Deck Weathering
The goal this last several weeks was to define a more consistent process. The alternative was pretty much a wing and a prayer. It has been a long slog, but I feel that I have hammered out a procedure that seems to take the guesswork out of it. On a side note, this would have been done last week if I had not missed one seemingly unimportant step in the process. More on that later.
Here is a brief breakdown of the steps. I will go into more detail further down in this post.
1. Paint the deck with acrylic flat white.
2. Mix a brown oil wash and paint the boards.
3. Apply a gray acrylic wash.
4. Paint the grating.
5. Apply the dye wash.
I have said this before... I am amazed at how incredibly difficult it is to image these decks. I have again resorted to HDR photography. Otherwise, the decking would have little tonal detail and zero color. Even with the HDR process I can't seem to capture color that the human eye can see. Admittedly though, I have the color set to be very subtle. Just a reminder... in some cases weird light and color anomalies can occur with HDR. So, the colors are not very accurate and some tonal ranges are exaggerated. I hate to even post these images, but I have to post something. Sadly, this is the best that I can come up with to show you. You will have to take my word for it that there is some color.
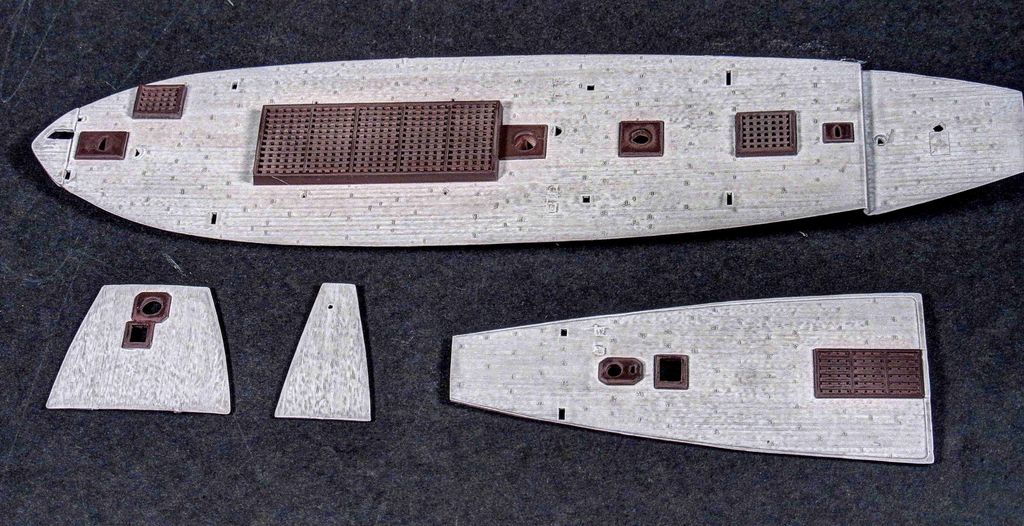
Below: I thought it would be fun to see how the decks look in my scrap hull.
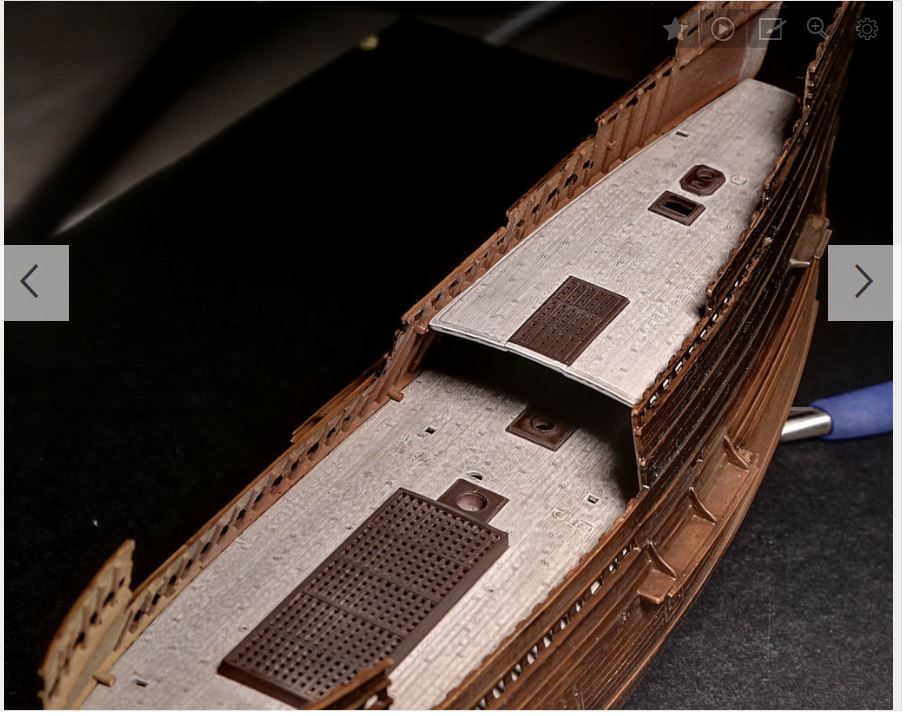
If I have any regrets with the end result of these decks, it would be that I am not too happy about the work that I did on the plugs. My impatience kicked in after a series of setbacks and re-dos. Ultimately, I rushed through the process of applying the surface putty. The ladders will hide some of this though and I don't feel that the problem is so terrible. One thing is for sure... I am in no mood to start over. This is a case for what JT likes to nudge me on, that the next model will be better.
Here is more detail for those that are interested.
Step 1: There is not much to say here. Painting the deck white seems to be the best color to start with. This helps ensure that the subsequent steps don't end up making the final colors too dark.
Step 2: This step changed. With the previous process I had applied a wash over the entire deck. I found that I could get a more realistic look by brush painting the wash onto each plank. I alternated areas of coverage, but I tried not to leave too many areas that do not have some wash applied.
I used Artist Van *** Brown for this. I made the wash so thin that when it is applied it produces a stain at best. This is important because if you go too heavy it undermines the look that you will get in the end. By the way, some credit goes to GMorrison for telling me about his plank painting process. It got me thinking. Thanks Morrison.
Step 3: This is an entirely new step, and there are two reason for it. The gray wash acts as a filter. It blends step 1 with step 2 giving it a more realistic look. The second reason fo the gray wash is that it tones down the almost white/gray tone that you get by the end of all this. I prefer an overall darker gray that could simulate dirt and or, water staining.
The gray paint that I used is acrylic, made by Liquitex. I found it at Michaels. This is interesting stuff. It goes on very much like a wash. In its own right, it does a decent job highlighting the woodgrain. With the dye added later on, the two seem to work together and further enhance the woodgrain effect.
You can apply it straight from the bottle using a brush, but I highly recommend an additional step. I would suggest that you add some of the paint into a paint pallet, or whatever you prefer, and then include some acrylic flow improver. This is a step that I didn't do last week. Based on previous testing I didn't think that I needed to, and the end result was a complete do-over. What happened was that the paint was slightly too viscous and more importantly, it was drying too fast. That left me with some serious brush marks on the main deck.
So... add a few drops of flow improver to the paint. This buys you time to get the coverage that you need and it really helps to minimize brush marks. Phew...
One other thing about this paint. I do not recommend airbrushing it for this purpose. Rather than going on like a wash, airbrushing causes the paint to spray like any other paint. It coats the deck in a nice gray paint layer and you lose all the underlying work that you did. I recommend that you use a larger flat brush to apply it.
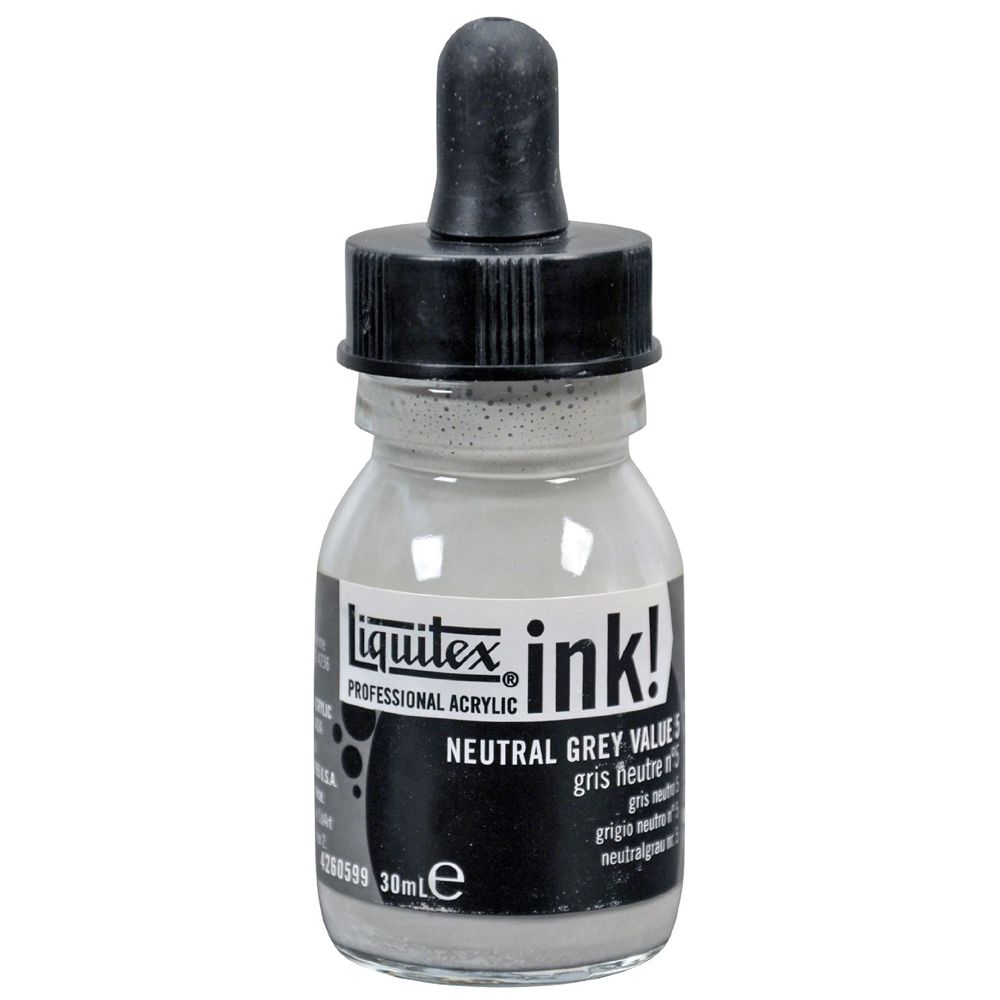
Step 4: Paint the coaming/grating. I recommend doing this before the dye is applied because the dye helps accentuate the paintwork. Also, the IPA used with the dye tends to give acrylic paint a bleached look, and it does it at varying degrees depending on where the IPA sits the longest. This is my experience with using Tamiya brand anyway; I don't know about other brands. So, this helps to weather the paint in one easy step.
Step 5: Apply the dye. However, rather than brush it on like how I did it at first, I airbrushed it on. This eliminates the problem that I was having earlier. If you recall that at times the IPA softened the underlying paint and this made it too easy to smear all your work whilst brushing it on. Not good. I want to thank Rob for this idea. He mentioned that he uses a spray bottle. I didn't have a spray bottle, so I used an airbrush.
The Mixture: I can't say that my mixture is the best way to go, but for those that want to try this, it can be a good starting point for you.
I add IPA to an airbrush jar so that its about half full. I then put three drops of Dye-na-flow into the jar and mix it. Be careful about using a dye soaked stick for mixing. The dye on the stick adds to the color in the jar; this is strong stuff. I like to build up the effect verses taking a chance of going too strong. I grab a clean stick for mixing.
Spray the deck liberally, and then allow the IPA to evaporate off. If you have a dual action airbrush you can use the brush to blow air onto the wet deck. This dramatically speeds up the drying time. You can use this as a way to control the bleaching effect as well.
Check the coverage/effect and decide if you want to add another coat. It might take several coats depending on how thin a mixture it is. I sprayed about 6 coats in the example images. The look is subjective, so it's up to you.
Final thoughts
I am on the fence about what I have come up with. Part of this doubt might be because I have been looking at this problem for too long. What I do feel pretty certain about though is that I can't go much farther with this particular process. I have tried every angle that I can think of to tweak things, and this is the closest that I can get. Based on that alone, I will have to call it complete.