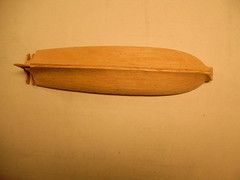
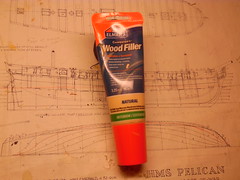
At the left is a clearer picture of the balsa MORRIS hull, where the bow has to be sanded down to the same configuration as on the plans of the PELICAN. Bulkhead additions were added to extend the stern the one inch to agree with the Hahn plan. Open spaces between the extended bulkhead additions were filled with Elmer's Carpenter's Wood Filler.
If I may put in a plug for Elmer's wood filler, that should be included in every wood modeler's box. Unlike most wood fillers that are packed in cans, this filler is contained in a plastic tube that is squeezed out like tooth paste, then the lid screwed back on. This has the advantage of having the filler remaining soft without contact to the air, unlike most canned fillers that soon dry out into a hard lump to be discarded.
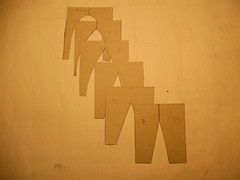
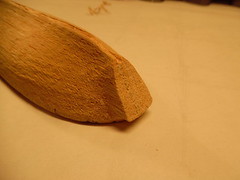
Trying to shape the balsa bow to agree with the Hahn plan required more planning. Consulting the plan drawings, the waterlines, which are horizontal stations drawn fore and aft, delinates the shape of the hull from the keel upward to the top of the bulwarks. On the Hahn plan, these waterline stations are marked "A" at the keel, then move upward to "F" at the waterline, where the ship meets its watery environment.
At each water line station at the bow, cardboard templates were cut out and labeled as seen at the left picture. Taking my Electro-File and inserting a sanding pad on the tip of the instrument, the bump on the balsa bow was gradually sanded down, while every so often, a bow cardboard template was inserted where a penciled "A" to "F" station was drawn to see that the sanding agreed with the template profile. After a slow sanding process, the balsa bow took the shape of the Hahn plan bow.
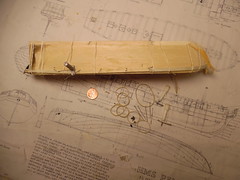

Now that the balsa bow and stern agree with the PELICAN plan, it's time to begin planking the hull with 1/4 inch wide planks cut from popsicle sticks on a hobby table saw. Before planking, the keel, the bow cutwater and the rudder stem was glued in place. Each horizontal plank was held in place with small elastic bands. Metal planking screws with an attached tab to hold the plank in place and also to prevent the plank from slipping sideways by the pull of the elastic bands. The copper penny gives the scale of the project.

The hull planking is now completed and brush painted with Minwax Polyurethane, to seal the wood and fill tiny spaces. Painting the hull with acrylic paints will happen later.

Before the deck planking began, each popsicle plank was rubbed with a black felt tip pen to sinulate the oakum and tar cauking that was used on the real 18th century ship to prevent water from leaking between the planks onto the inside deck.
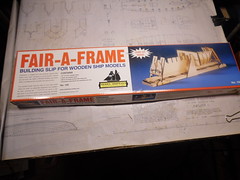
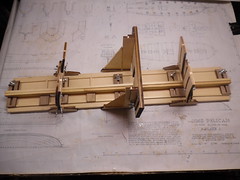
It's time now to plank the deck. To hold the model hull upright in a secure position, Model Shipways, Fair-A-Frame was used for this purpose. This device is used to build plank-on-bulkhead model ships, where the keel is secured in place by two horizontal clamps held in place by winged screws, while vertical supports prop up each bulkhead.

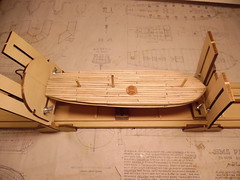
Here, the deck planking process has begun, while on the right panel, planking is completed. This panel also shows how the Fair-A-Frame holds the model hull secure. Wooden pegs were placed in holes where future masts were to be inserted. While decking planking, these wooden pegs made sure deck planking was accomplished around the mast holes, rather than over these holes.

The completed deck planking was stained with Minwax Golden Oak stain.
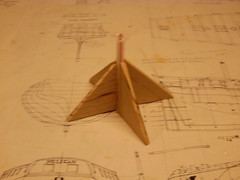
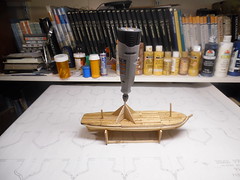
To make sure the mast holes were drilled absolutely true and straight in a vertical position for the future masts, a template was devised consisting of a plastic soda straw held in a upright position by wooden triangular supports. This template was placed over the mast holes and drilled deeper by my Dremel Cordless Electric Drill. The right panel is only for demonstration purposes. When actually drilling, both hull and template were held firmly in hand. Using a 90' right angle straight edge as a check, all three holes were found to be accurate.
I see by the clock, it's bed time. To be continued by copper simulation of the hull bottom.
Happy modeling Crackers 
