Now that I've gotten to a comfortable point with my other projects; I'm now in full concentration on Kanu. From last night, I was able to get the initial priming session done. I will explain the reason behind the term "initial priming" a little later. I did a quick fit after the priming so that I can take a few snaps of her together :
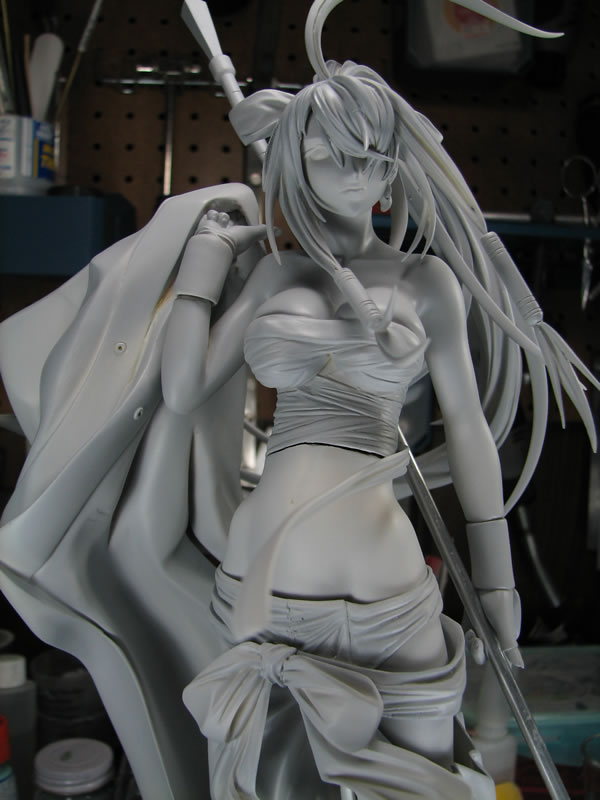
Since the last update, most of my parts were glued and puttied for gap filling:
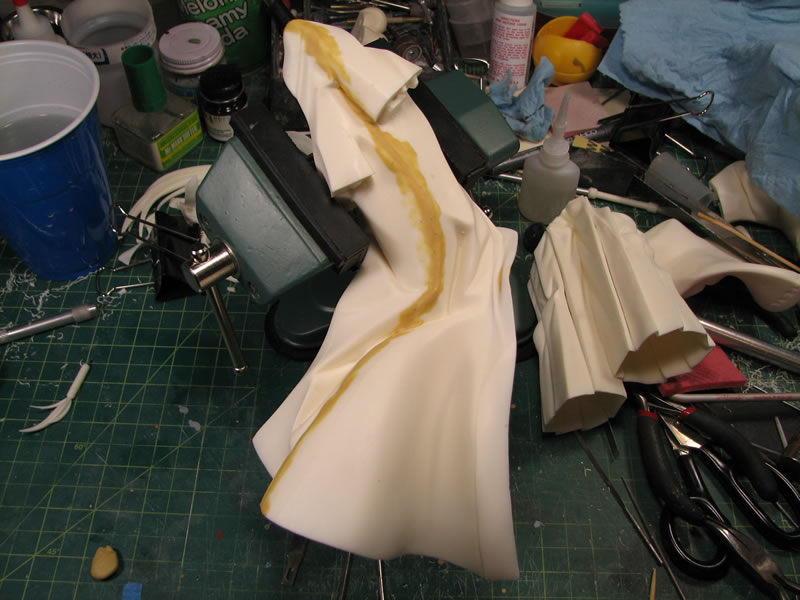
After a the putty cures, I went in with the various sanding implements I have (files, 100 grit sand paper, 100 grit sanding pads, 150 grit sanding pads, 320 grit sanding pads, the toothbrush sanders, the flexi-file sander, etc) and went to work on sanding down all excess putty as well as sanding down all the mold lines and surface defects on all the parts.
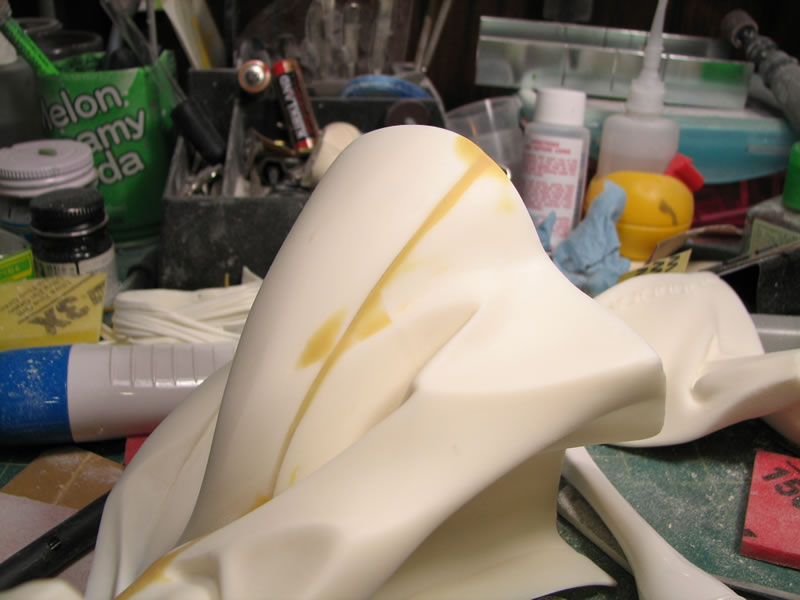
The robe is composed of 4 pieces, the 2 major halves, then two smaller pieces that attach to it. I first glued and gap filled the major part. Sanded that down, then sprayed on a primer to check for defects in the gap filling process. Once I was satisfied, I then went on to glue and gap fill the smaller pieces.
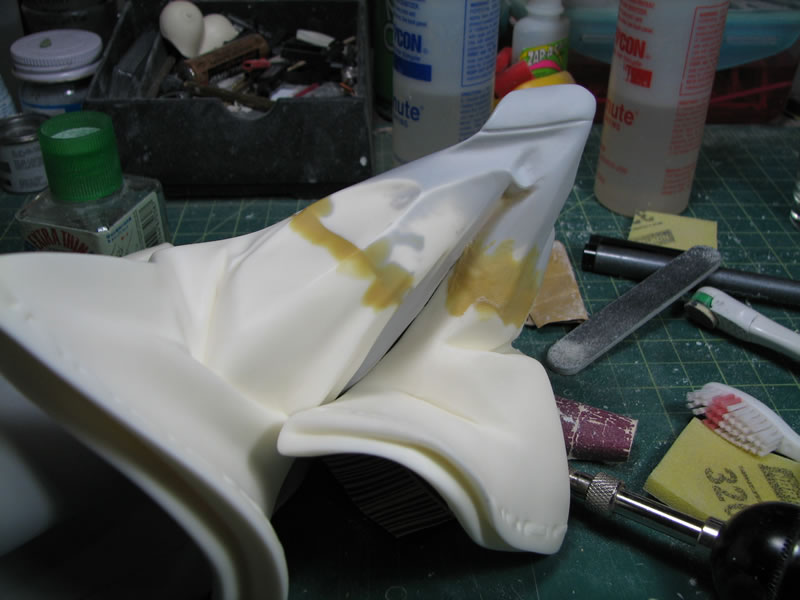
With all the parts sanded, I threw them all into a purple colored industrial strength cleaner for a couple of days. The industrial strength cleaner will dissolve any residual mold release that may still be on the surface of the kit. This is a very important step as all the hard work of sanding, painting, masking, more painting, will be useless if the paint and primer fail to stick to the surface. After a couple of days in the purple cleaner bath, the parts are removed and placed in a bowl of water to help wash off the cleaning agent. From this point, parts that fit into the ultra sonic cleaner are then placed in there with regular water and run through the cleaner. This ensures that the parts are pristinely clean after the soaking. The parts too big for the ultrasonic cleaner are just scrubbed with an old toothbrush.
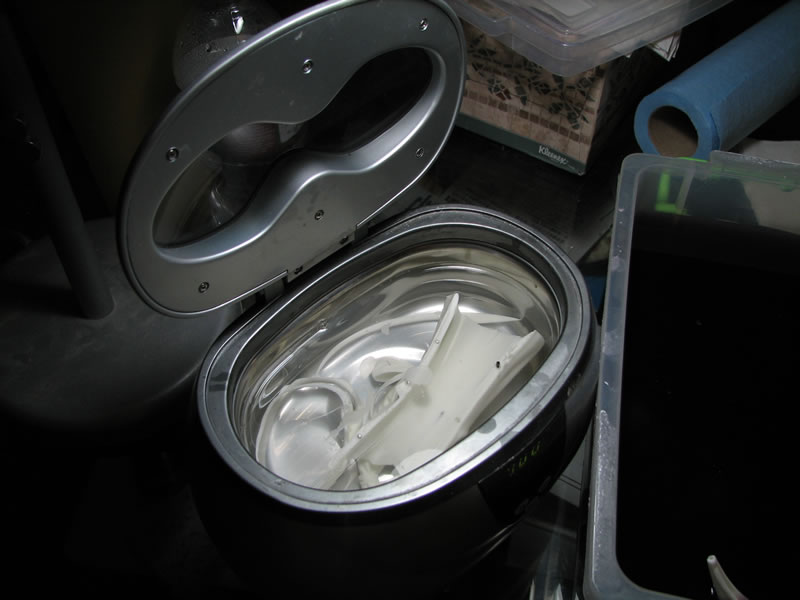
The parts are then dried and placed on skewers or alligator clip attachments and are now ready for the initial priming session. At this point, the parts are clean and white. It is difficult to tell if the surface was properly prepared. Sanding marks, pinholes, tiny surface defects are very difficult to see.
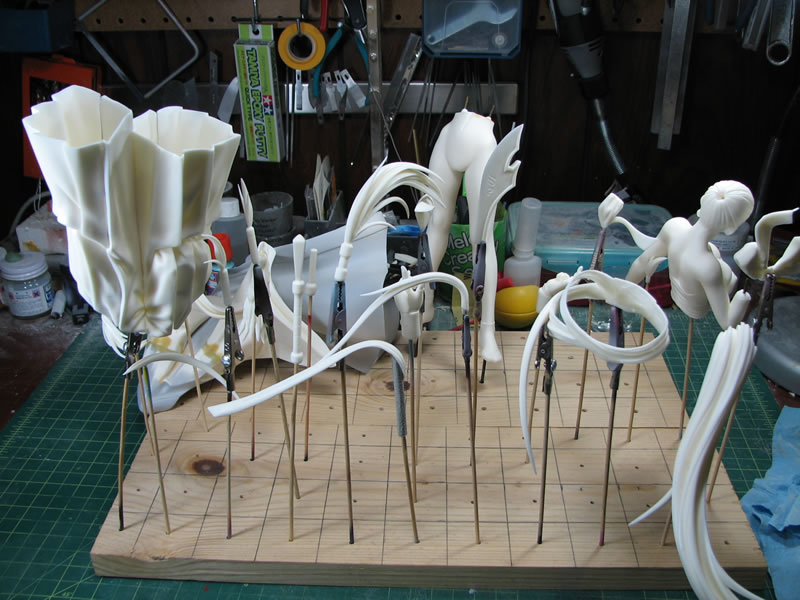
I use Mr Resin Primer by Gunze Sangyo. The primer is gray in color and once sprayed on to the parts; the small sanding mistakes, missed surface details, pinholes, gaps, etc become very clear, and now I can get some fine tune sanding and work on problem areas with much greater attention.
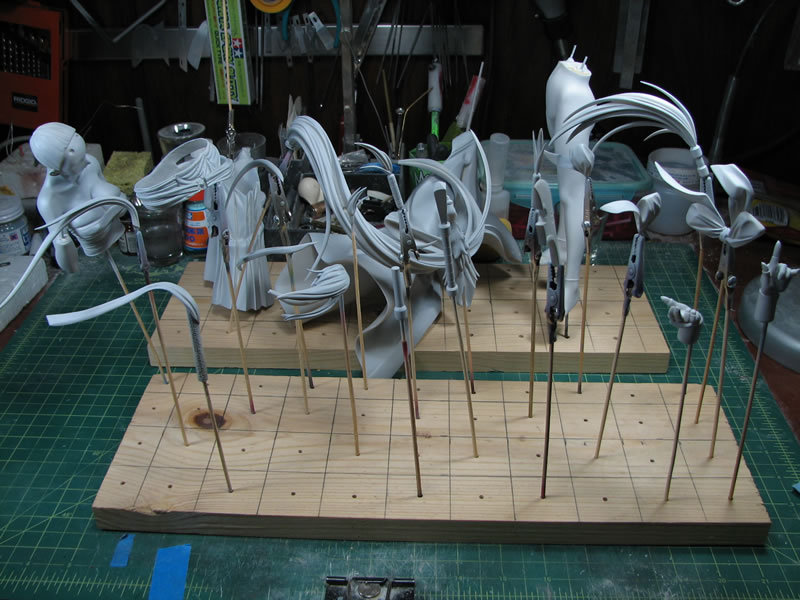
And just for the sake of taking photos, I did a quick mock up: