Thanks guys and for following along. Today I worked from after 1:00 to about 4:45. Of that three hours and 45 minutes, I'll bet I spent at least one hour of it on my hands and knees looking for lost parts. And that wasn't all. I needed to move the table (a drawing board screwed to an IKEA stool I made in Germany when living there) and knocked off a bottle of Tamiya Clear Smoke paint. Usually they bounce. This one fractured in half spilling about half of the paint onto the floor. My shop floor has been spilled on so many times it's looking like a Jackson Pollack painting. I emptied one of my smaller bottles used for the airbrush and cleaned it in the ultrasonic cleaner so I could salvage the remaining paint. The bottle came out spotless. Then I dropped it while wiping out the insides with a rag and it broke into smitereens. Then I found an old Tamiya Thinner bottle. I did the same drill again and this time didn't break anything else.
Speaking about full-size armor. From the Summer between freshman and sophmore years until my first year teaching I had the pleasure to work as a mechanical technician at American Electronic Labs (AEL). They manufactured military electronic countermeasure gear. I started as a rank amatuer and eventually was making experienced wages. It was great experience for me. One of the coolest things was the APC project. They received 15 brand new M-113 APCs into which they were going to create mobil jamming vehicles. It was a $4.5mm (1964 dollars) project and took three years to complete. The tanks were built by FMC. They were fully equipped regular M-113s. They even had the 50 cal in a crate inside. But this was not what AEL needed. They had to be completely stripped down to their bare aluminum. Yes! M-113s were made of welded 2" aluminum. So all the seats, hardware, everything had to be removed. This also meant air-chiseling all the little attachment brackets that line the walls for soldiers' gear.
It was a hot summer and the boss gave me the air chisel and told me to start breaking the welds to remove them. When the chisel hit the weld the entire vehicle rang like a bell and I was inside! It was intolerable. I told the boss this was not a job I was willing to do. He said okay and got a bunch of poor souls on manpower roles to do the work via per diem. We did provide jet muffs for them so they wouldn't go deaf. The boss was one of the best supervisors I ever worked for, and the team were some of the most clever and resourceful mechanical craftsman I've ever known. They could do absolutely anything.
But the best part of the gig was running the tanks. These tanks did not have any preservative in them so they needed to be "exercised" on a regular basis. AEL built a test track in the back lot and we all took turns driving them. They were very easy to handle and the steering levers is very intuitive. I got to do it once during my tenure.
The project was completed after my fourth summer. When I returned in summer 1968, the APCs were back. What happened? It turned out that they were so comprehensive and complex that they couldn't train operators in the 10 week cycle the military had. So they gave them back. We stripped out all the gear and AEL was using them in subsets mounted in standard equipment enclosures that would be mounted on trucks.
Okay, enough story telling. I got the upper turret painted and assembled and made a big dent in the gun. The gun body has 24 parts itself, not counting the 30 cal coax gun. There is a connecting link that was the elevating linkage, that if you include it, the gun will not elevate. I left it out since I want it to be movable. There are poly caps in the gun trunion to permit rotation so why not take advantage of it.
I based painted the white on the upper turret parts before assmbling them. It made detail painting much easier.
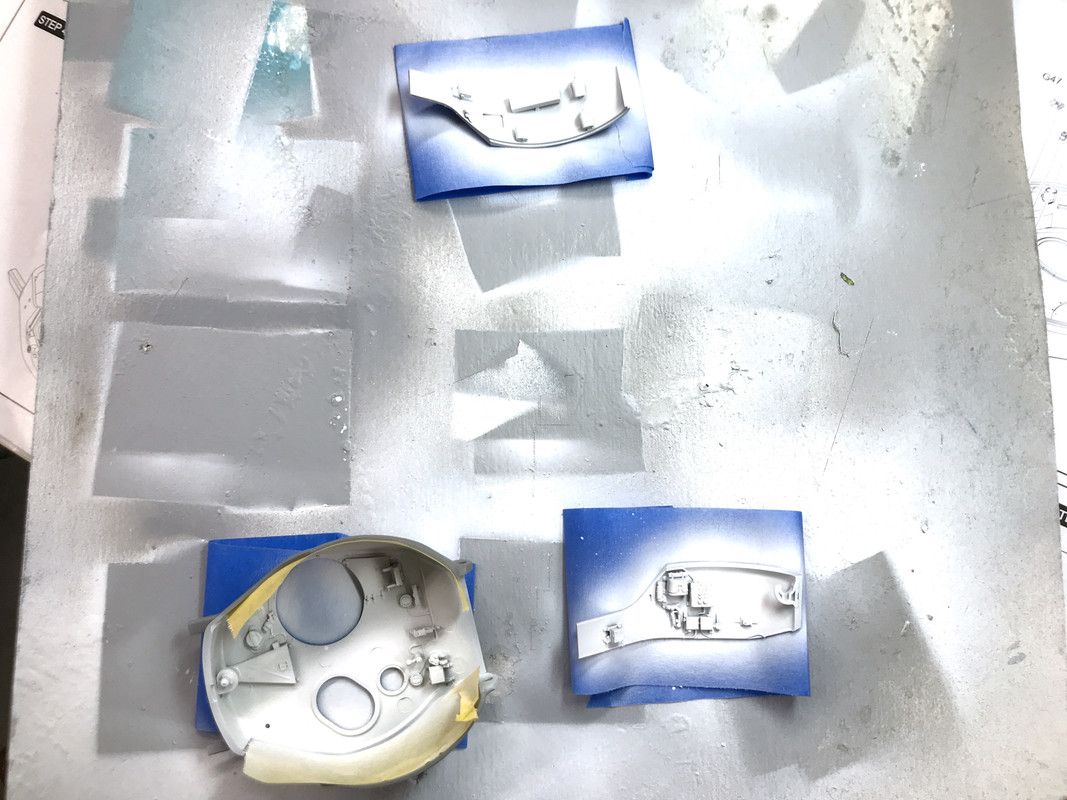
I picked out all the little boxes and things. There are three canteens and a binocular box that I paint kahki. The canteen caps are semi-gloss black. I picked out the electrical wiring with better luck than I did on the hull.
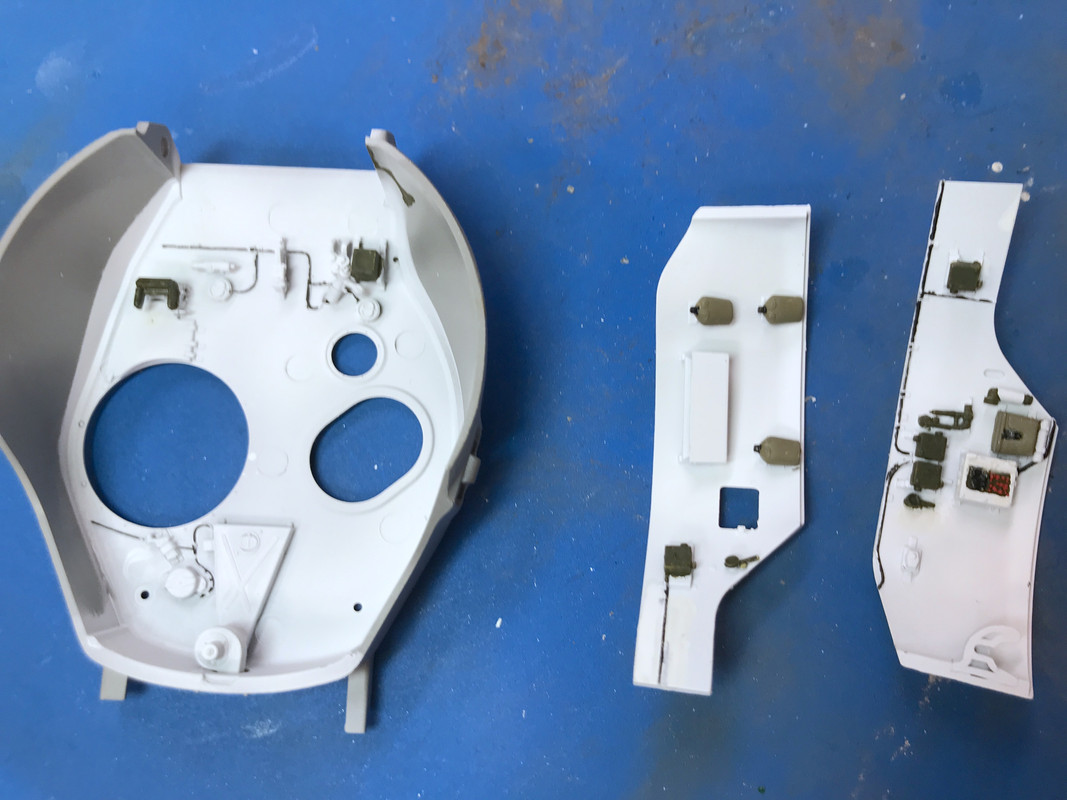
I was surpised that the commander's fixed periscope was not a clear part like the driver and asst driver's. I picked out the lenses of the overhead light fixtures with the Molotow Chrome Pen.
I glued the side panels in with tube cement, again since it gives longer working time for large surfaces. I did a lot of back painting on all these little bits so everything came out clean.
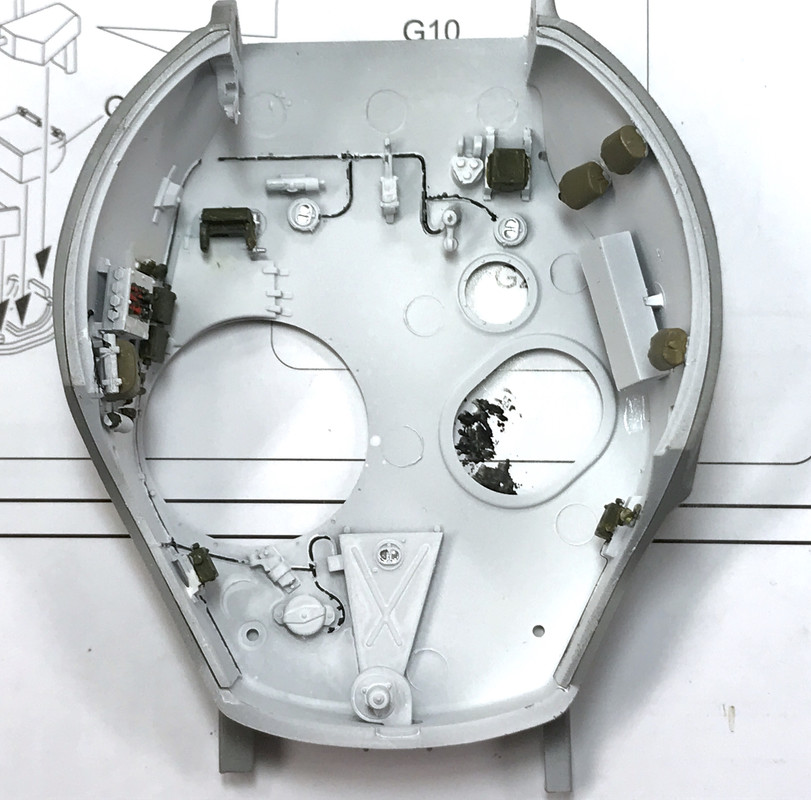
Onto the main gun. This is an enormously complex assembly. Many are delicate and require a lot of location testing to ensure their in the right spot. The recoil mechanism does work! Part G35 is this link I mentioned in the prolog. It connects to that clevis on the roof, but doing so would lock the gun since the rest of the linkage is non-working. I was looking forward to the gun build since I've always had a fascination with artillery pieces.
When in Junior High School, the amazing Franklin Institute in Philly had a fully working model of, what looked like, a 5" deck gun from the WW1 era. It even had a step-thread break modeled. WW2 High Angle 5" guns had sliding wedge breach blocks not step thread. That model impressed me so that my friend and I found plans for it in the Institute's library. We had delusions of grandeur. We were going to build it as shop project. Of course we couldn't do it and the project never got out of the planning stage, but my interest remained. Only recently I found just how tricky it is to machine a step-thread breach. It's done on a special lathe that can engage the cutter for the short distances of each thread on each step. It's not something a kid's going to do in a junior high metal shop.
Here's a perfect example of a step-thread breach. This is the center 16" gun of number 2 turret of the USS New Jersey Iowa-Class BB. Very impressive indeed! The threads themselves do not seal against the blast pressure. That the job of the "Mushroom", the bulge in the breach plug center. The threads apply the tremendous pressure to hold the mushroom in place. As an aside (this post is full of asides...) if any of you ever saw Steven Segal's "Under Siege", the guns in that turret weren't real. Each Iowa gun was in its own "room". You can see the walls flanking the breach block. Each compartment is isolated from the other for obvious reasons. In the movie, the gun room was wide open. You can't make good movies in the rear Iowa turrets.
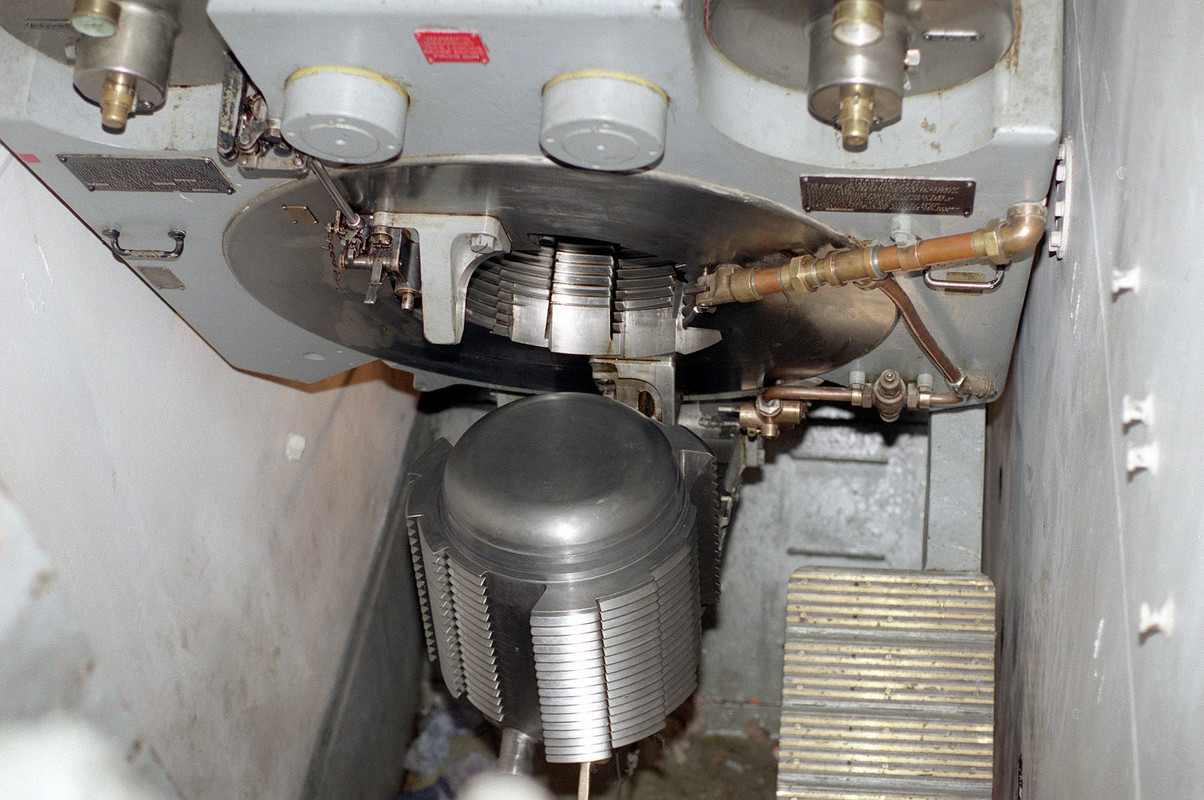
Tank guns are not step-thread breaches. They are sliding block affairs and the breach block iteself is in two parts for the model. If any other model would use one part for something, Ryefield is going to use three. This is the gun top. In the foreground is the optical sighting system. 76W Sherman's had a stabilized gun system and were the only one during the War.
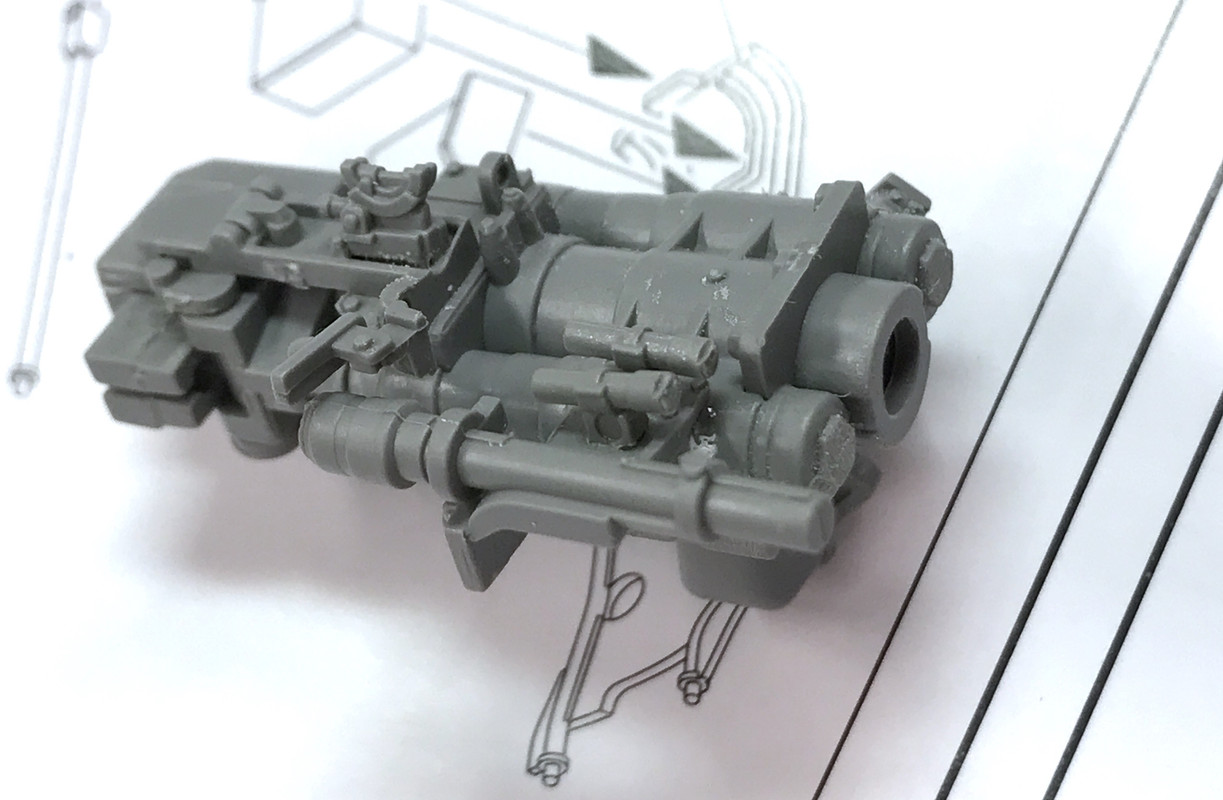
Here's the bottom view.
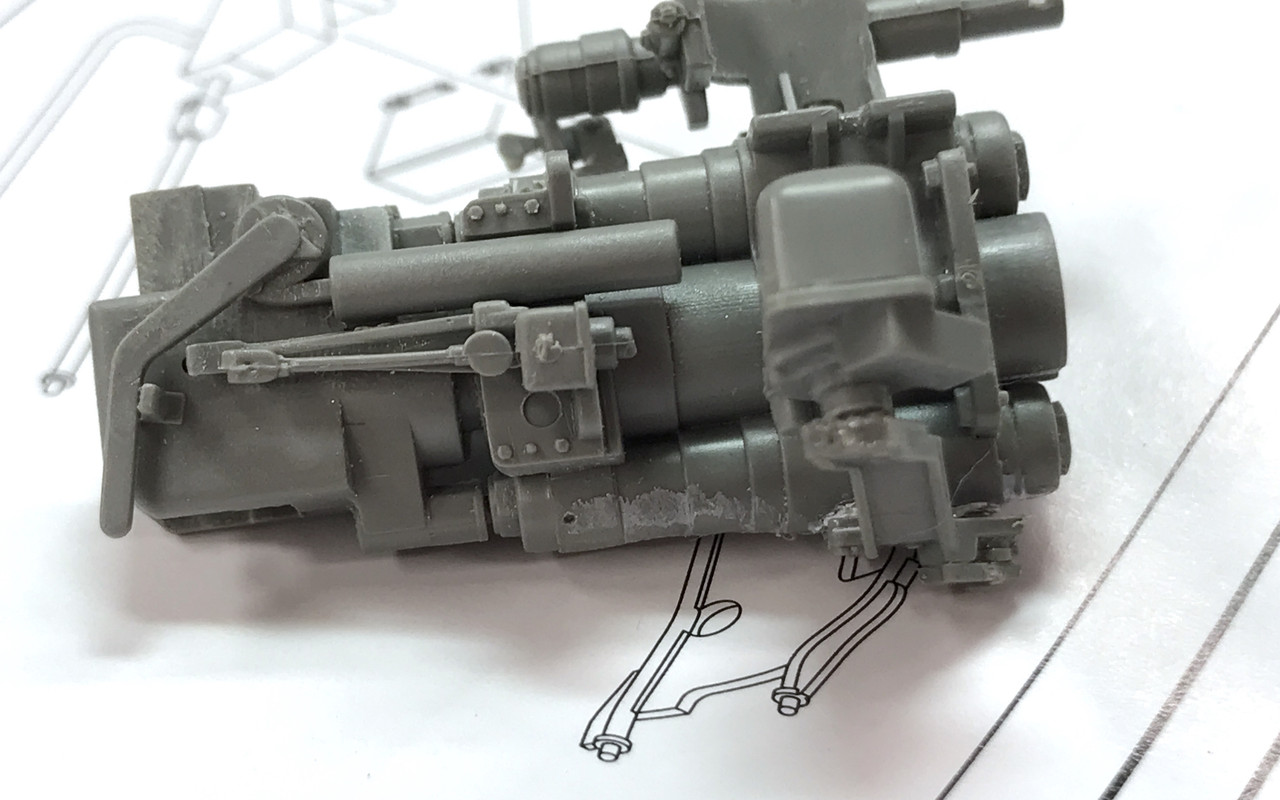
And here's a view of the breach itself.
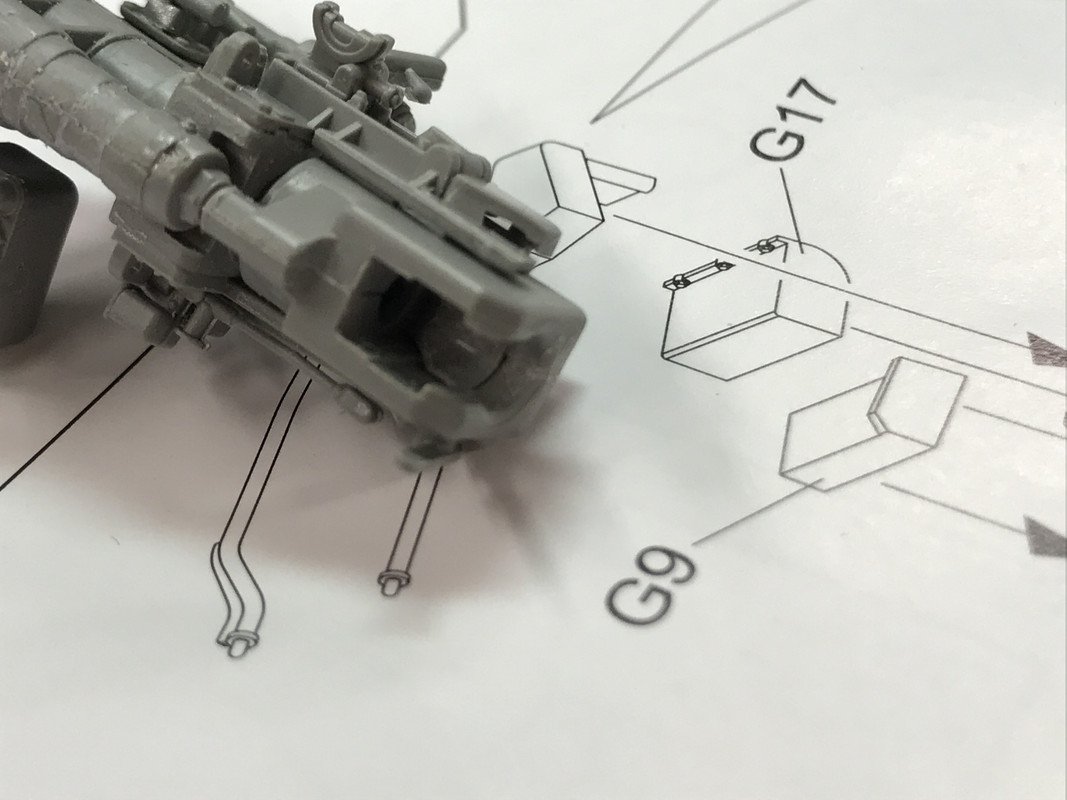
The Manlet went on next with its polycaps. The 30 cal coax gun is also built at this point. Again, it's a delicate, very detailed assembly. When I took this picture I hadn't glued on a diminuitive plate that connects the two prongs of the gun's mount to the mantlet cover. I had it in place, went to adjust it and launched it out of the tweezers. This was a high-velocity launch off to the right and I spent 20 minutes looking for it. Ended up making one which I didn't finish by the end of the session. I found a lot of parts (treads) that were lost days ago. They came out of the dimensional rift when this small part entered.
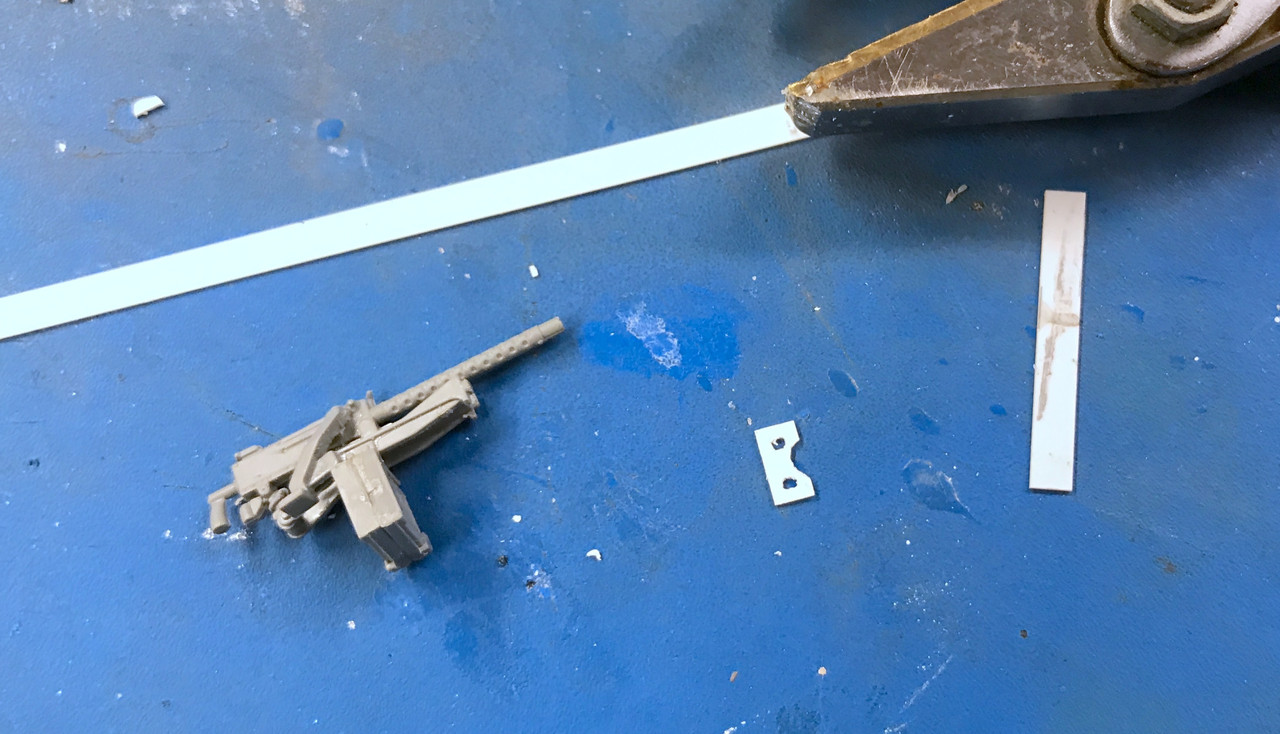
Hopefully, this styrene will be strong enough to do the job. The Ryefield styrene is pretty hard an tough. The Evergreen styrene is not. With all the fine parts I really haven't broken many. I've dropped and searched for many more than I've broken.
I now have a MiniArt WW2 US Army Tank Crew to go along with this model. Trouble is, they're all in poses outside of the tank. I wanted a driver and asst. driver for inside. I may have to do some kit bashing to get them to work. I looked at the Tamiya set, but all of the insde folks were half-bodies meant for tanks without interiors.
Tomorrow the guns get painted and then mounted into the upper turret.