Greetings Folks. I am still here, and I am still working on this. I am currently focused on the stern. That section has three windows, of which are molded in solid brown plastic. From what I can tell, the actual ship had glass panes in them. Thus, I want the windows to be transparent. The windows are pretty tiny, and that limits me to what I can pull off to fix the problem, without destroying the intricate detail. After all said and done, I decided to make a whole new piece out of clear resin. Then, I will attach it to the hull, and I will mask the windows during paint. Time will tell if my plan works.
Learning to work with molds and resins ate up a bunch of my time. I tried a couple of mold compounds and I found one that worked pretty well. Once the mold hardened, I made some castings. My first attempts had some bubbles that reached clear through to the surface of the piece. In short, they formed divots on the surface, and ruining the piece. After some experimenting though, I was able to cast a decent copy.
I did have an oops in all this. In making the mold it is often recommended to use modeling clay to set the master piece in. In my case, I used Sculpey clay. This was a mistake. When it came time to pull the piece out of the clay, I found that the clay turned the plastic to goo! There were gooey strings and all! It was quite the sight. It was a bit of a bummer because I wanted to keep that piece intact, just in case my master master plan failed. Unfortunately, the plastic melted enough that is compromised the strength of the piece. In light of the goo scenario, it seems that I am committed to the resin piece.
Question: What is the best method to join the resin piece to the styrene hull? These have two dissimilar properties. I am thinking epoxy to make that connection. Do you guys have any thoughts on that? Any possible concerns?
Here are some images of the process.
Below: This was earlier on and before tackling the stern. The two hull sections are glued.
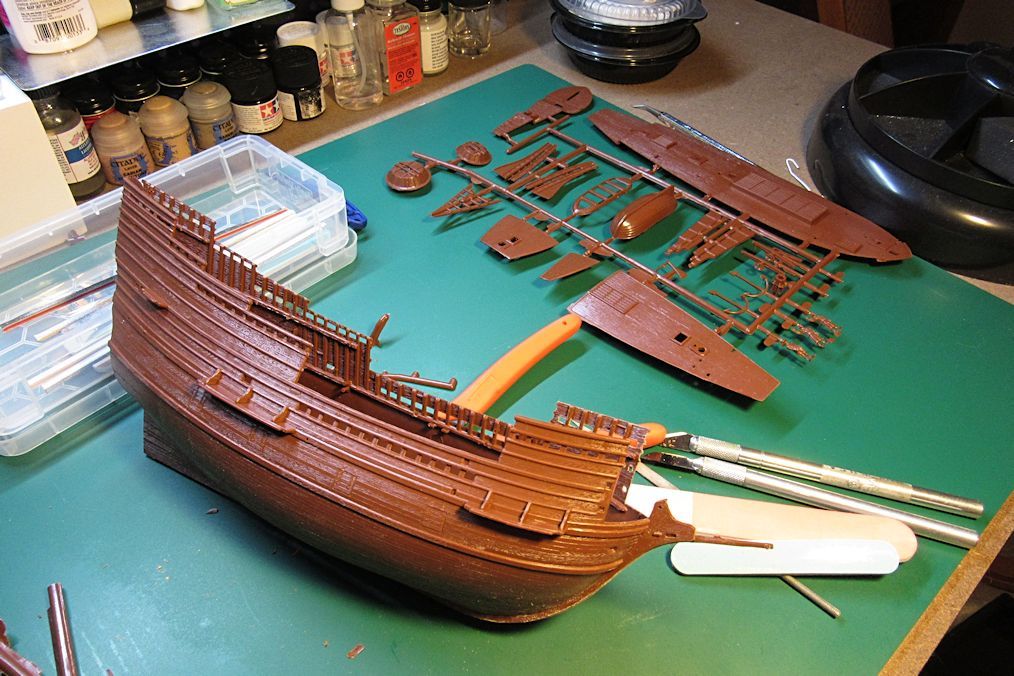
Below: Here is a closeup of the stern section showing the windows.
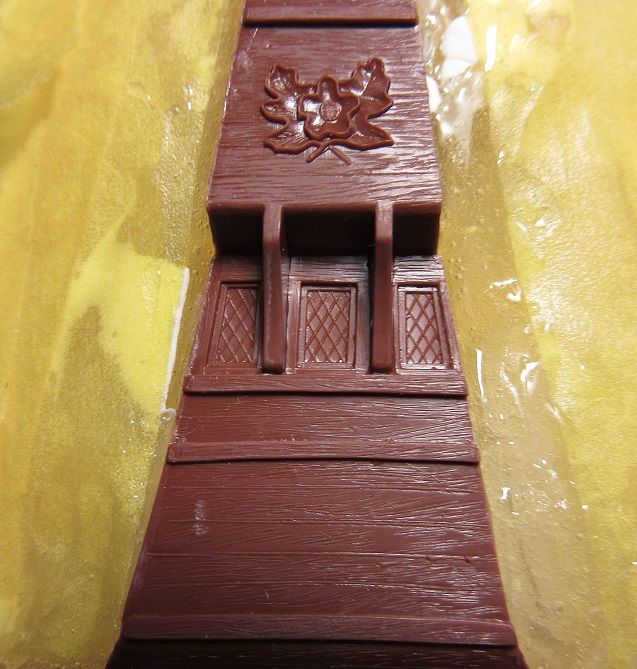
Below: The mold is cured and the master is removed. BTW...this is not when the gooey accident happened. I used a different mold compound prior to this, and it was then that the clay ruined the backside of the piece. For this mold, I epoxied the piece to the cardboard.
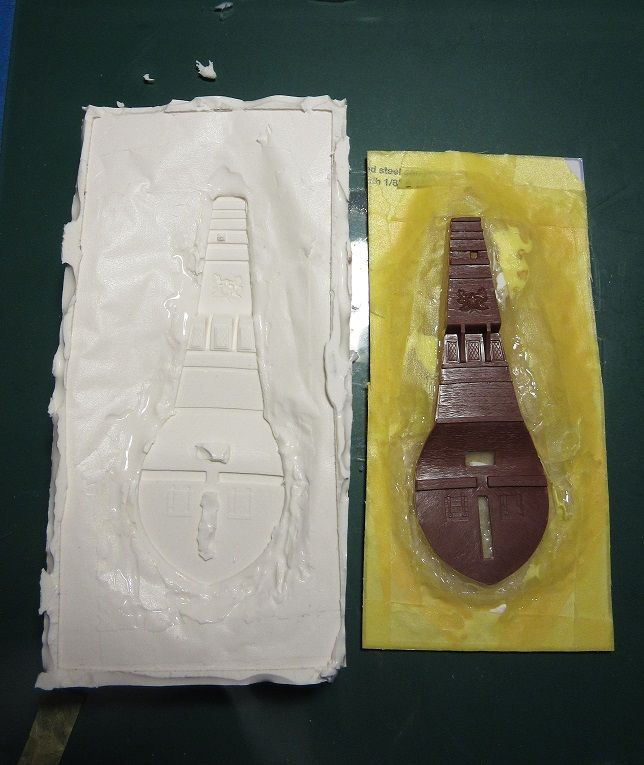
Below: You can see how well the mold captured the intricate detail.

Below: Here is the resin cast. I have some cleanup work to do.
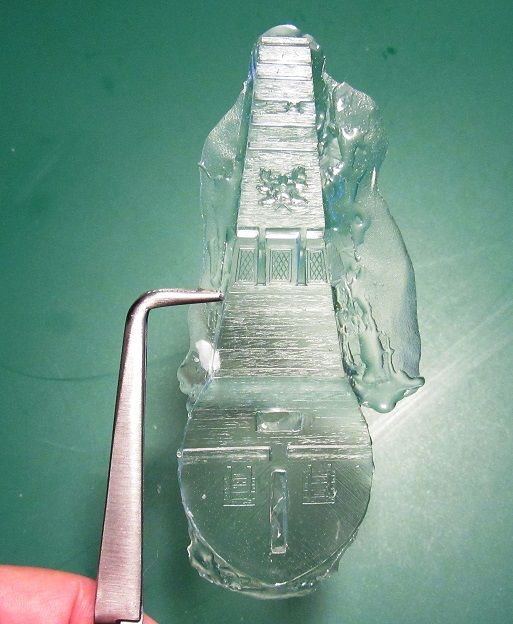