I spent almost an hour the other day writing the post with lots of images. Unfortunately, I let it sit too long before uploading and my computer reloaded the website "Because it takes too much memory" and the whole deal was lost. And now I have to do it again. I came up with a scheme to copy after writing so if anything happens, I just paste it and am good to go. This time I forgot to do that.
So here goes.
The reprinted ring gear was excellent, one slight area needing fixing. I fixed with Bondic. It fits the mounting ring on the frame well and the two can rotate. The real one has retaining clips that grip under the training gear and I'm going to duplicate so the turret will be positionable. I found that the Training Buffer interfered with the ribs on the stand, I surgically removed the offending material. I found another drawing of the buffer and it looks like the back is relieved for the same reason.
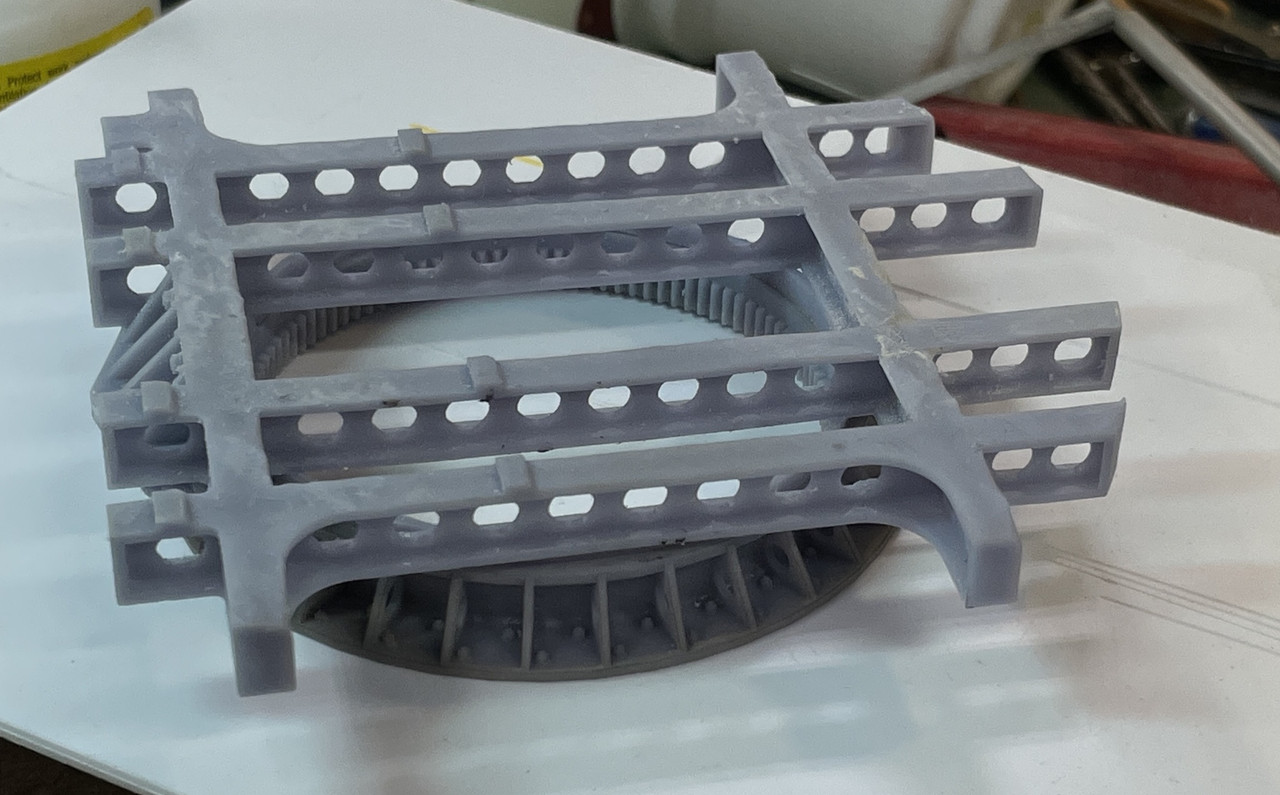
The mod: I also replaced the printed plungers with steel. One didn't form right and after replacing it, I did the other to match.
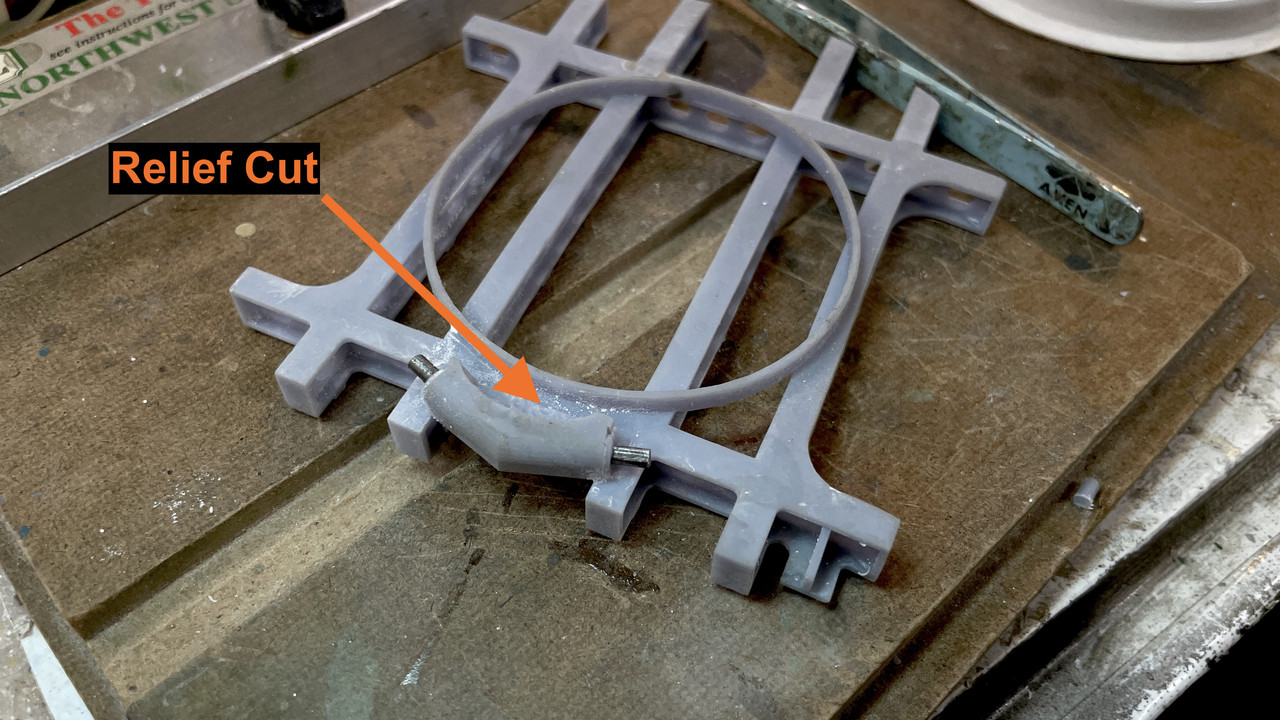
The gun mounts printed well. I always make more than I need and one set had a fatal defect. Didn't matter, I had three more and only need two. As printed off the machine.
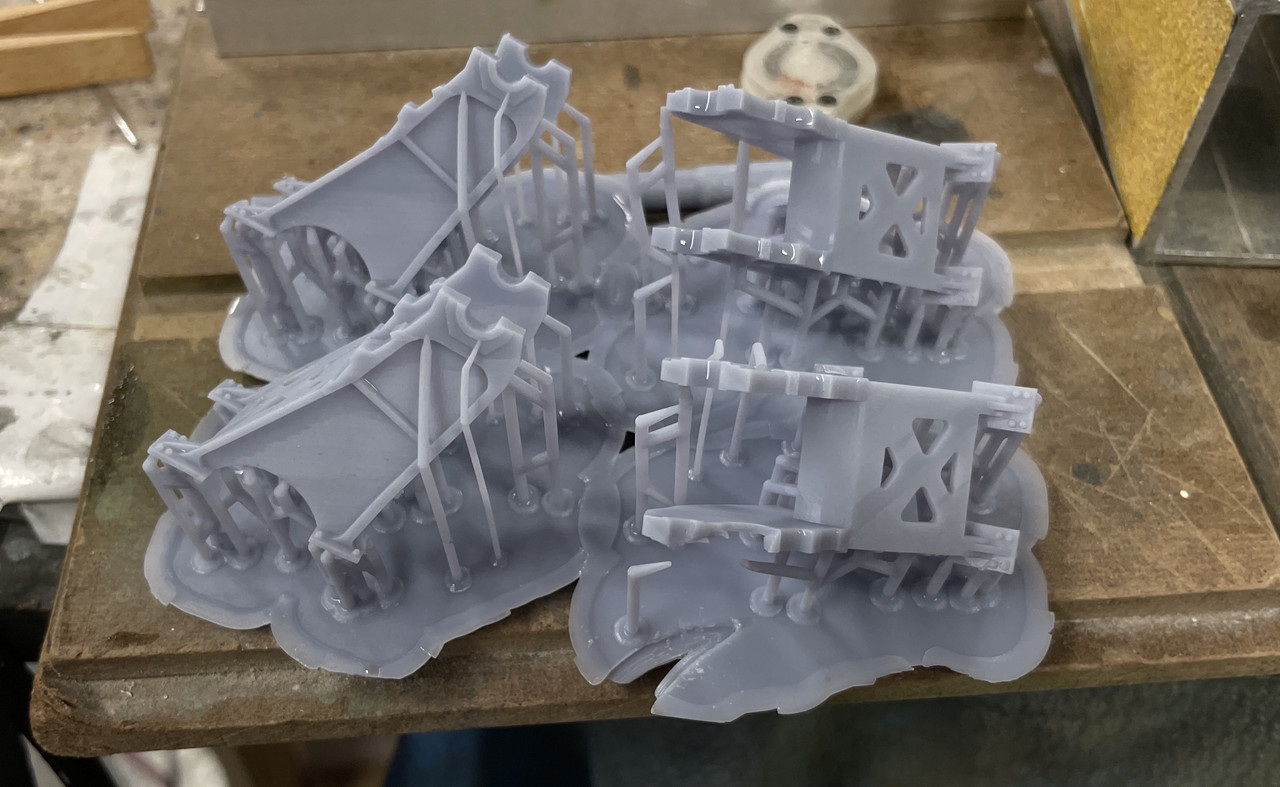
Finished set: Not glued, just set in place.
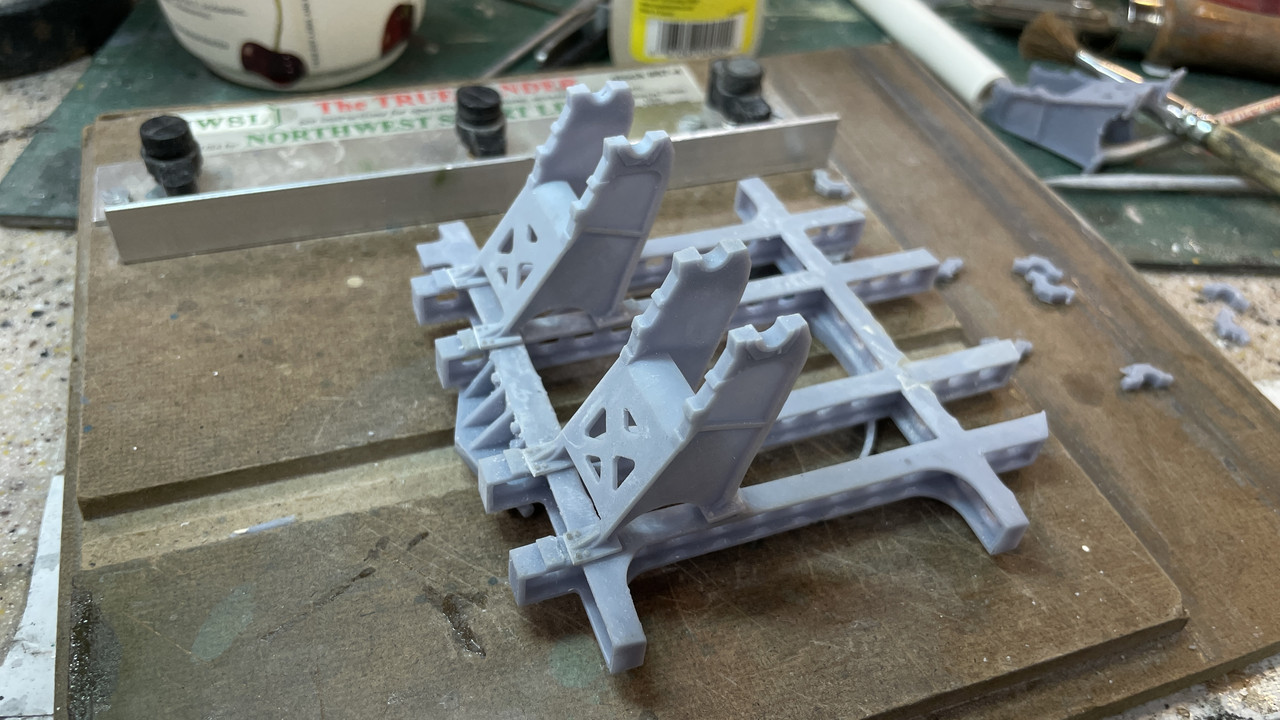
Printed a gaggle of trunnion caps. I erred. I put two bolts on each side. There is only one... Not going to worry about it.
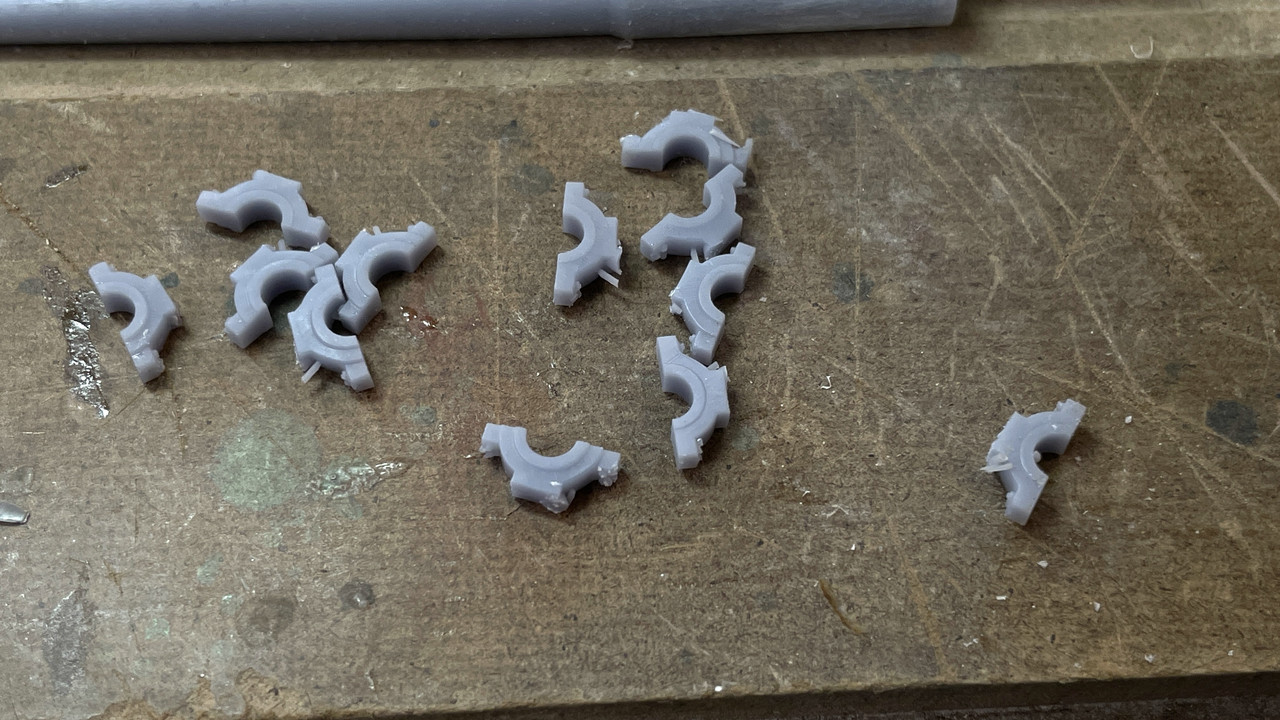
Here's the caps placed on the mount. Again... not glued. Can't do that until the guns are in place.
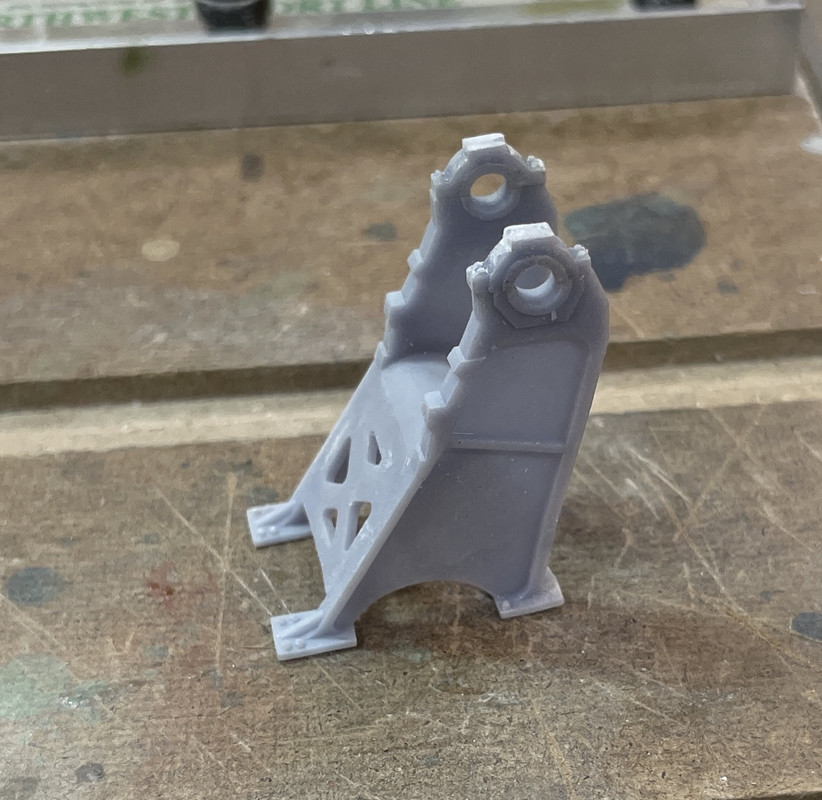
Here's the one that failed. And you can see why. That support failed. When the support fails it usually leads to a local or catastrophic failure depending on how strategic the support is.
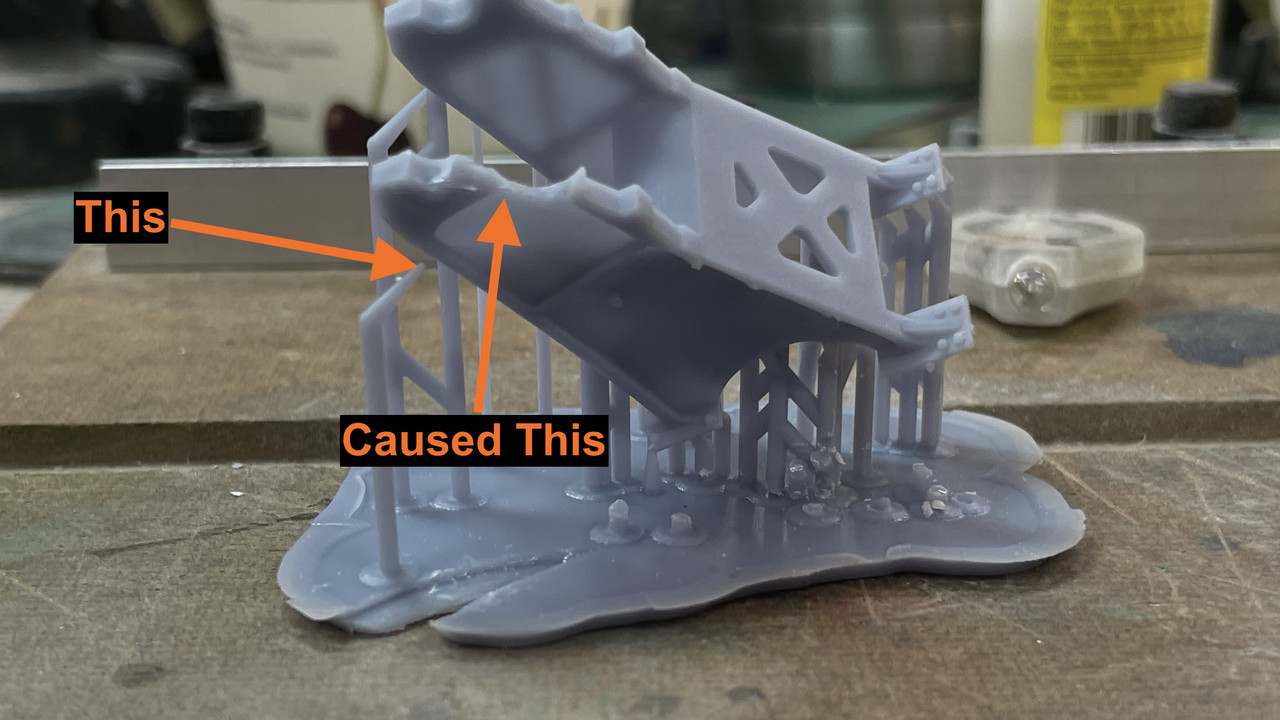
I also printed successfully, three out of four Training Worm/pinion assemblies. Only need one. This one was also a support failure, but of the more catastrophic variety. It left the partially formed part stuck to the FEP film at the vat's bottom. The new version of Elegoo's FEP film is very forgiving. Stuck parts pop off with no damage to the film. I can run for months without having to replace the film ... a 20 minute job. Looks like something that didn't make it through the Star Trek transporter too well...
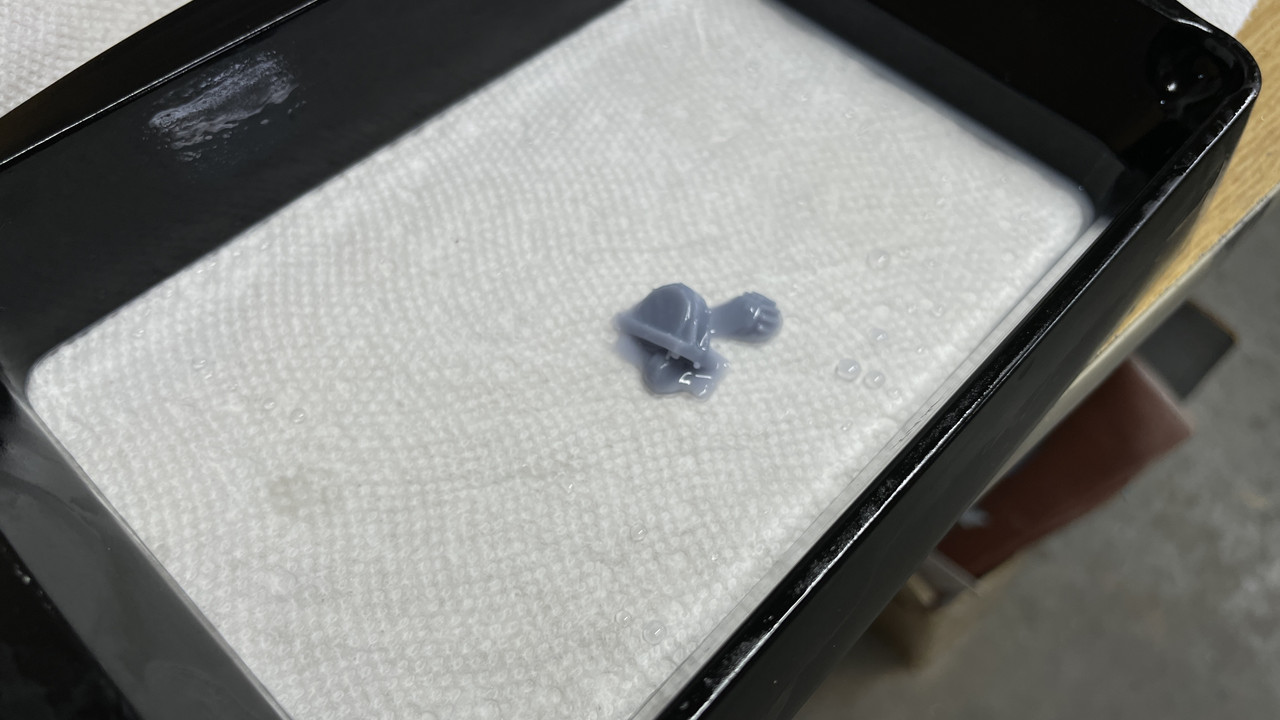
Here are the good ones. Even among these there are some that are better than others. Always make more than you need!
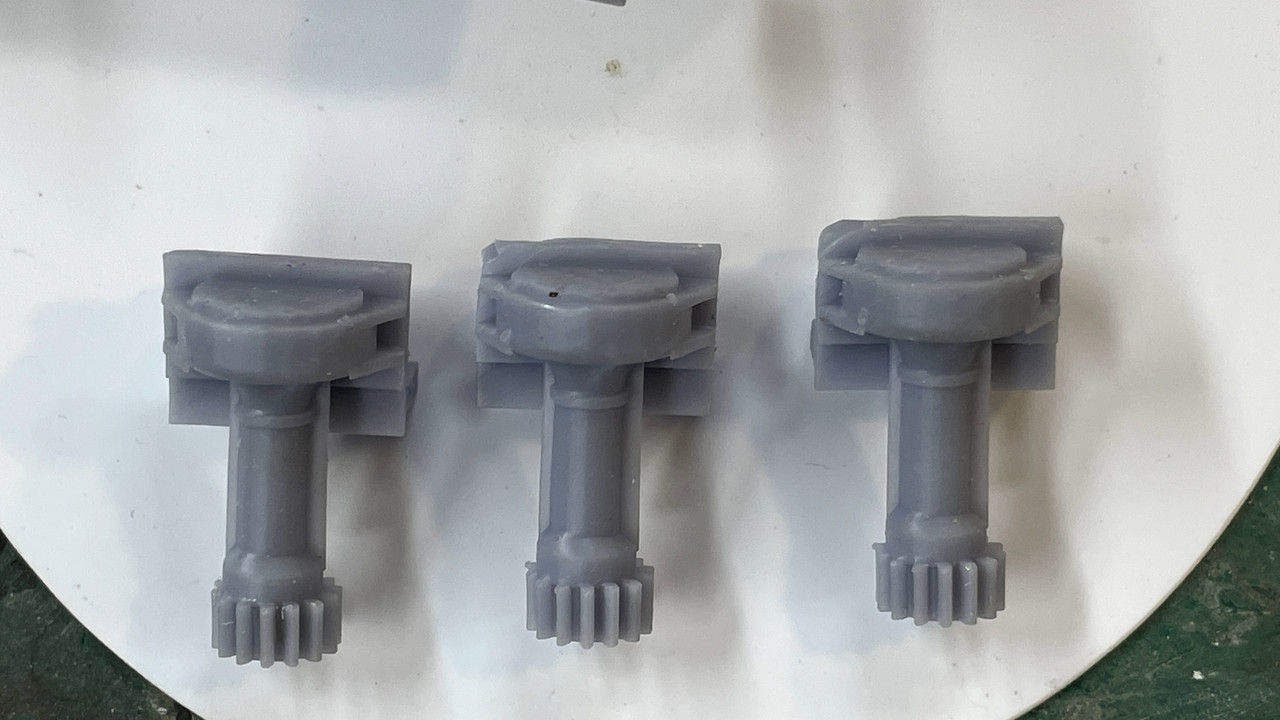
Here's the trial fit top view. Part has NOT YET been finish sanded and you can see by the support marks on the top.
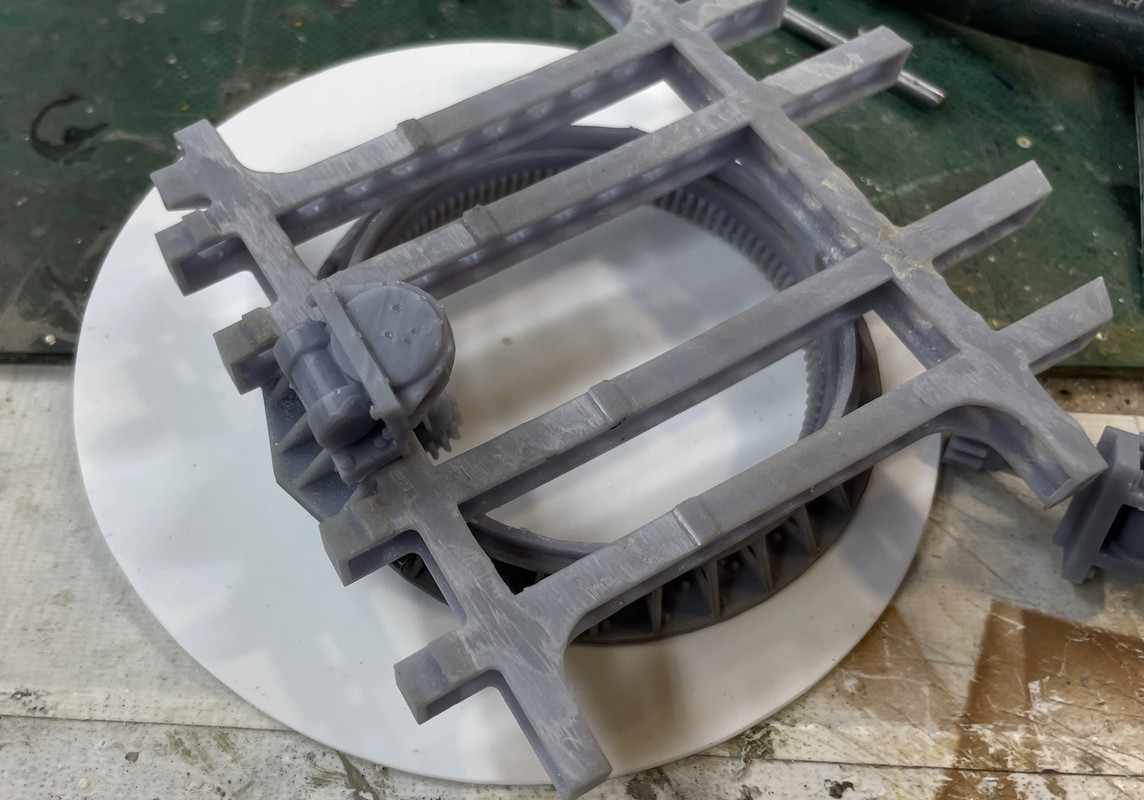
And the bottom view showing the pinion meshed with the training gear.
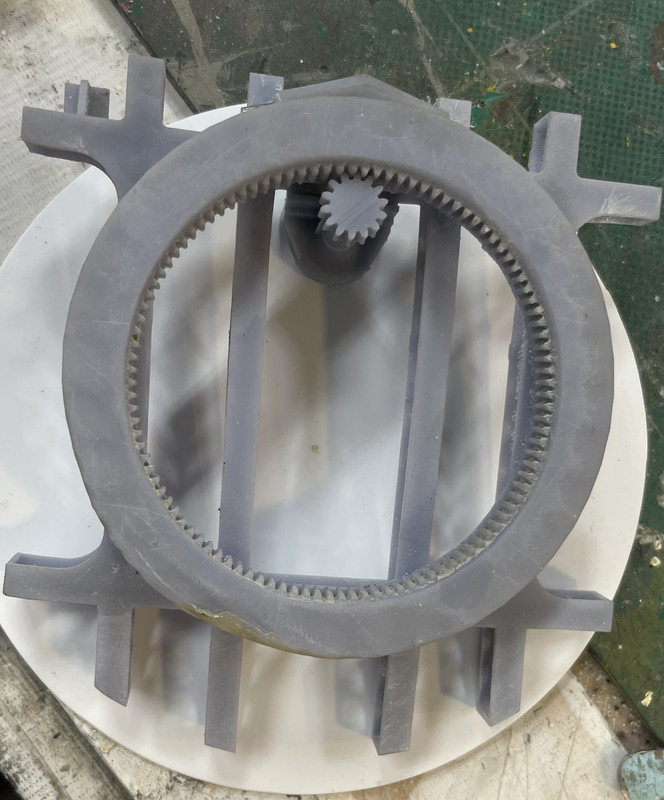
That's all the parts that are drawn to the point of being able to print. There's a whole lot more going on in the design department. I finished the gun shield and elevating sector gear, but both have to wait until the gun proper is finished. There are some brackets that engage in the gun that can't be finalized until gun is done. I also started delineating the armor housing with the curved back plate. I'm going print the hatches with their hinging, but the curved wall will be 0.040" styrene. Technically, the armor on the this ship's secondary batteries are 2.5" which is 0.050" in scale. I may laminate 0.040 and 0.010 to make fifty. Laminating also helps maintain the curvature. I had to extrapolate the lateral position of the hatchways due to the curvature of the image. I then flattened the curved piece using SU's "UNWRAP & FLATTEN" facility.
The gear teeth are finer on the prototype, but at 1:48, if they're too fine, you won't see them.
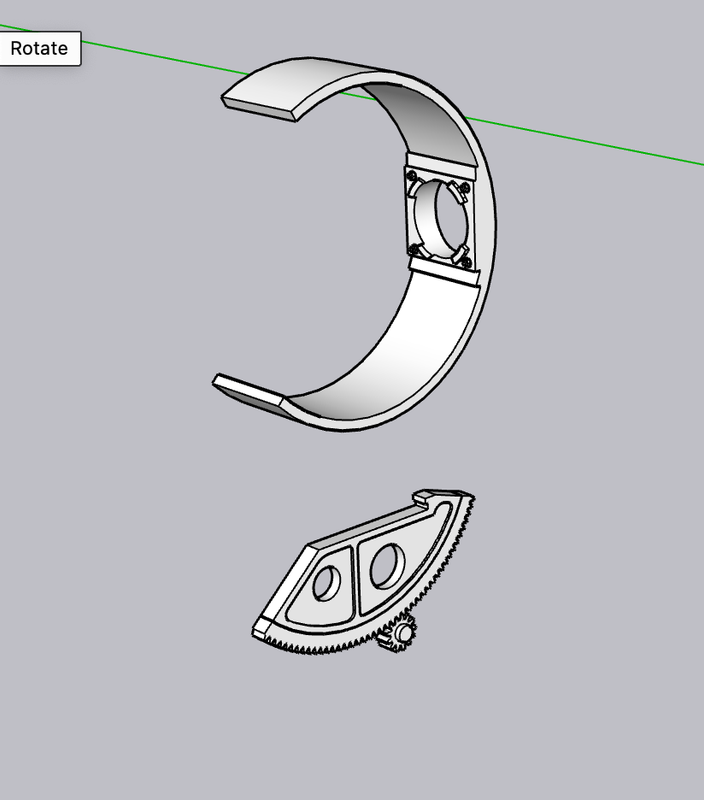
Here's some WIP shots of the rear panel. I'm not sure if the hatch is curved. It too a while to create the curve using a copy of the wall section to cut the inner and outer faces. If flat, that's much easier to do in styren. In addition to the crew hatch, there are four others for the cartridge discharge chutes.
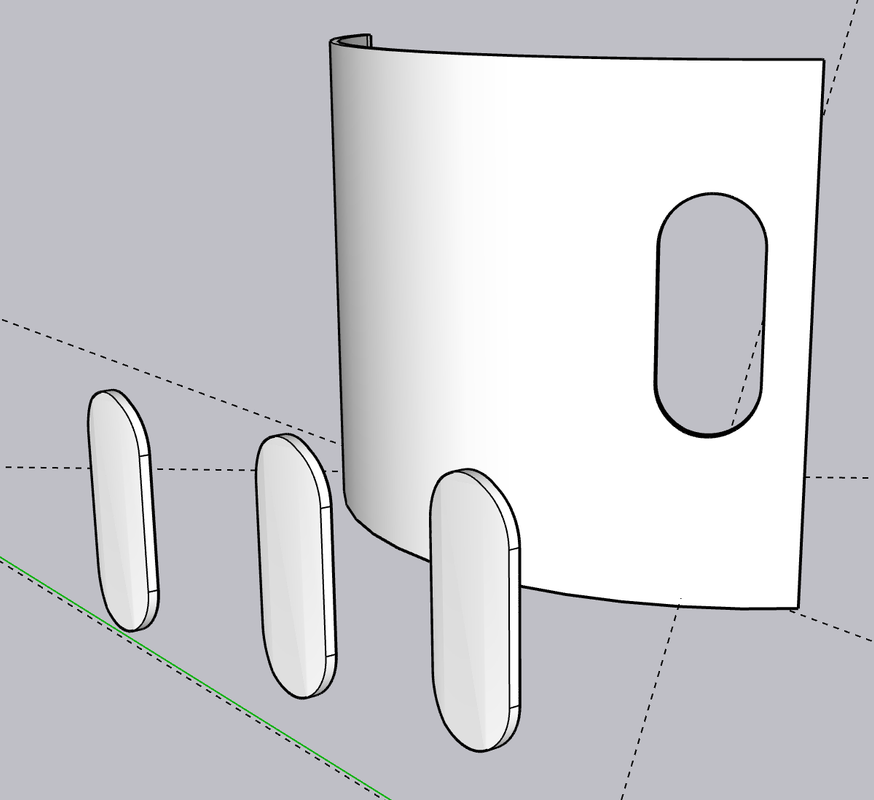
Here's the wall flattened as a test.
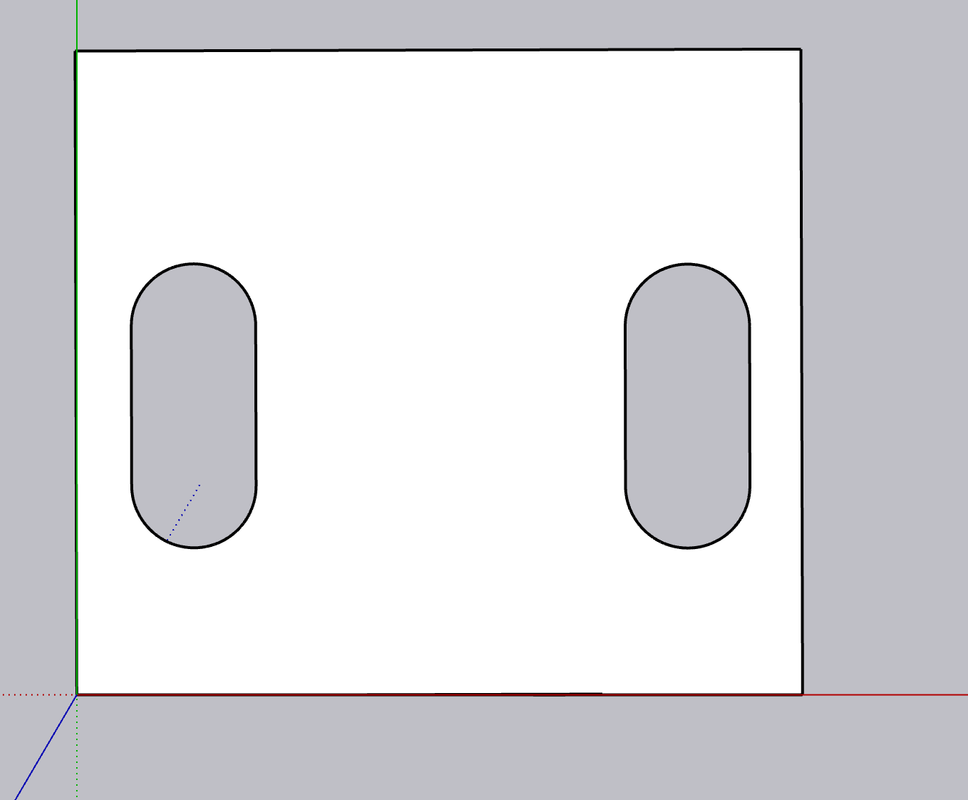
There are angle bars that attach all of armor panels to shape the gun house. I'm going to 3d print these with fasteners. My shape isn't exactly right as I've ssen on some video footage. Don't know how anal I'm going to be about it. The fastener pattern's probably not right also other than it's a combination of rivets and bolts.
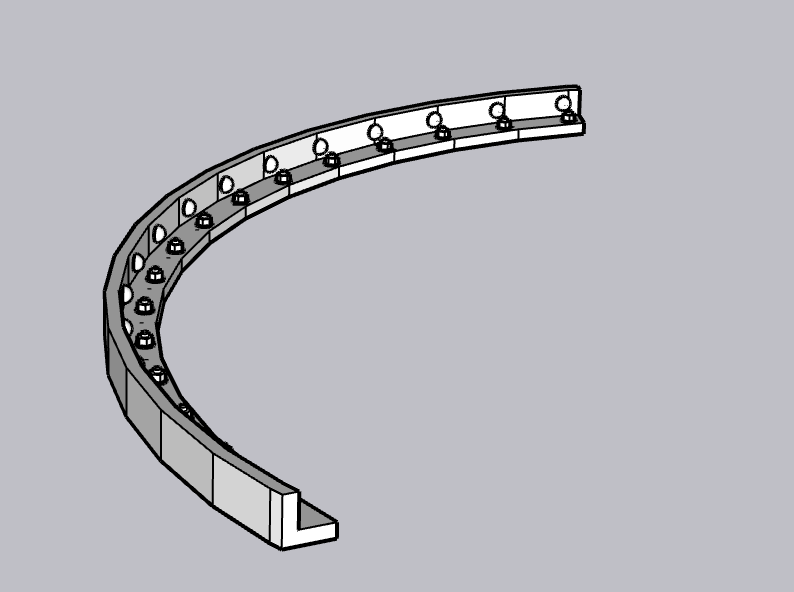
Here's the actual back do. I'll print the foot rungs too. Hatch looks flat. This is the lower discharge port. The six bolts to its left are those that are holding the housing to the longitudinal frame rail.
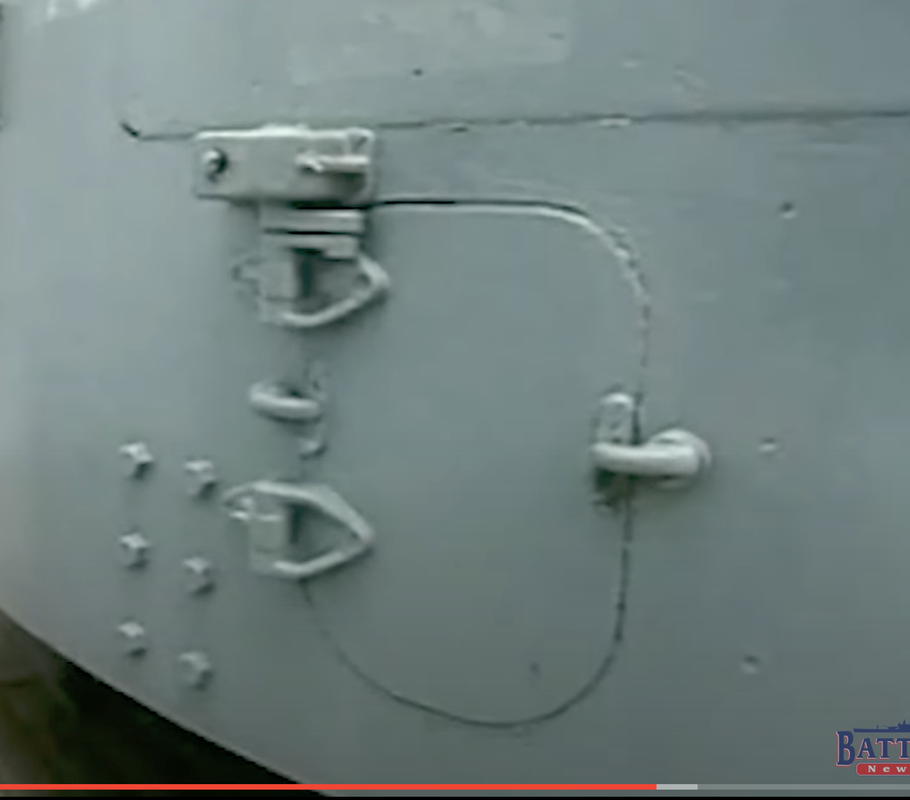
Now the gun. The geometry is a killer for me! I don't have any drawing of the parts separated, e.g., slide, housing, etc. I was very difficult for me to visualize just what parts move during recoil and what parts are fixed. When you watch videos of the guns firing, the recoil is so fast you can't stop it when recoiled. I suppost you could copy the video and do some frame-by-frame editing, but my bet is that it would highly blurred.
The real of the housing is curved in two directions... sort of part of sphere. I first had it curved only in the vertical direction, but realized it was wrong. To do compound curves in SU, I find it easiest to create a cutting too of the right shape and use it to shape the object. In this case, I created a segment of a sphere and placed it so it would remove the right amount of material.
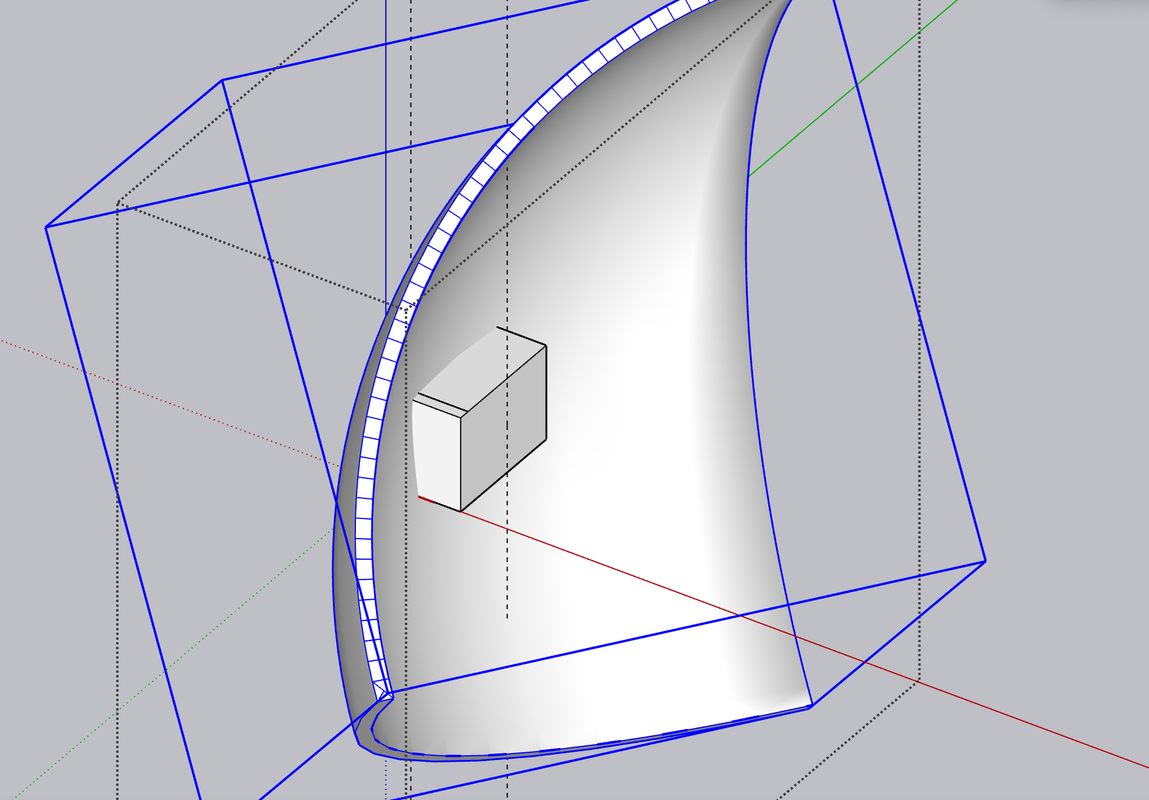
After cutting I grafted the part to the rear of the gun frame and it actually worked out. Still have lot of details to include and am constantly checking that the object is still solid and printable. Last night started working on the rammer hydaulics. I used one of my drawings a as guide only to find it was completely wrong for the reservoir. Found others that were accurate. I spent almost 8 hours yesterday just doing drawings. And I have hours and hours more to go. Taking the day off to go see Openheimer.
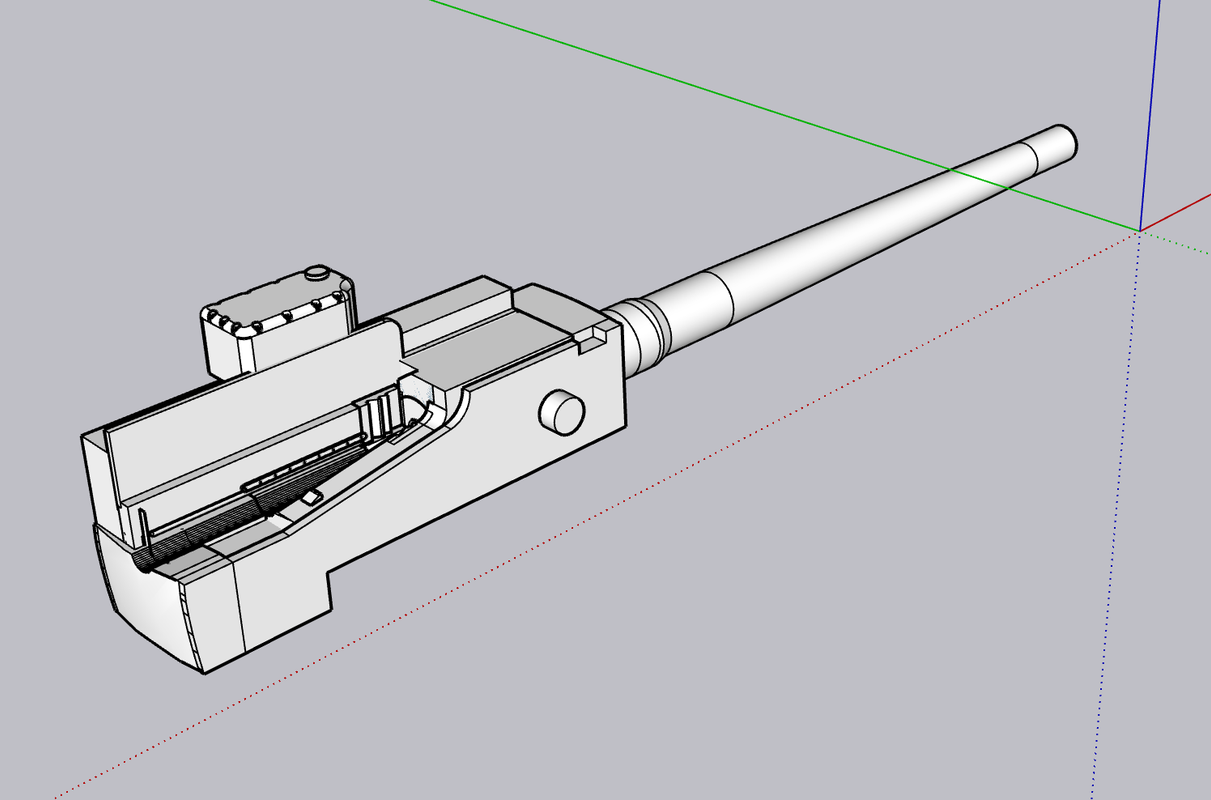