Thanks Edmund, Bill, and Rob. Rob, I appreciate that, this is my first try at chipping.
Update!
So you may recall that the entire front section of the tractor cab was formerly a clear piece with windows molded into it. I decided that masking the "clear" parts and painting the rest would result in the masks being on the windows for so long that they would never be clear again. Also, they were very thick, scratched to heck, and the windshiled wipers molded in place looked bigger than 1/35 prybars. SO... I dremeled out the windows and left the frames, and got this:
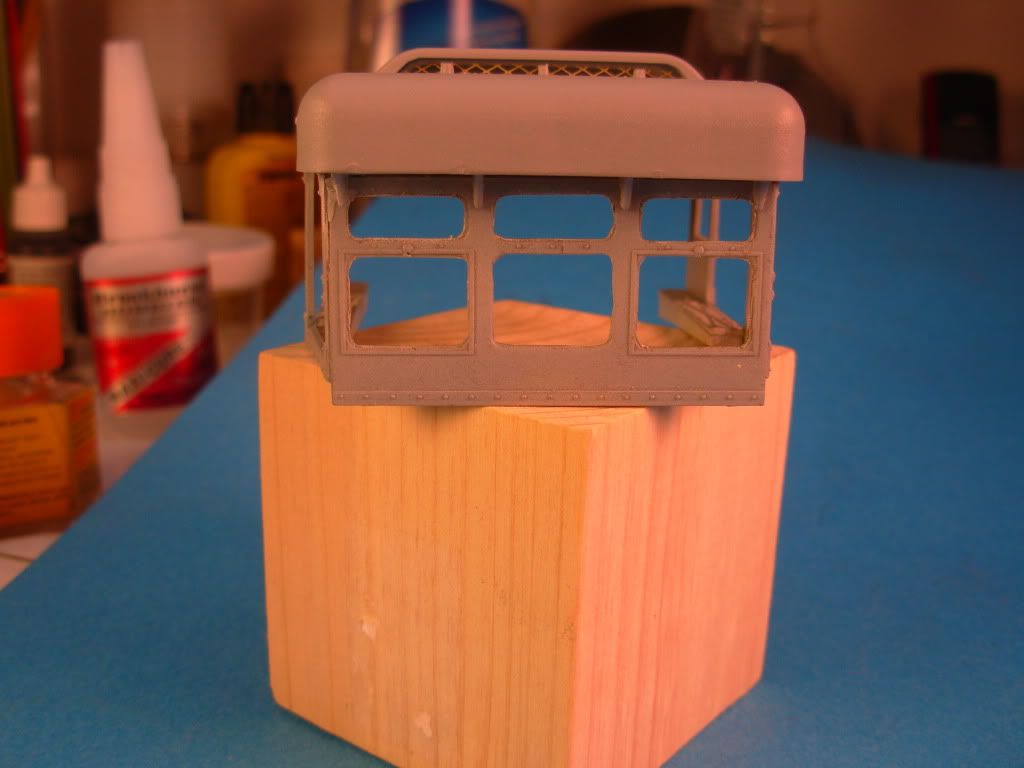
I planeed to simply make clear plastic windows and put them in after I paint it. My problem was I should have made a rubbing of hte windows before I got rid of them so I would have templtes to make the clear windows. I didn't, and had a mental block about the best way to go about getting properly sized windows.
Enter Schnobs, in the finest FInescale tradition, he suggested tracing the window openings onto some card stock, and trimming those to fit, then transferring that to some clear packaging for nice clear scale thickness glass.
SO I did:
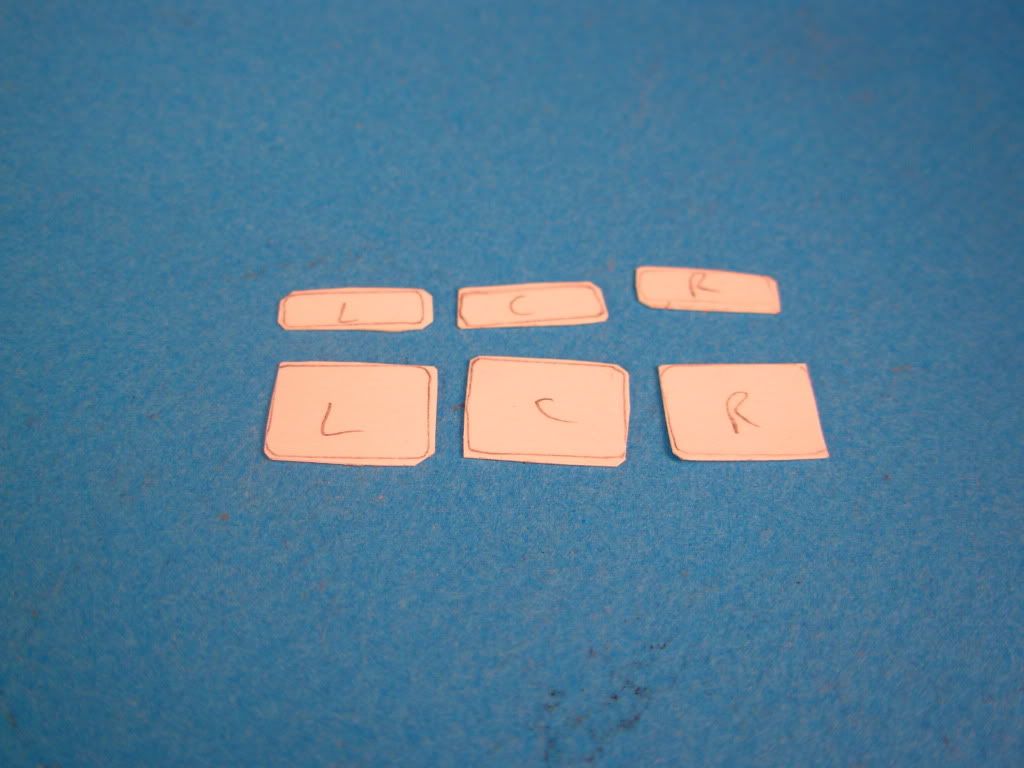
And a quick shot of the raw "glass" I intend to use. Points to anyone but Schnobs who can guess what that package is for:
THen I started on the myriad of tiny outside details, starting with the exhaust. Here's the first part, the tip, nice and solid:
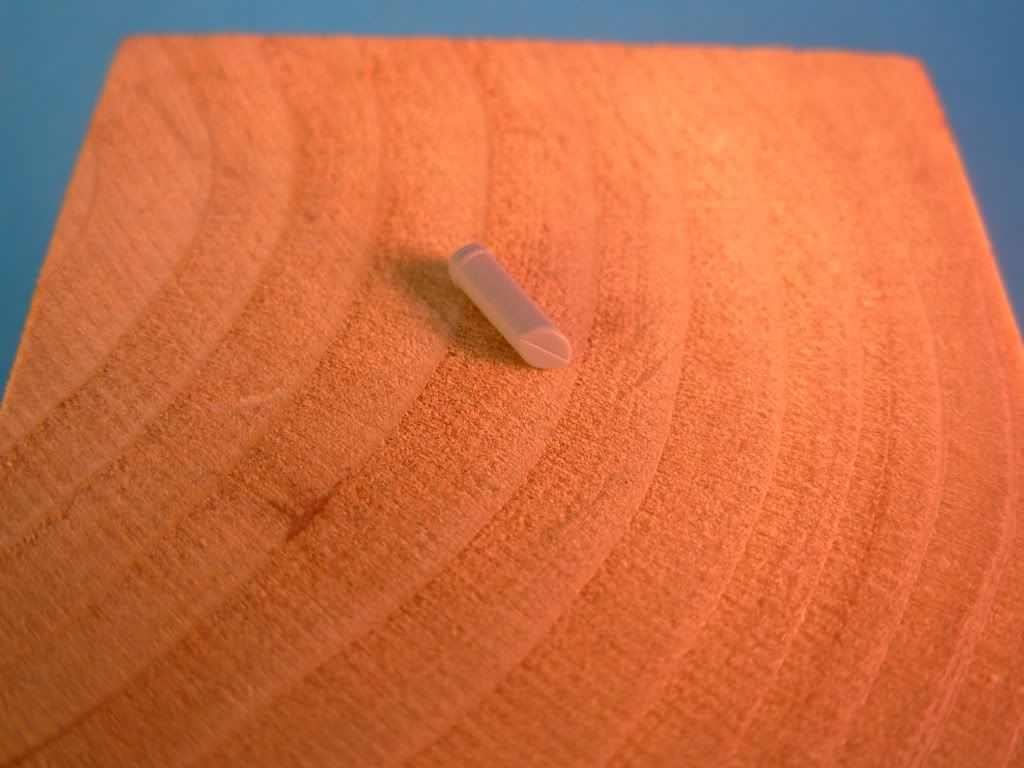
I started to root around for a bit to drill it out, then, brainstorm, I found some brass tubing that I bought for the BA 20 exhaust, and here we have a realistic ( I hope) tip.
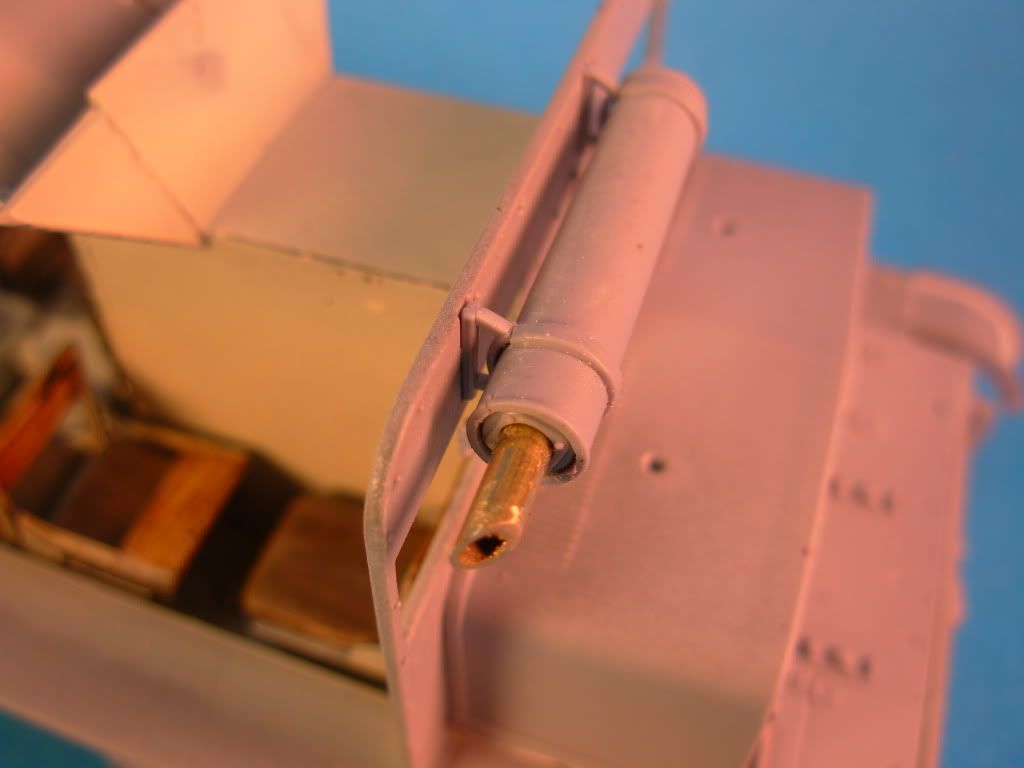
And here is the overlal shot, that thing didn't fit very well at all, I needed a couple extra hands
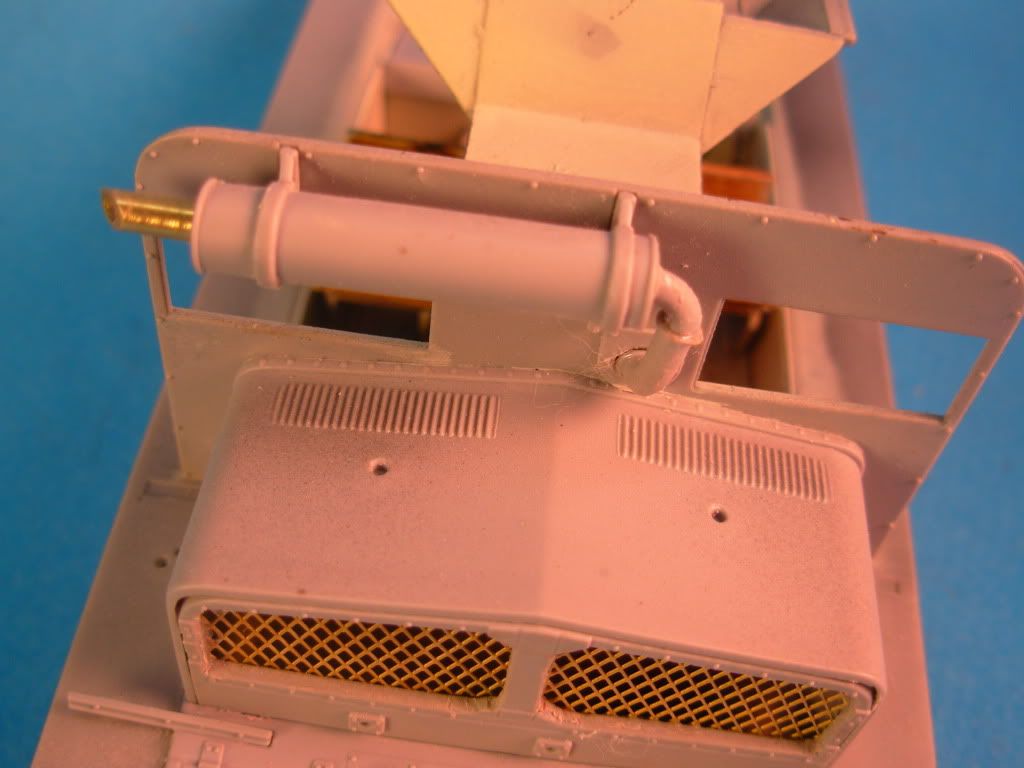
THen I started with some other smaller details, check these fender supports for WOW does that not fit well. Combination the fenders took on a droop to get them flush with the hull, and the top plate is also warped. Check these clearances, anyone have any suggestions? I can CA them down and they will look bent, not out of the question, or they can remain straight and I can rip some holes in the fender and they can be "torn off."

That's where we sit tonight, I will next drill another couple hundred thousand Fruil links, maybe get the first run finished.
Please weigh in with any comments, especially with teh fender supports.
Thanks, guys,
Bill