Lads...
I've been laboring away at the build but haven't taken many photos along the way... And some that I have taken have gone missing in the nether world of my old hard drive.
I'll pick up here with my progress and get the build log up to snuff.
Firstly, I decided that my original location for the main sheet sheave holes was too far forward. They really should've been positioned aft a bit - centered in the gap between the main and mizzen shrouds. So I filled in the first version and laid in a new row of inner planking with rivet detail, etc. and painted it all to match. Then I redid the sheave holes and moved the cleat.
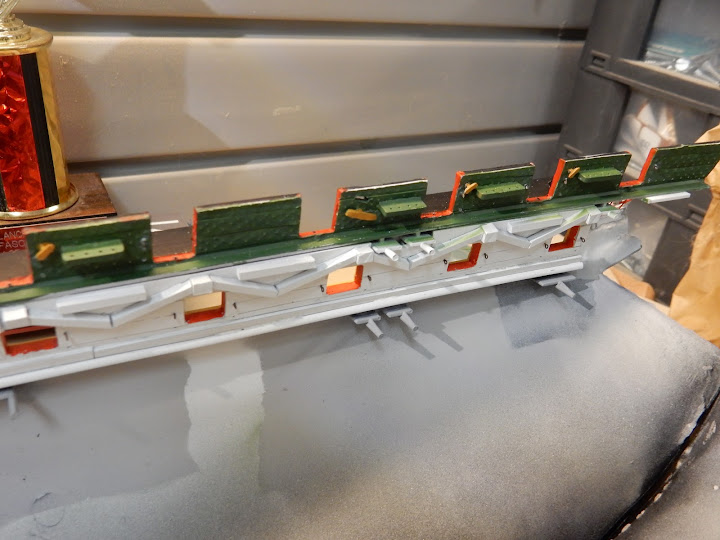
You'll notice the addition of more cleats along the bulwark. My understanding is that halyards were NOT tied off to pin rails... Those tie off to cleats or bollards at the ends of the pin rails. I used the guidance from Olof Eriksen to position appropriate cleats to tie off the various halyards on either port or starboard. The cleats were quickly fashioned from Styrene I-Beams from Evergreen using the handy Chopper:
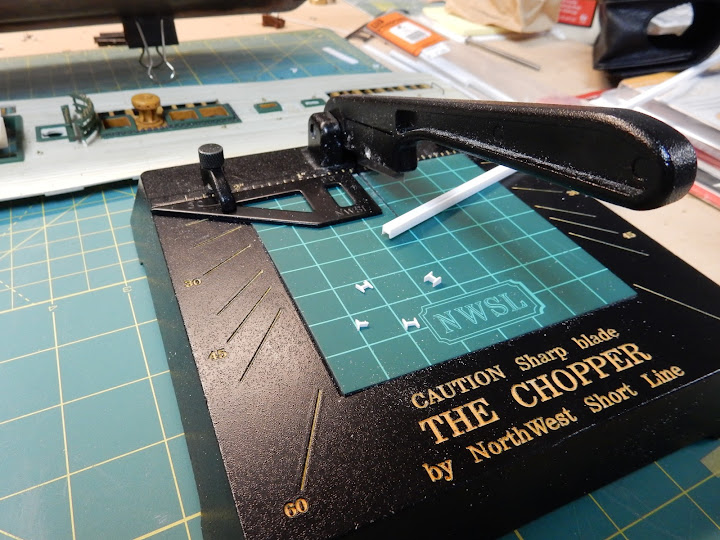
Once sliced off of the stock piece, one end would be snipped and the remainder filed to shape and glued into a hole drilled almost thru the bulwark to maximize the surface area for holding power when glued. After the glue dried, I came back and painted with wood brown.
Deadeyes:
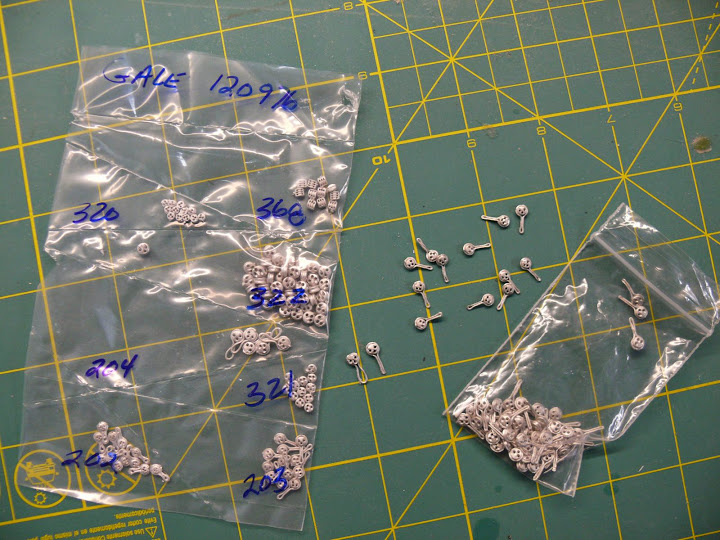
I've got the deadeyes all primed and painted to resemble wood with iron strops and light tarring (just smeared them with a dark wash). I wanted them to be wood-like- not entirely black.
I've reamed out the holes in the channels and test fitted the initial batch on the fore channel.
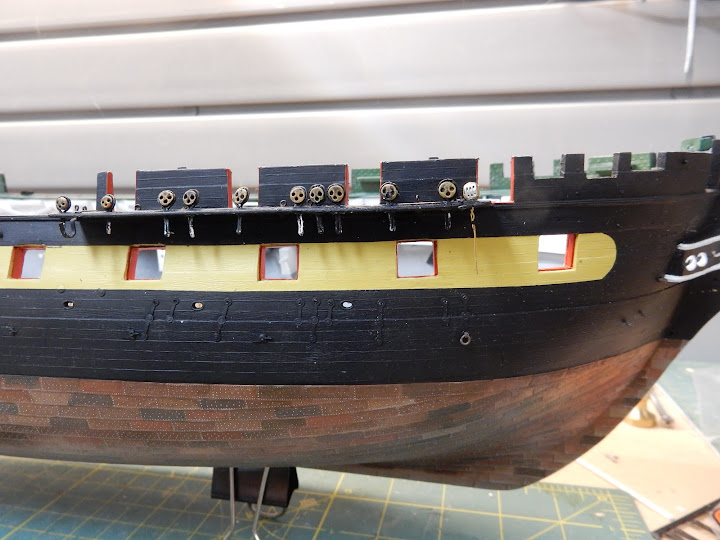
You'll also notice that the forward most shroud will lead to a triple block instead of a standard deadeye. (I've got a test version mocked up for now and should have something in place after I put the solder iron to work on the wire strops.)
The Hull model in the Peabody Essex museum clearly shows the triple blocks fitted on the forward shrouds on the fore and main channels. The mizzen does NOT have this block - just the standard deadeye.

This contradicts the guidance from Larry Arnot in the BlueJacket kit manual, but Mr. Eriksen confirms this approach against the Brady Naval Apprentice Kedge Anchor (Ed. 1841) Apparently these first shrouds would be eased or tightened as the ship changed tacks. As such, Eriksen refers to these as "Swifters" - although that term is a bit ambiguous to me. I know, for example, that the aft most shrouds on a channel were often referred to as the "Swifters" - they are not paired with another shroud when rigged and seem to have evolved from some sort of backstay in an earlier time.
All part of the mysteries of rigging as I venture forth.
Sorry for the delayed update and thanks again for all the kind interest.
Evan