DK666 wrote: |
|
Yup Got em. Wanted to surprise everyone.
Here are the Weapons that I choose to Cast, 6 out of the 10
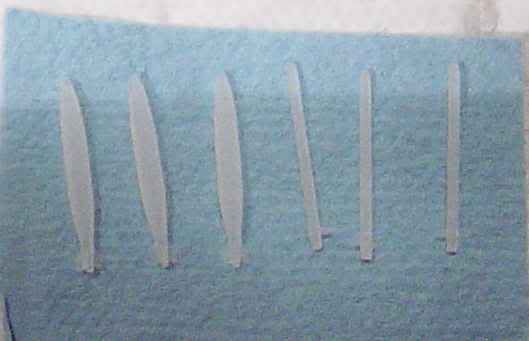
Putting the Sprue on the first of 6
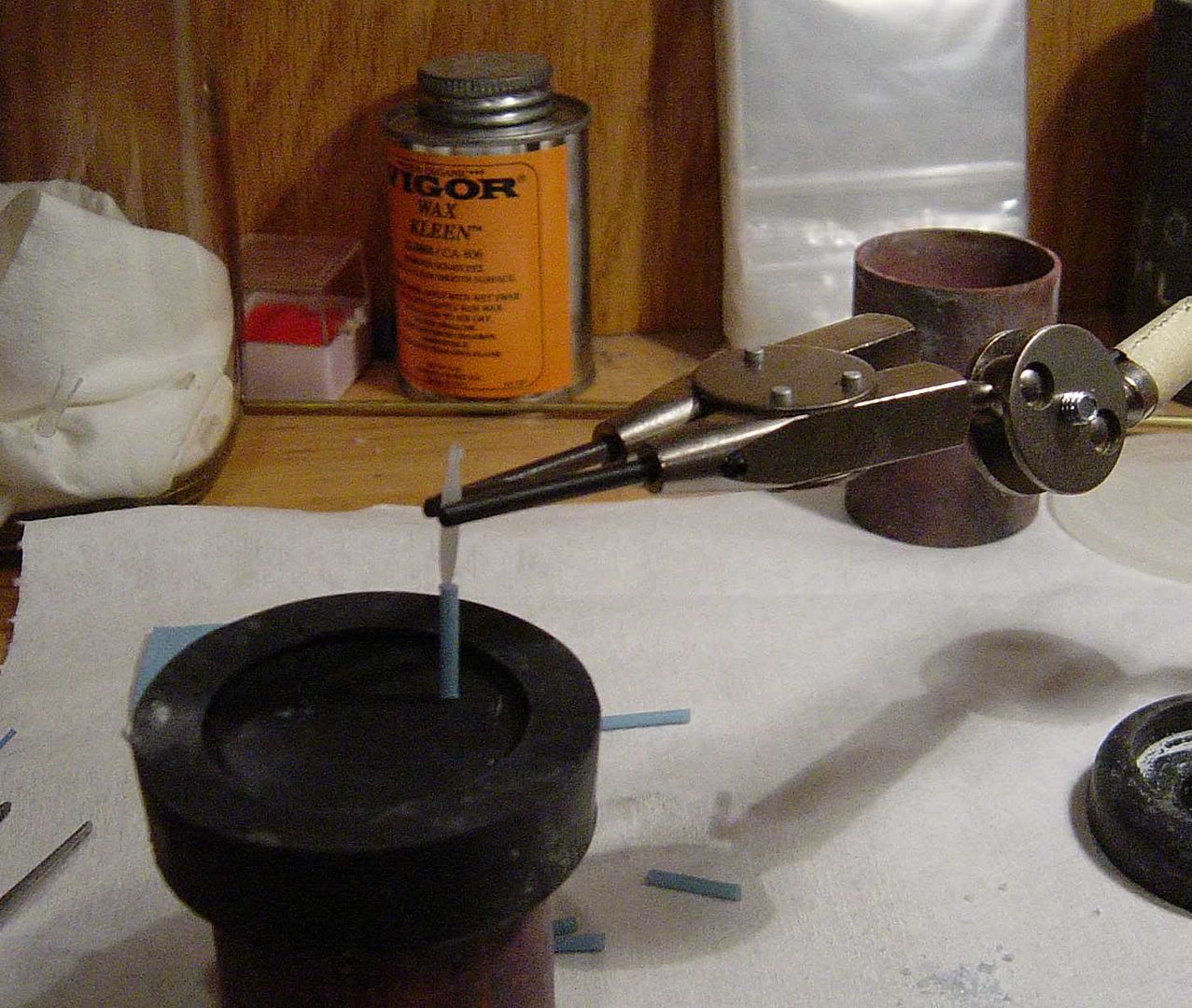
Here are all 6 Sprued and Waxed to the Investment base
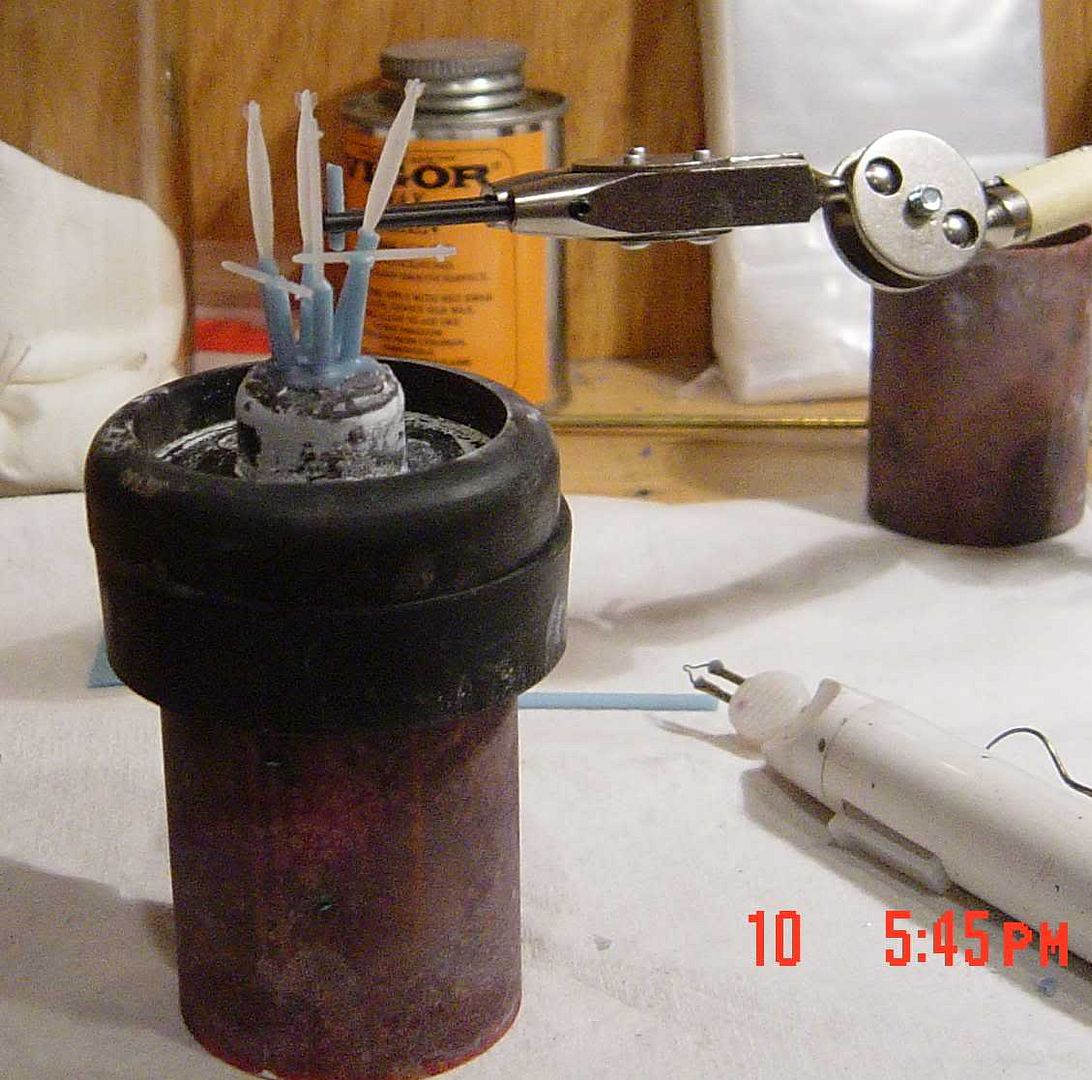
Now they have been sprayed with a liquid to decrease surface tension prior to pouring the investment. And, the canister has been mounted on the base almost ready to pour and vac
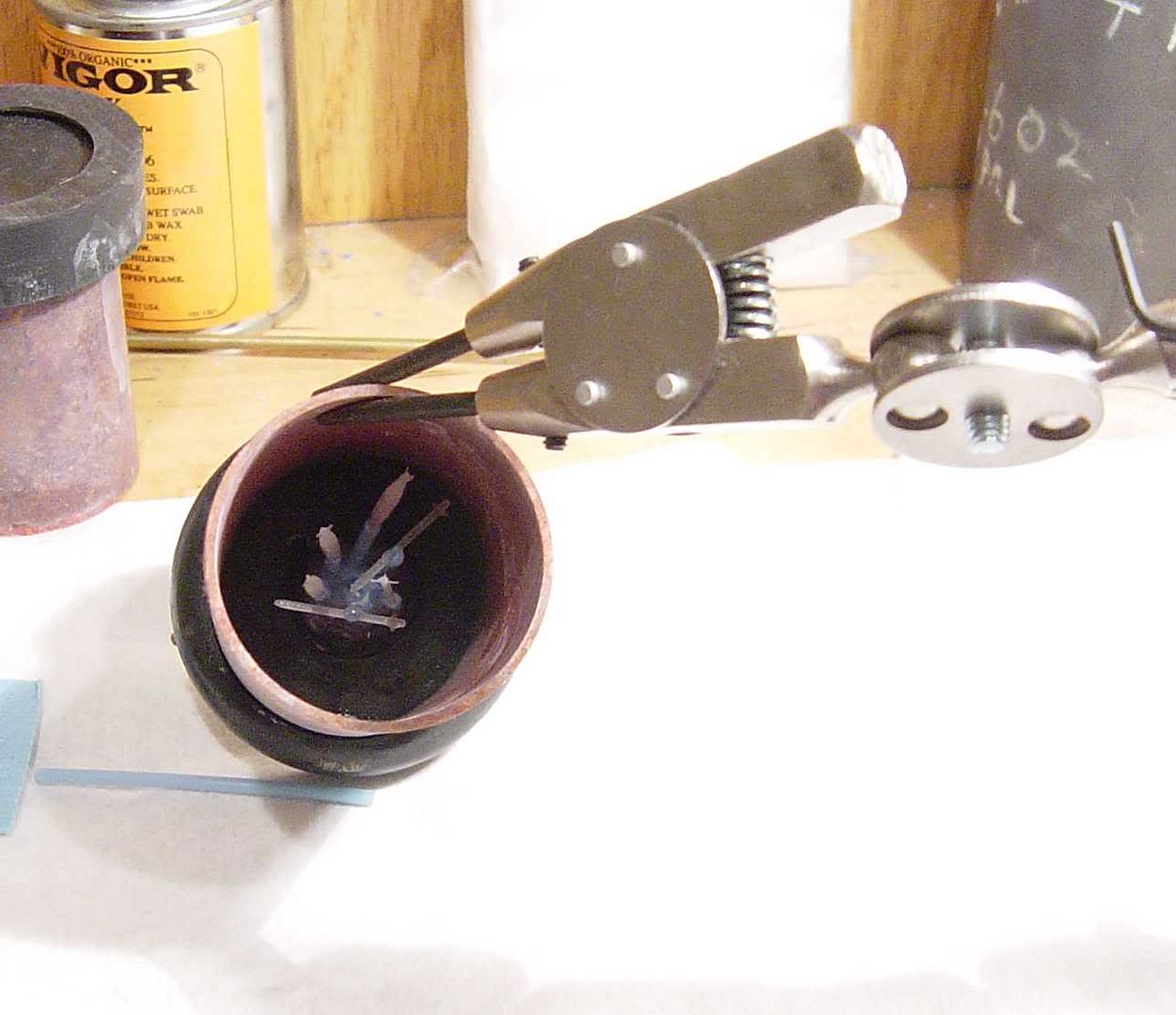
Here is the medallion with 4 sprues attached. one on the edge center, two on each edge side at about 90 deg and one up the back into dead center of the back

Now it has been sprayed, and mounted on the base ready for the investment.
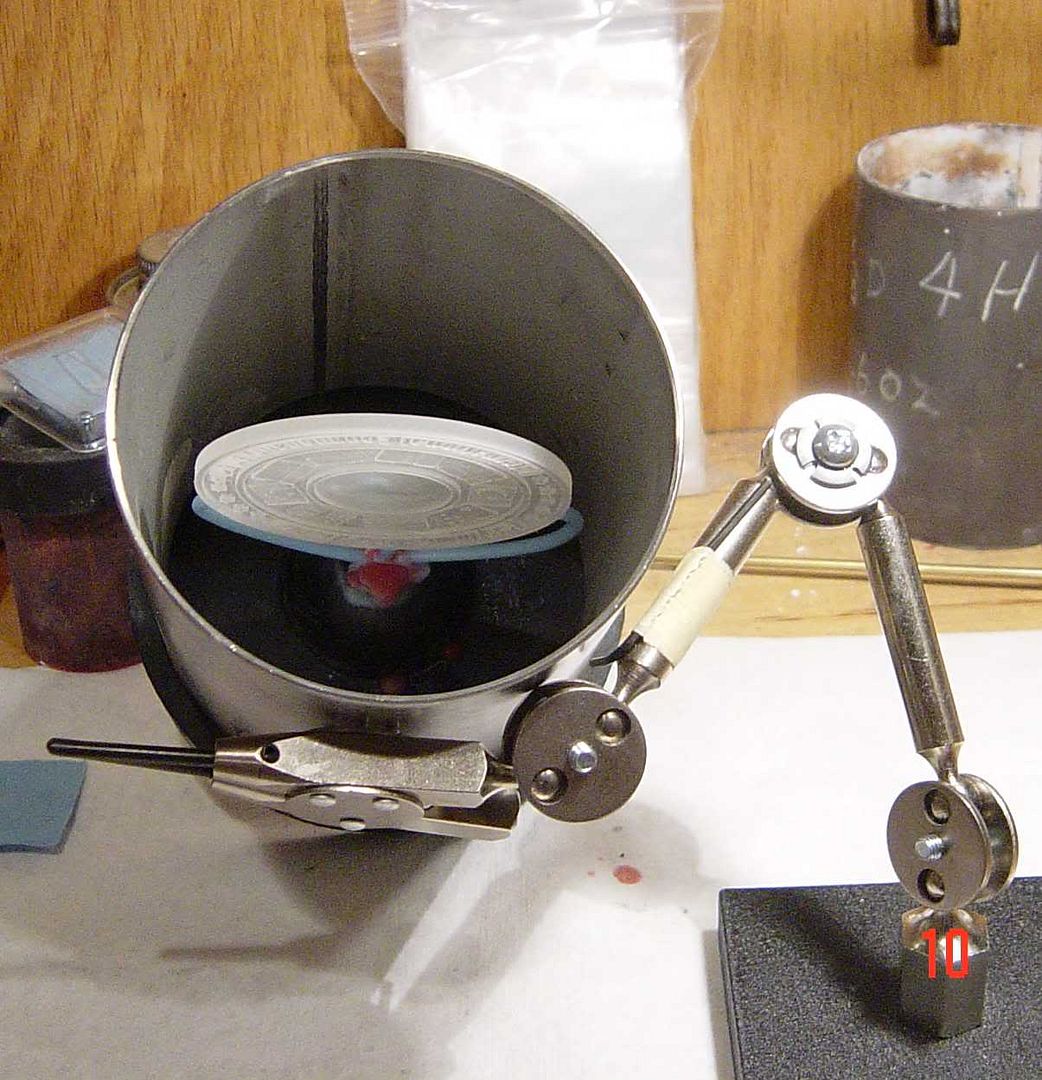
Here are the canisters fully invested and setting on the vacuum plate. The process is to mix up a closly measured amount of investement with a closly measured amount of water for 2 minutes, vacuum in the mixed mode for 2 minutes (I get about 27.5 in of merc, pour it into the canister and vac and vib for 2 minutes. Counting the slack time for moving around, 7 to 7 1/2 minutes have passed. And the investment will set solid in another minute or minute and one half. The base is then removed and the surface top and bottom is trimmed and made concave with a plain old knife and left to dry out as much as possible. I try to do it overnight.
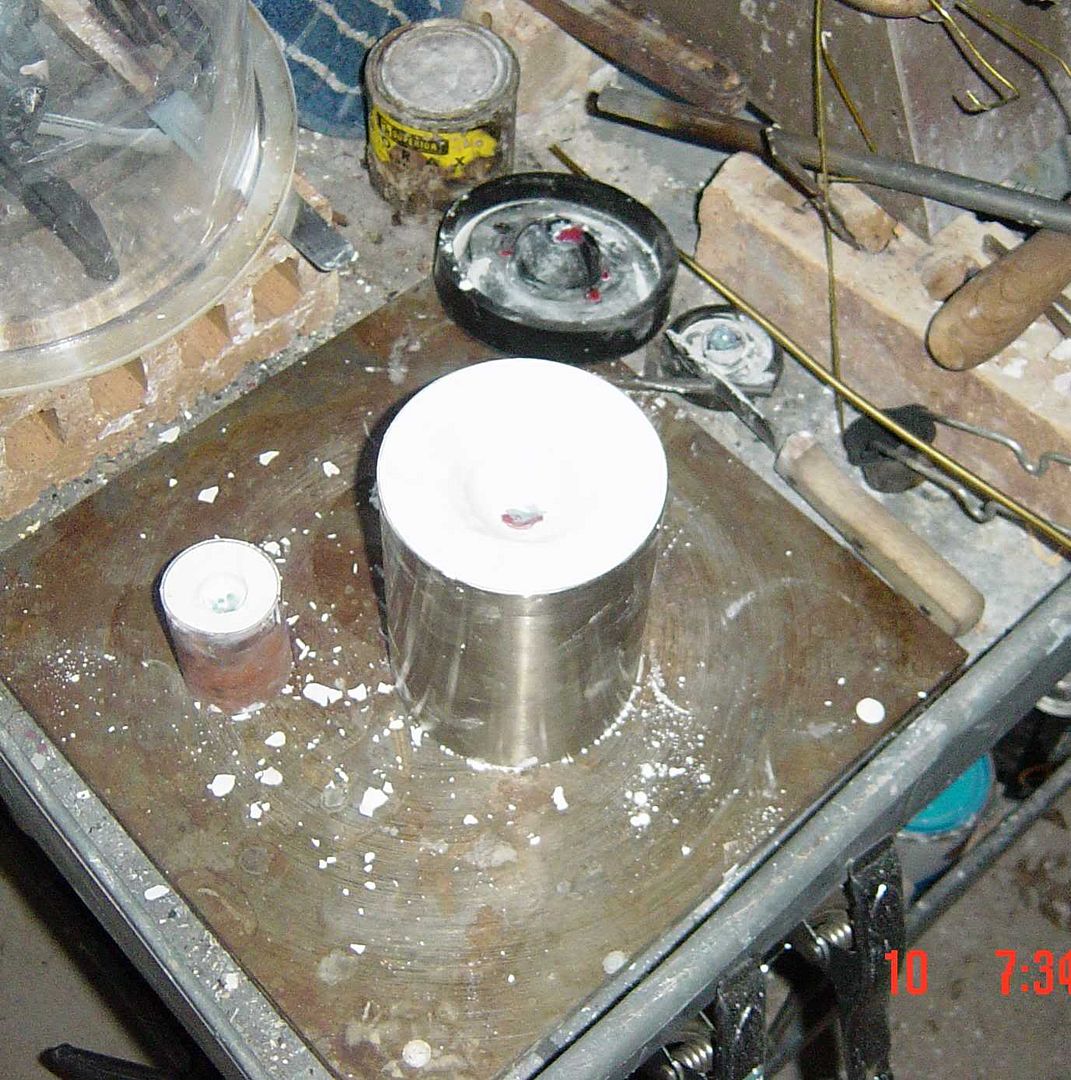
Now put them in the oven to bake. 2 hours at about 450f, 2 hours at about 1000f, 1 hour at about 1400-1500f, rest for another hour after the temp is down to 1100f
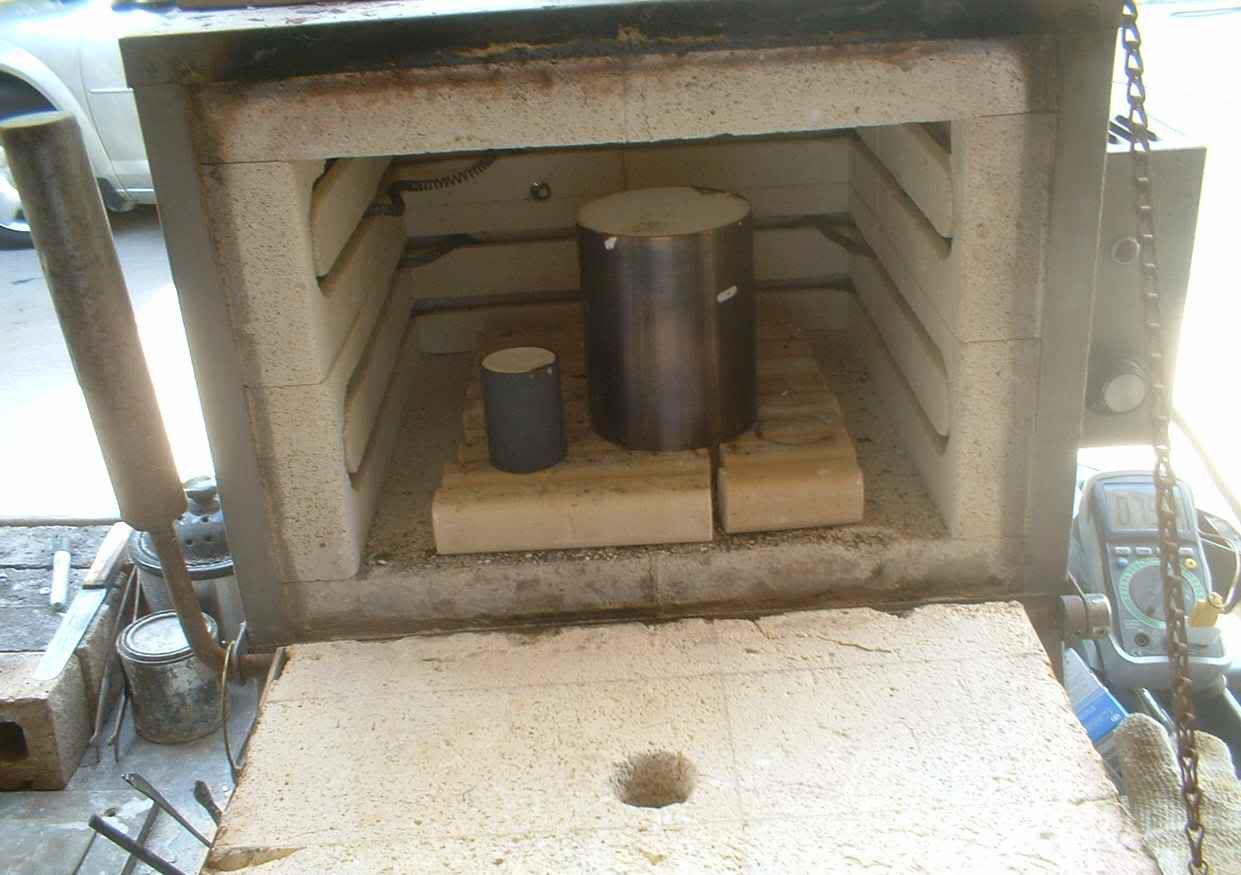
The medallion has been poured and she took the picture during the pour of the small Weapons
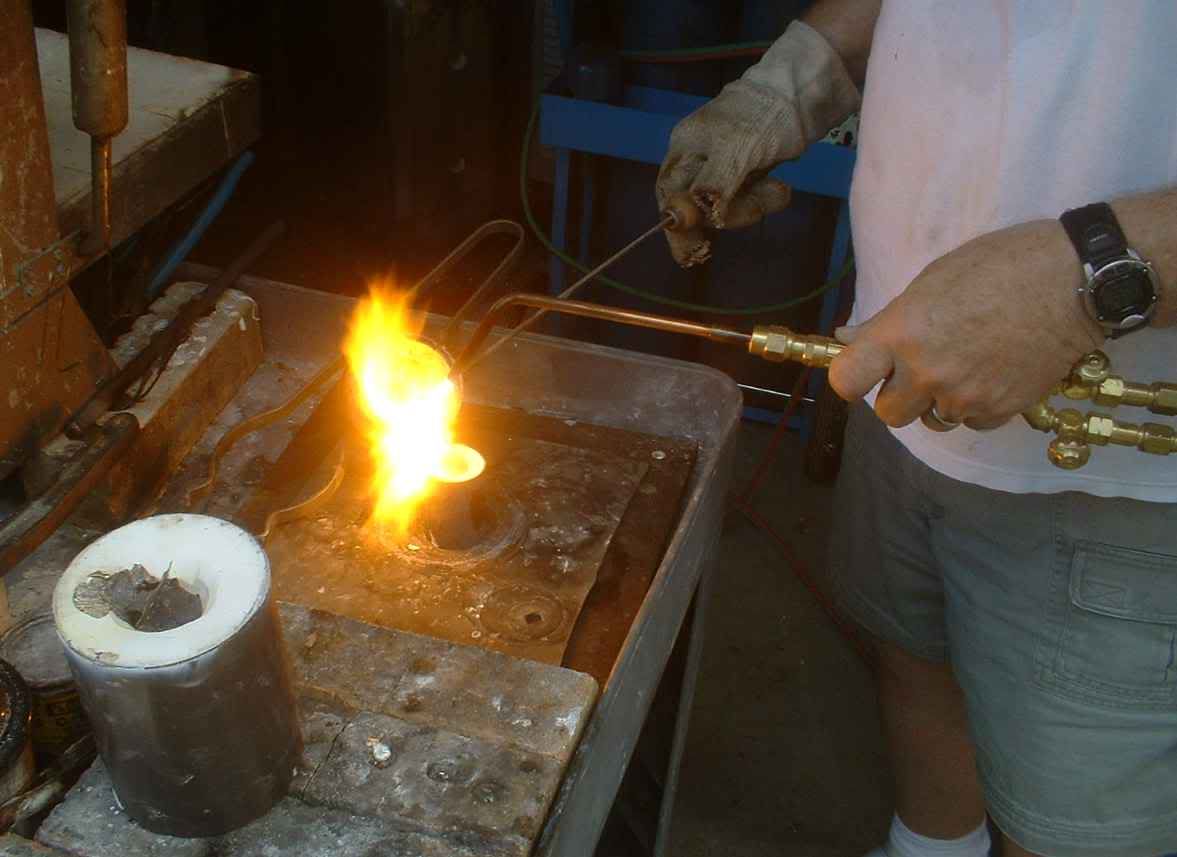
The quench. After the sprue turnes dull grey, it is submerged sprue end first in water and then totally. The canister and investment create steam which blows the investment out and the object can be removed
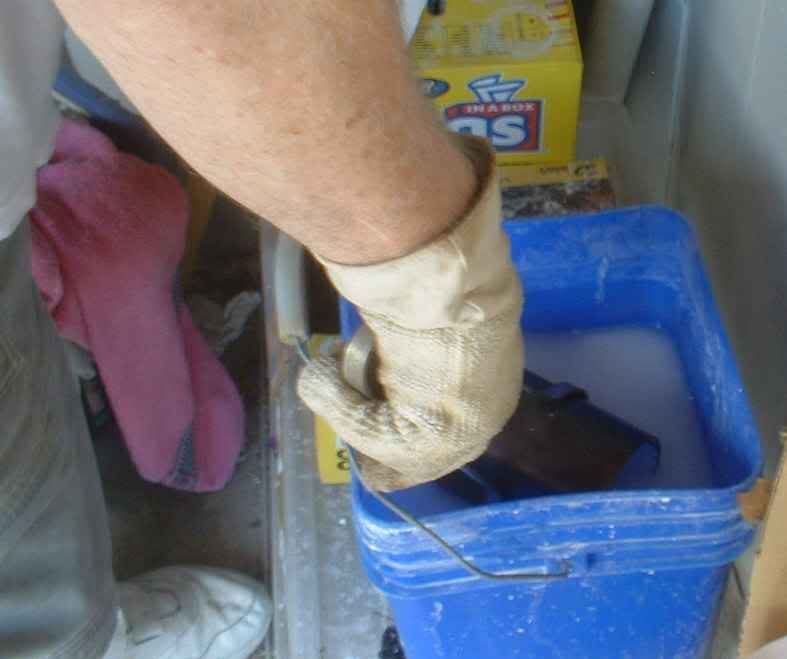
Success on the Medallion
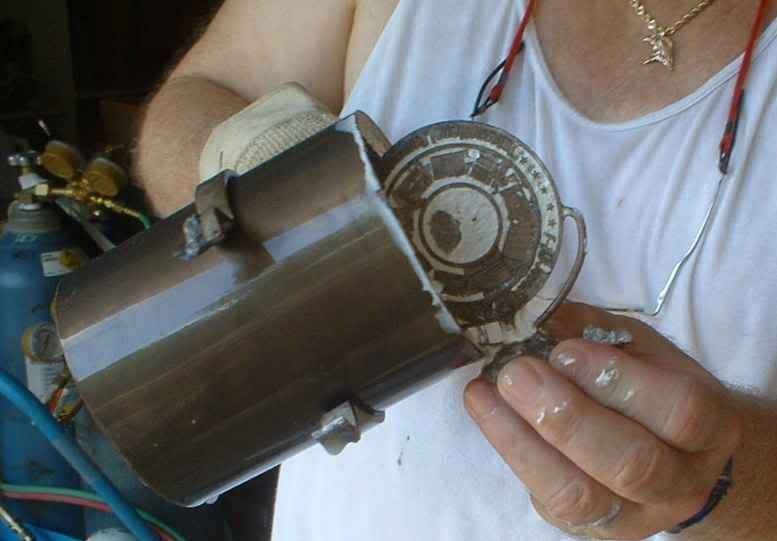
5 of the 6 Weapons turned out. I mounted them in various positions to see if there was a good or bad way. One of the horziontal ones must have broke loose during the investment because the sprue end turned out great.
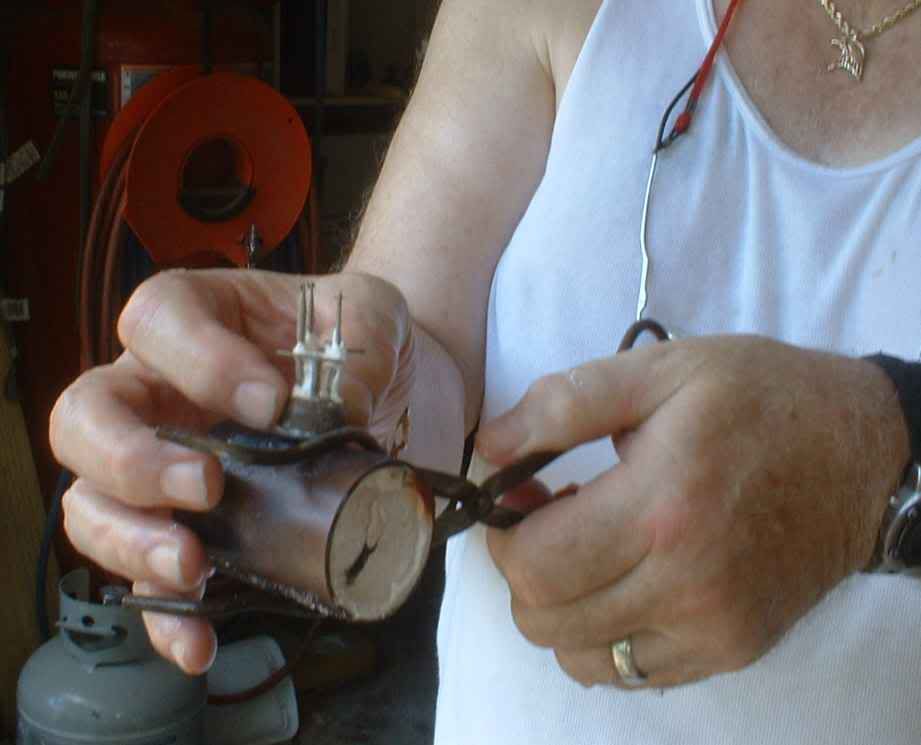
Ed, I'll contact you with some changes that will be required to be successful.
Regards Caster (RLW)