Happy Monday!
We are at the beginning of the end! I'm doing all those things that were left until now so they wouldn't get wrecked. Even with all those precautions, I still knocked off a few things that needed re-attachment.
I started by making the slot in the rear cockpit bulkhead to receive the newly added hinge bracket. I measured the brass tab's width and marked that with a dividers. I then drilled these three holes which were then opened to a slot using the #11 blade. I'm surprised that there wasn't a slot in this part already. This was a kit part.

I then flipped the beast over, put it in the bead foam support and mounted the gear doors and the missiles. For the inner gear door and the main door I used "Glue Dots" which are very sticky bits of contact adhesive. They're very tenacious and hold well, plus they're a bit flexible and won't break loose like CA which is brittle. Henkel Loctite makes a flexible CA which has rubber in it, but it's not available on the retail market and it's black which doesn't work well for a lot of modeling situations. You buy the Dots at Michaels. If you get it, be careful. There are both permanent and removable versions now. I suppose the removable ones could be used for holding masks.
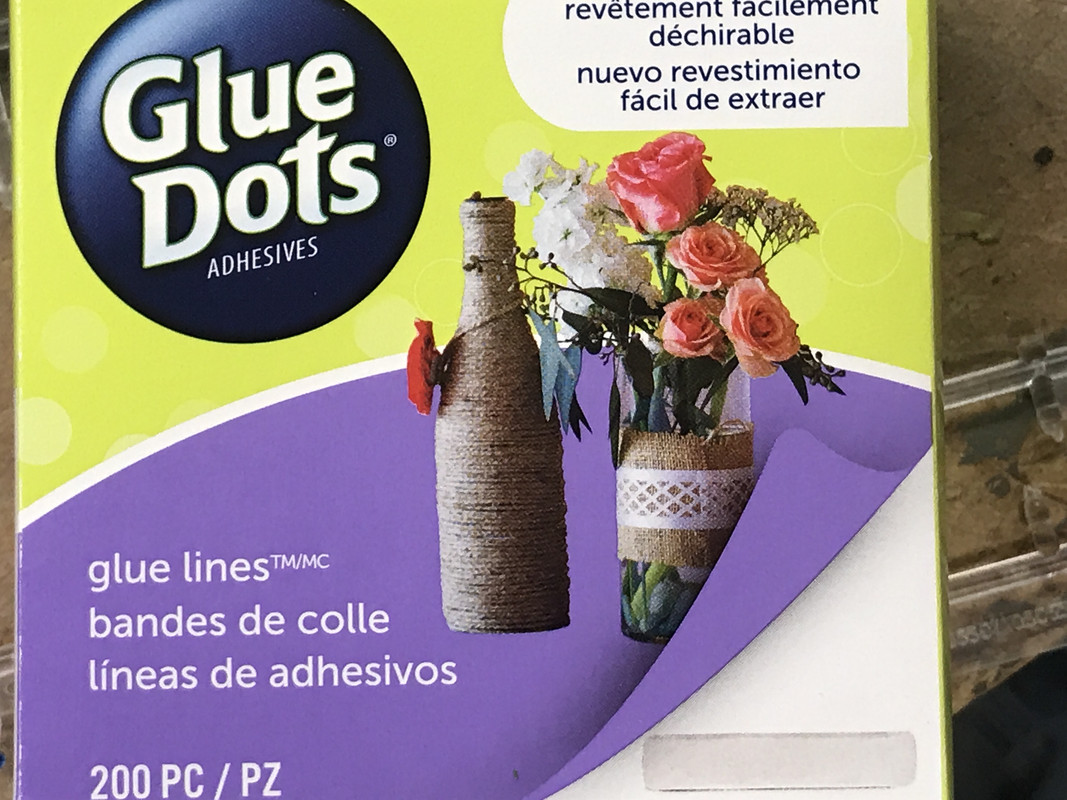
For the inner doors I used the dot form of the adhesive, and I recently bought some linear strips and used them on the main doors. I just put the adhesive strip on the flat side of the strut and stuck the door on. Once you've placed it, you pretty much have to live with it since it holds like crazy.
I used Testor's Tube Cement to hold on the missiles after scraping some of the paint off. Then I knocked some off when I put the model on the bench and the missiles hit some paint bottles. This was my fault! The work bench was a mess!
I also glued the big center tank in place. I did not rebuild those missing auxilary levers that would close the small third gear doors. They're really hard to see and even harder to scratch build. I'll see what kind of mood I'm in tomorrow.
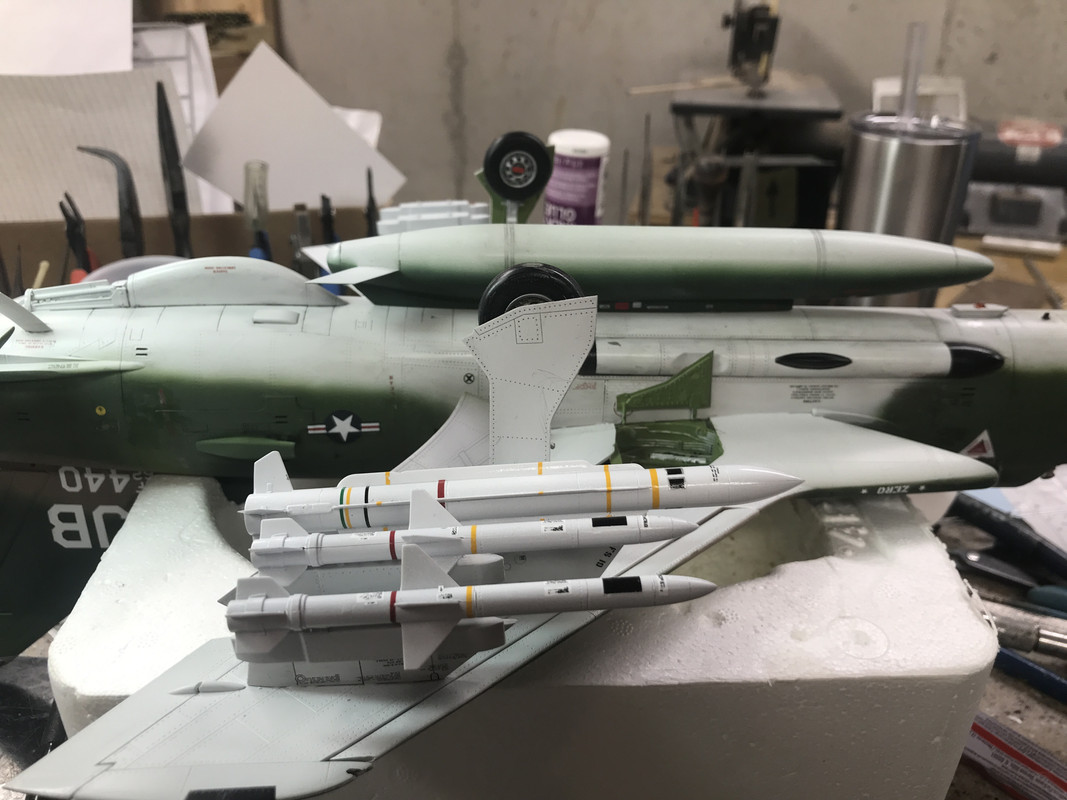
I went to insert the belly marker light which I pre-painted on the sprue, but the darn thing didn't fit into the opening and it was getting all screwed up (paint coming off, etc.). At least I was using my new Testor's Canopy Cement. I decided to go the Bondic route by filling the opening with three layers, each UV cured, and the final having the same shape as the original lens. I painted it Tamiya Clear Red. Bondic is a life saver.
I then flipped the model over and got back to work on the topside punch list. I built the HUD with Canopy Cement, added a couple more PE instruments on the instrument panel cowl, did some touch up painting and got it ready to receive the windshield.
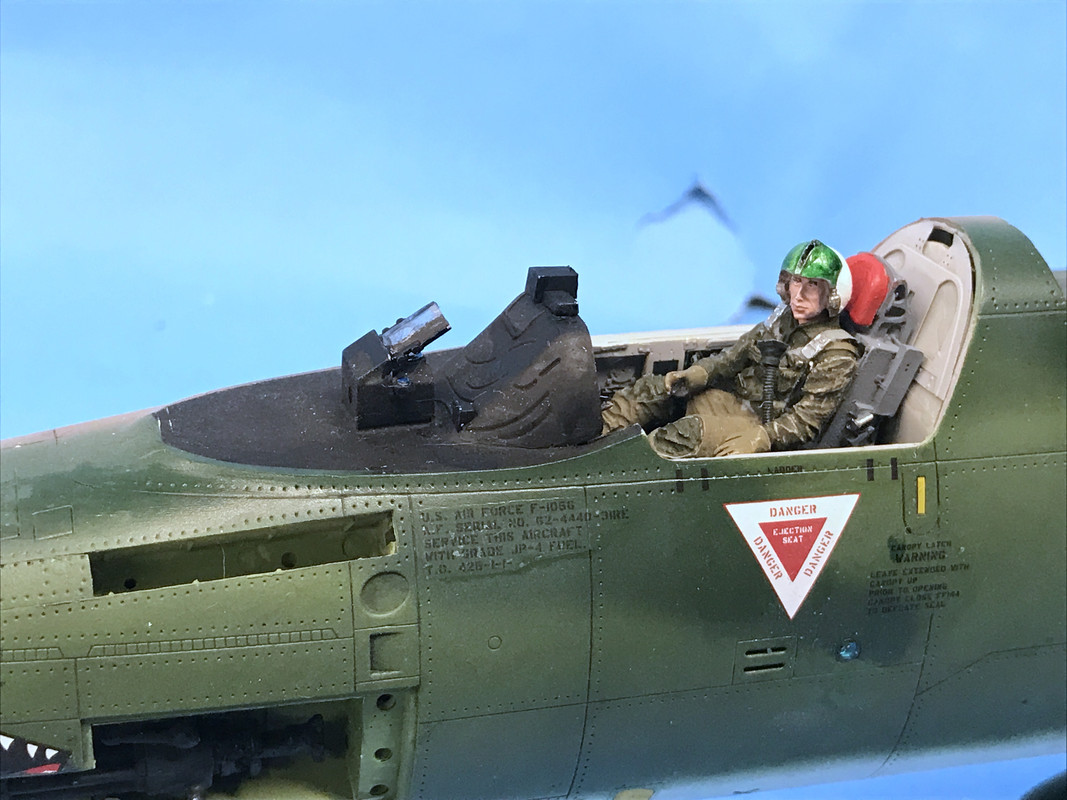
It was time to finish up the canopies. Based on Marty Schwendau, the Plastics Dept. Manager at Scale Reproductions suggestion, I bought some 1/32 "Pin Stripe Tape" used for model car building. With this I made some very believable gasketing for those Thud canopies. In the pics, none of these are in their final, glued positions.
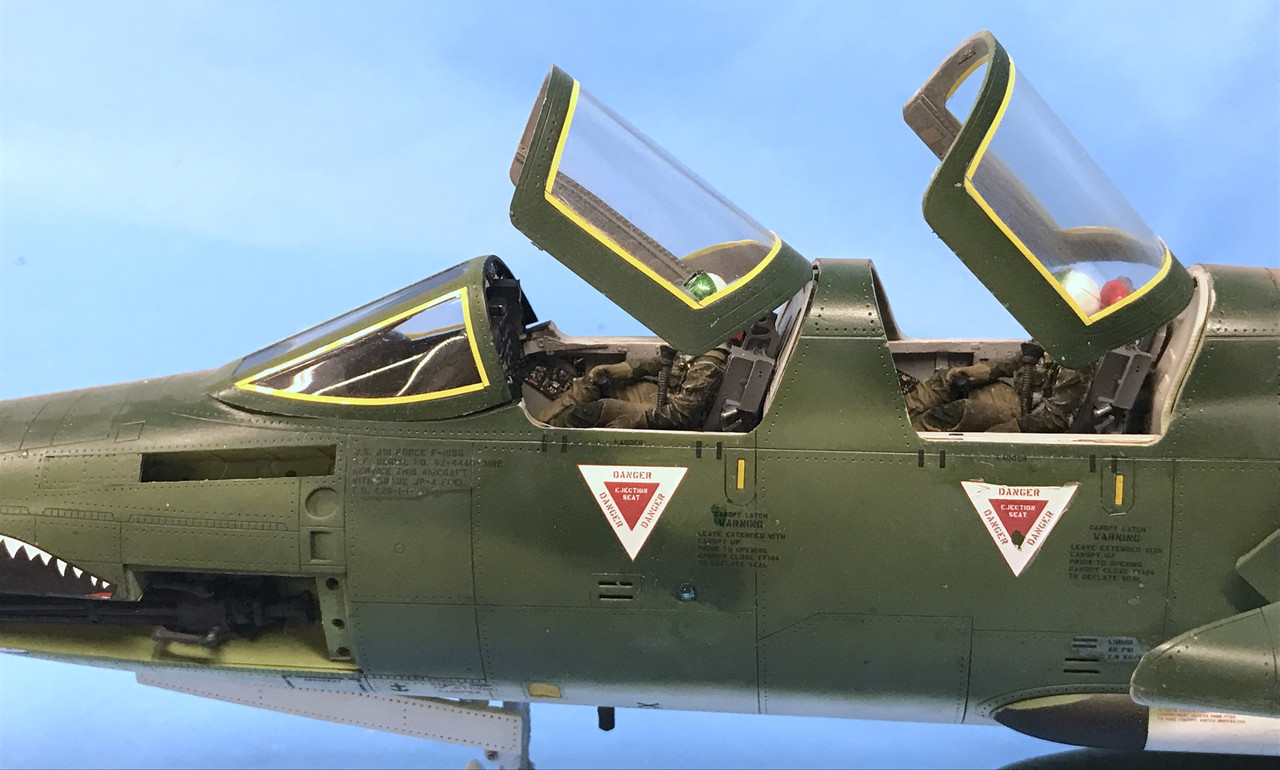
In the process of putting the stripping on the windshield, I broke off all the added pieces hanging from the bottom of the windshield frame. At the end of the session, I was in the process of remaking some of these including the rearview mirrors which weren't looking so hot. I'm making new ones out of very high polished PE fret left over from one of my grandson's projects.
I also attempted to add some wiring details in the gun bay. I broke two carbide drills in the process and was getting very annoyed, so I gave up on it.
I also attempted to put the blue identification lights in their holes in the sides. like the bottom lens, these did not fit nicely. Again, I went the Bondic route. I started by painting the holes silver, filled them, and then painted them clear blue.
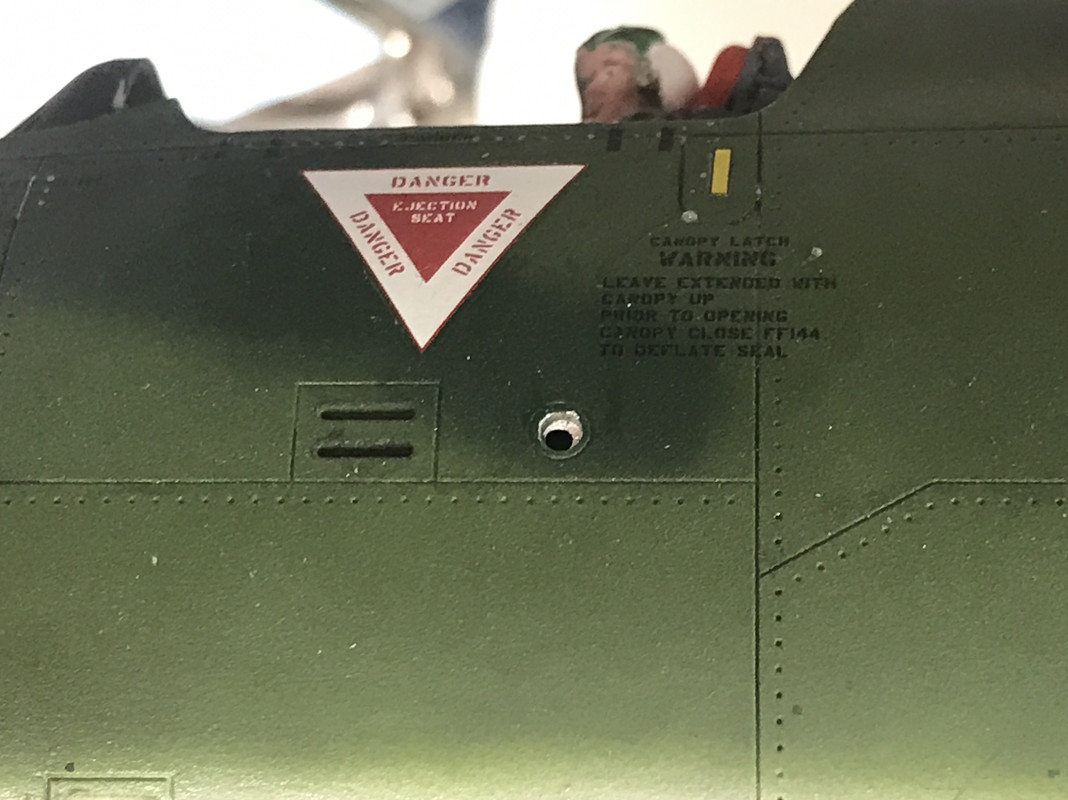
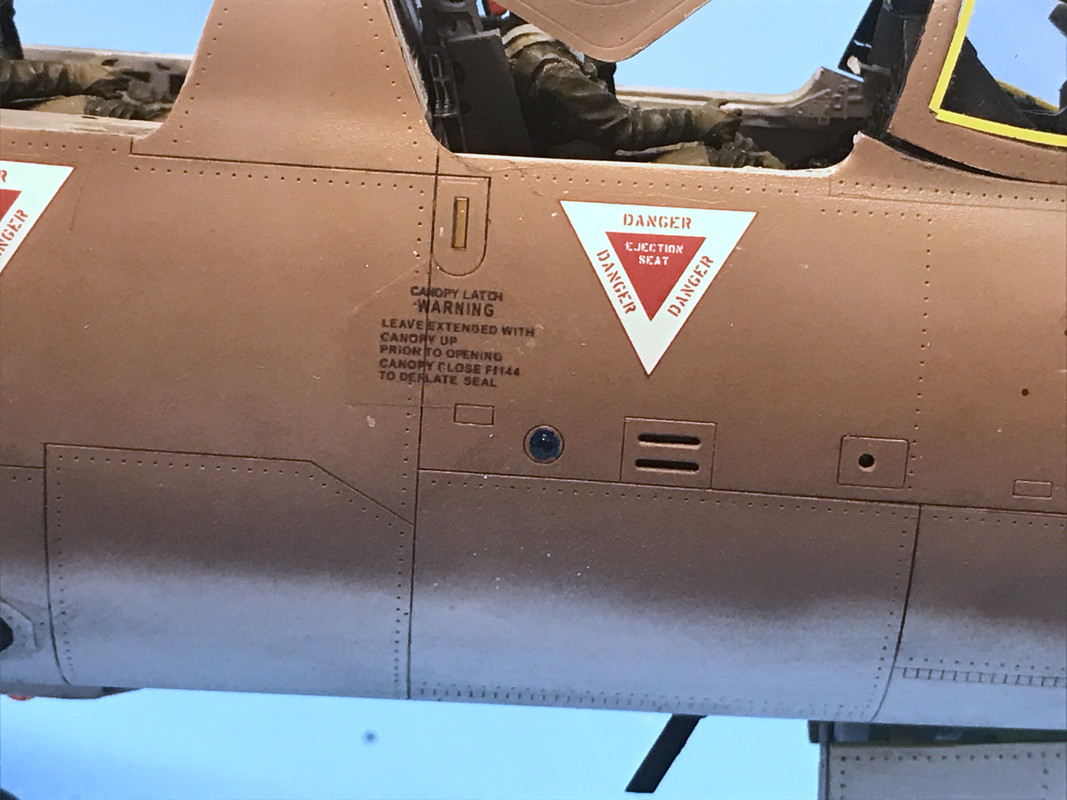
I had resisted getting Bondic thinking it was a bit of a gimmick, but I rely on it for all kinds of interesting modeling uses.
On another topic, I've been getting some things 3D printed at outside sources. These jobs have generally cost me about $40 each for some very small stuff that I didn't want to or have the skills to create myself. But the Filament Additive Machines (FAM) generally only get down to about 100 microns (a 1/10 of a millimeter) which at 1:32 and 1:48 scales show up badly. You need to have them printed on an optical resin machine. These traditionally are very expensive, starting at about $3k and then going up... way up. Then I read about units that use UV LEDs instead of lasers and are being sold on Amazon for under $400, and they produce 10 micron layers. These work very well for model work.
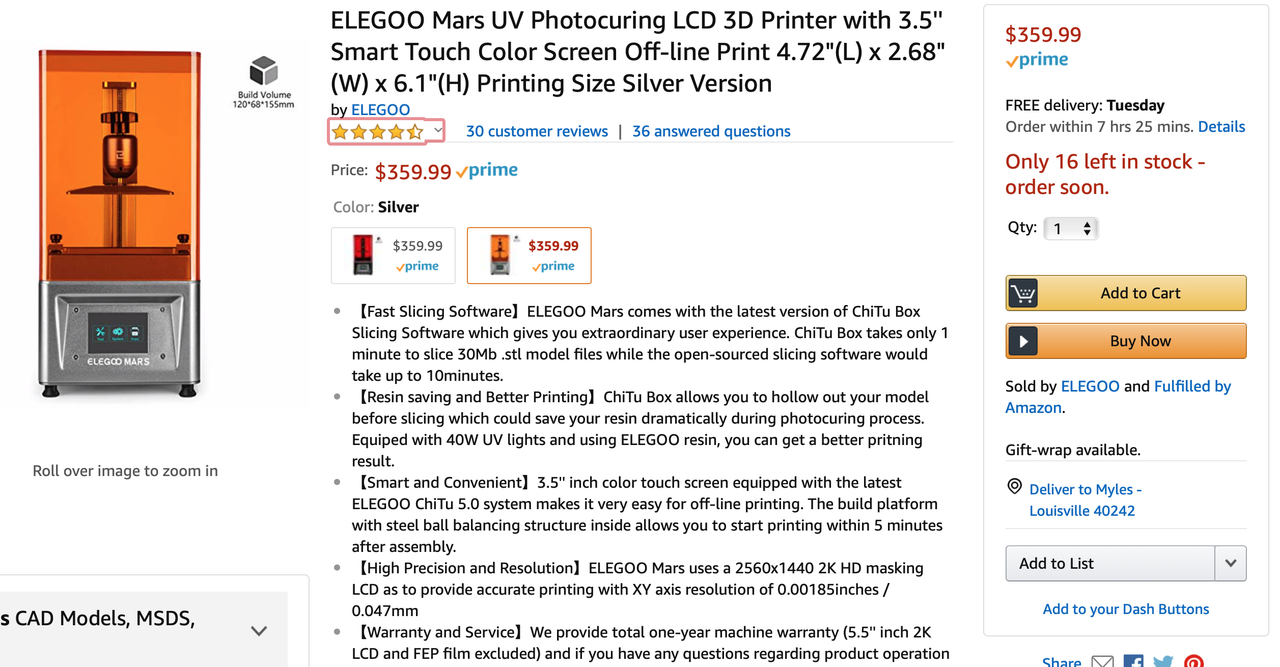
The unit above is Chinese, but most of the lower price 3D are. It uses a resin that's water soluble until cured and the models produced generally need more exposure to UV to become really solid. Amazon sells another UV that can be used to harden the models.
At this price point, if I do 10 parts, I pay for it. Furthermore, even though the resin is pricy ($40 - $80 per bottle) after downloading their slicing software, I ran the part that I just had done by Shapeways, and it ended up usng $0.72 worth of resin. Resin that isn't directly cured by the UV scan can be returned to the bottle and re-used.
I'm seriously considering this for a my father's day/Birthday present to me. My son, last night, said "For $360 what's the risk?" Exactly!