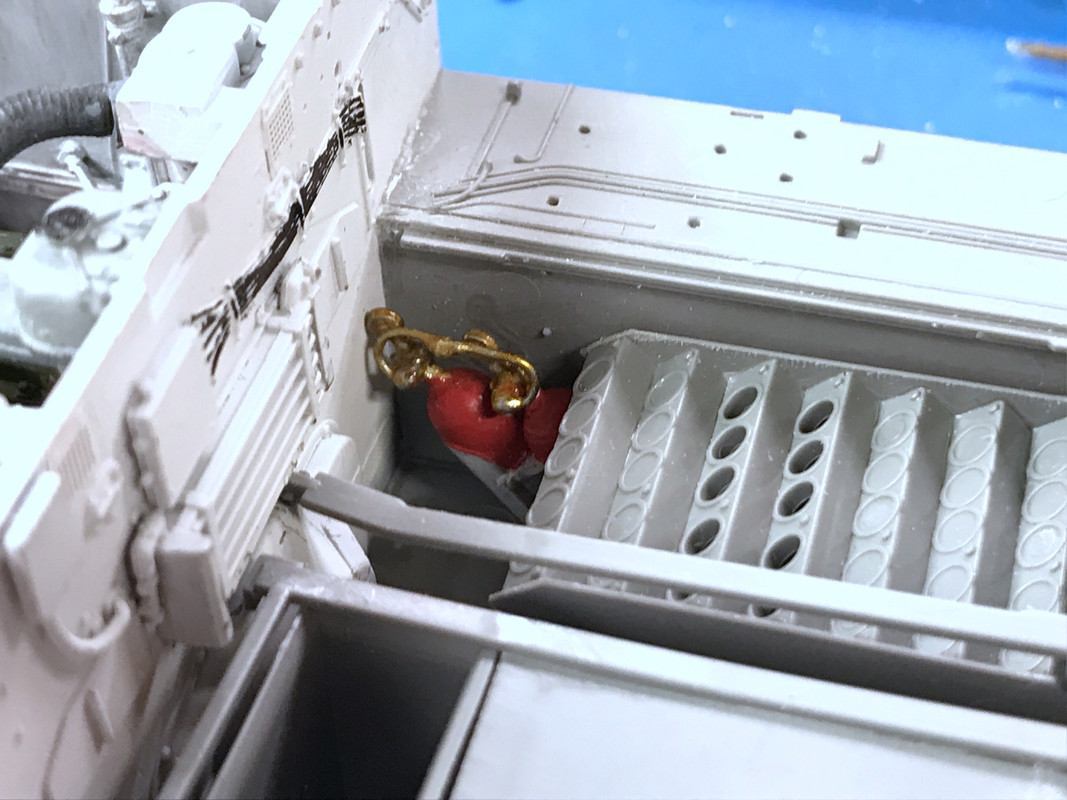
Incidnetally, that pipe rack thing on the firewall is the oil cooler, not a heating radiator. The air is drawn through the cooler fighting compartment by the main engine fans and exhausted out the back. By putting the cooler on the fighting compartment side would keep it much cooler than being in the engine bay.
It was time to paint some more white. I masked the engine compartment and stuffed some foam down the area where the fire bottles were since they were finish painted. I also wrapped a reversed loop of masking tape around my finger and stuck the trans assembly to it so I could airbrush that along with the rest. I only wanted to paint the drivers comparment and the fuel tanks that were also added that are now flanking the engine bay. I didn't worry about the sponsor tops. There are ton of detail that goes there and will be painted later. I just needed to get the lower parts painted before the floor goes in.
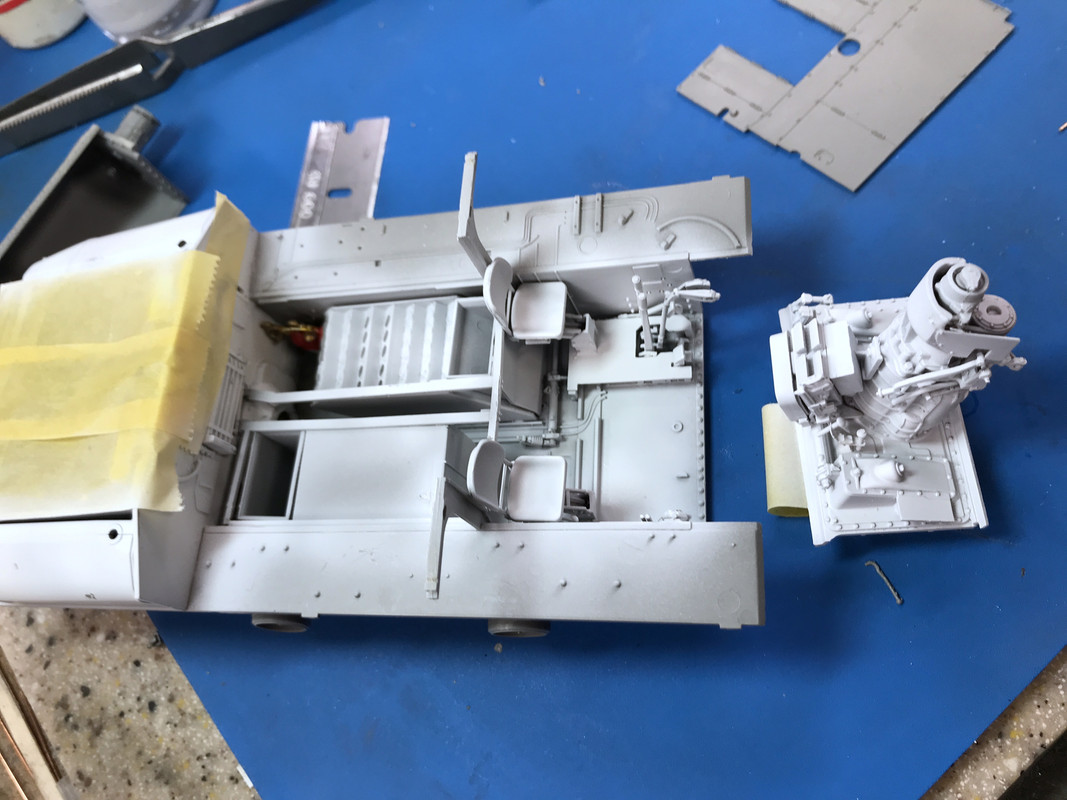
This is all that will be seen when the floor goes in.
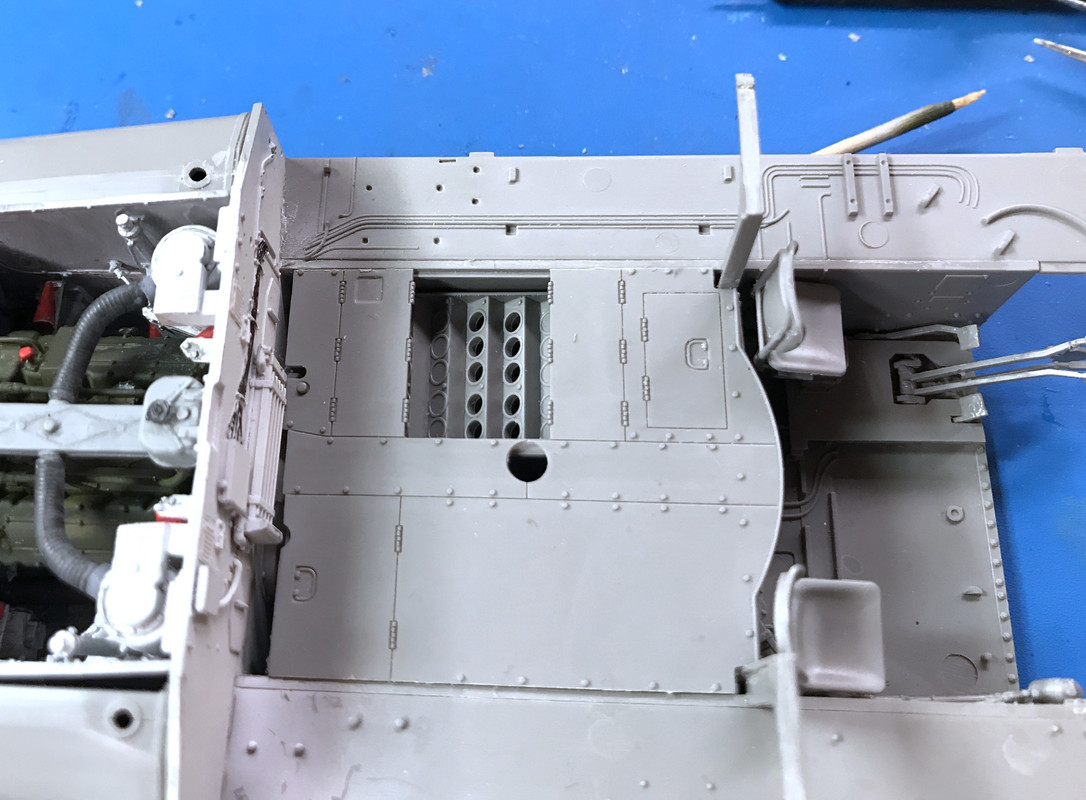
Do you see the fire bottles? Neither do I! Bummer! I have a choice to maybe open up the hatches directly next to them so they're visible. It's my Sherman. I can do anything I want. The problem is that the doors that cover the ready-ammo locker, flop over the same area that the fire bottles are, thus blocking them anyway.
The instructions have starting to build the bogies. Lots of parts! And a bunch of silly parts. While many of you have built armor, I doubt that the bogies had this many parts. At least the ones I built didn't. The indidual swing arms have two parts.
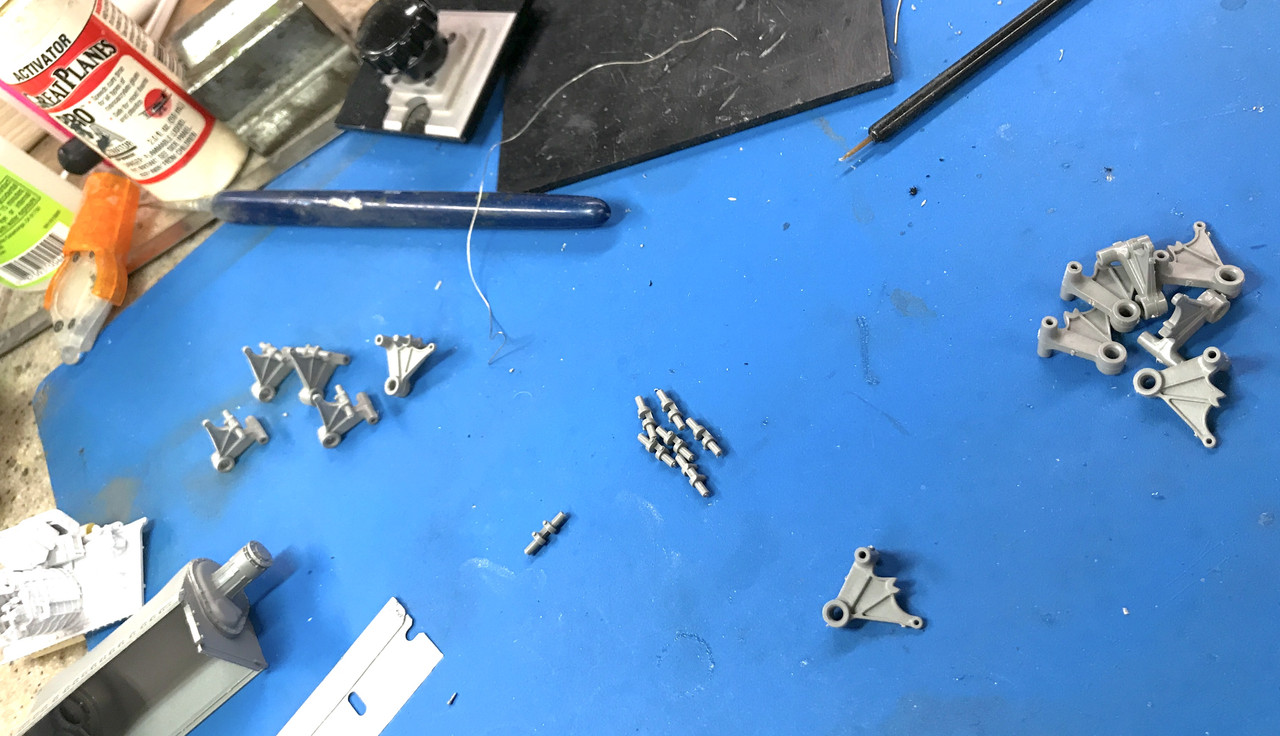
The little round part glues to a notch on the half-arms. Took a while to clean all the parts. No flash, just sprue nubs and some parting lines.
Then comes the shock absorber that is one of the members that holds the two sides together. The shock is three parts: the main shaft and two very little other halves of the two ends. These ends are supposed to be movable if you want the suspension to articulate. I was able to successfully get all of the part 58 (6) onto the one end and captivate the arm.
The arrow shows the notch that the part goes in. The part is laying upside down in the image. BTW: that very large tool in the picture is a very fine-pointed pair of Swiss tweezers. You can only get glue in the notch so the pivot remains free. That was not easy. And the gluing surface is small. The only way I could figure to get it together was to glue the part in place, spread them enough so they could pass over the pivot holes in the shaft and then squeeze them back together. Sounds simple, but it wasn't because the solvent cement would cure too quickly so when I spread them apart to slide them over the end, the little part would fall off. It wasn't too bad one the single arm.
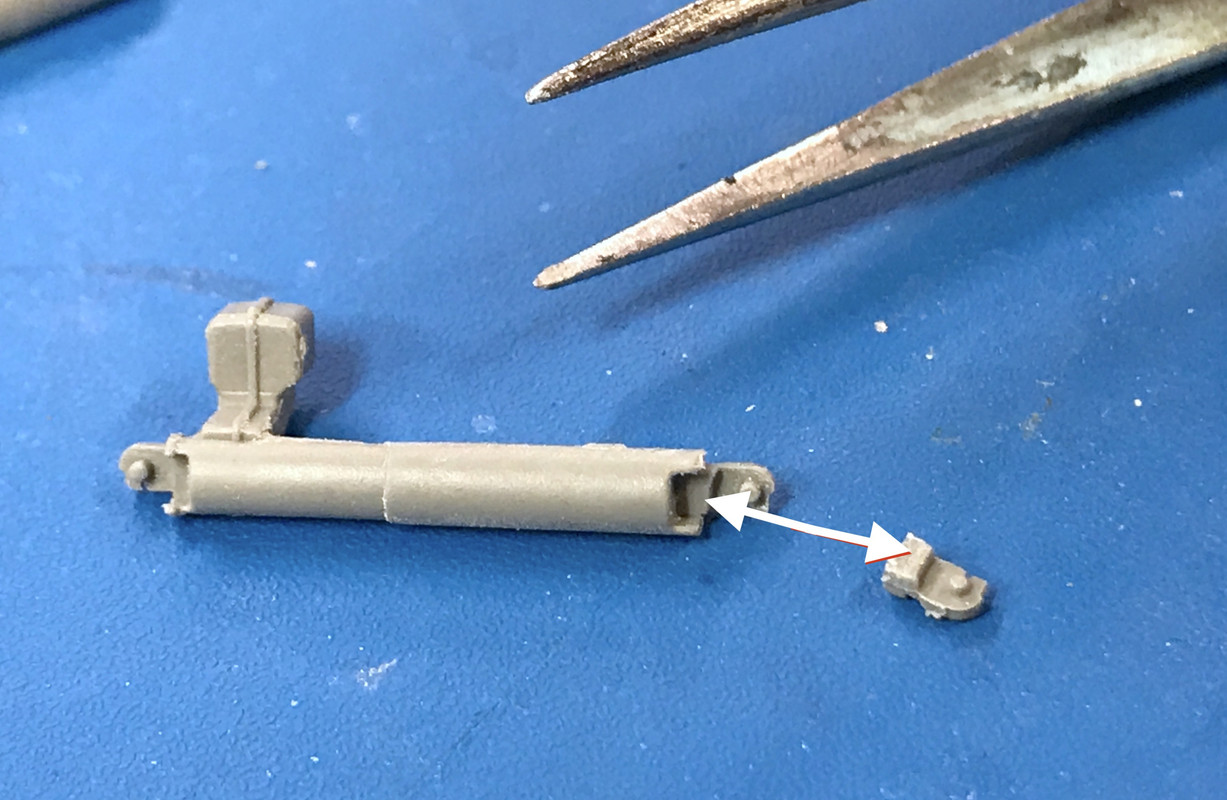
Here are some completed first end connections.
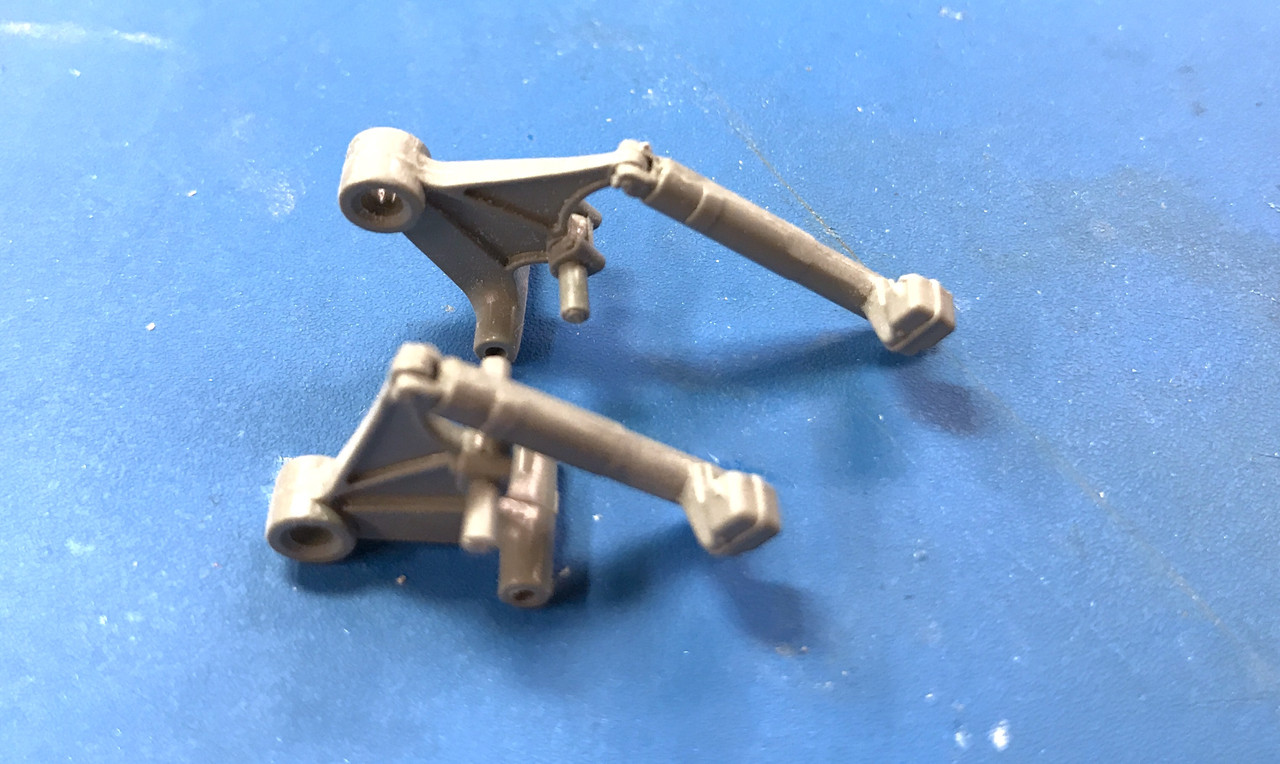
Things have gotten much uglier when I attempted to add the second end and connect the two sides. Again the quick drying cement was causing trouble and I even had the first ends starting to come apart while I was manipulating the parts. And then I kept flying them all over the place as they launched at of those aforementioned tweezers. I'm now down two, hopefully I'll find them, but if not I'll figure something out. My guess if this was Tamiya, they'd made the clevis as part of the shaft and make it flexible enough to spread to snap over the end. Or it could be drilled and pinned. That may not work here because the ends don't have much meat and the holes will probably break out. If worse comes to worse, i could actually make them out of brass. Where there's a will...
The easiest parts so far were the horizontal volute spring assemblies. These two identical parts just slip together. They don't actually expand and contract via the spring action. But they're not supposed to be glued to that cylindrical cross shaft and I'm not sure how they'll hold there. In the 1:1 Sherman, the springs are pushing outward with signifcant force.
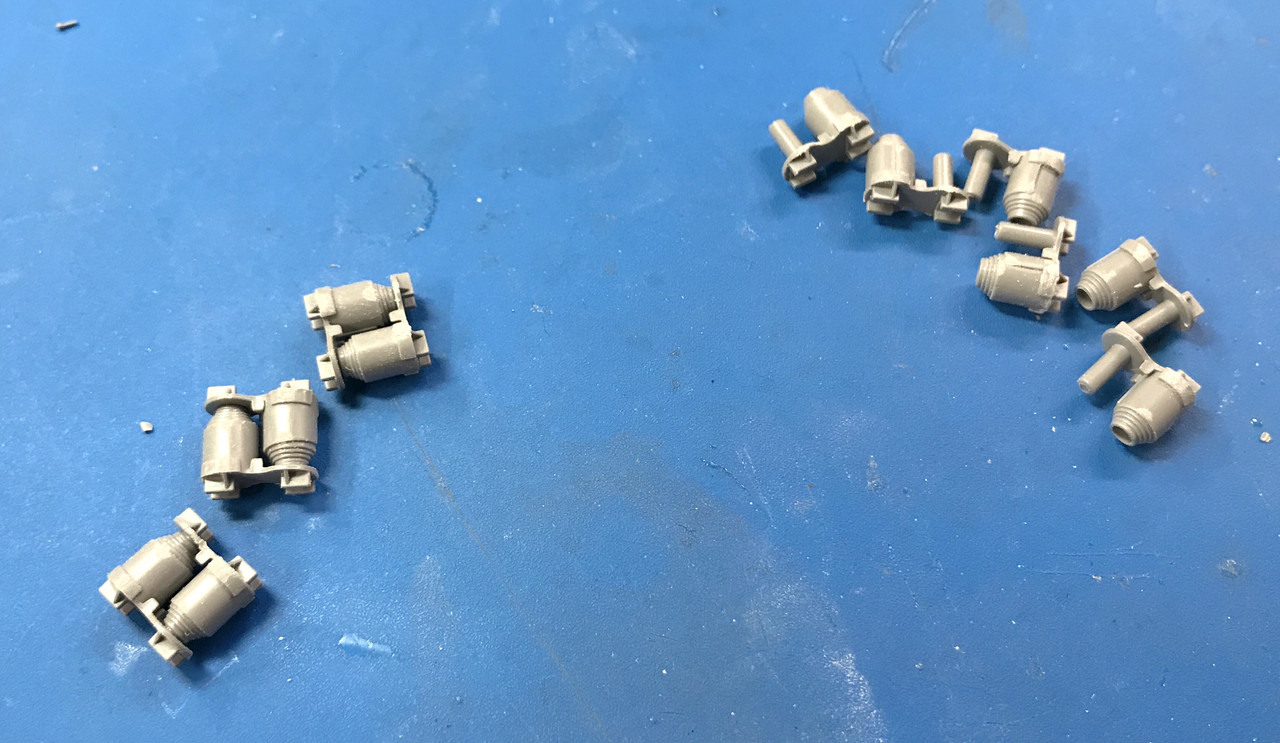
I'll keep going on this tomorrow.