Well, as I thought through this more, I realized that I have to sort out the observation area before I can sort out the light.
Below: Here is how the cabin dio folds together. As Emmet Brown said in the movie Back to the Future, "please excuse the crudity of this model."
This is loosely taped and this is not the actual piece. I first practiced on the instructions.

Below: Here is how it sits within the model.

Below: Here is a rough gander at how it will look. Again, everything is loosely taped.

Being a guy that always looks to improve things, I tried to. I spent a good two hours cutting and fitting styrene sheets in an effort to get a better fit. In the end, I concluded that the designers of this foldout have it close enough.
So now what? I was not happy with the sloppiness of the paper. I know ... I will back each piece of paper with styrene. This should give me a tighter and more solid assembly. And that is what I set out to do.
Below: I started with this side wall. As I was fitting this I noticed that light comes through the map. Apparently, this was by design. So, I cut a corresponding shape in the styrene backing so that the map will remain illuminated.
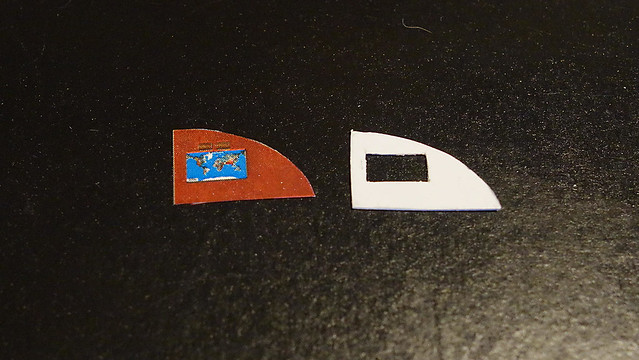
Below: As it is coming together.
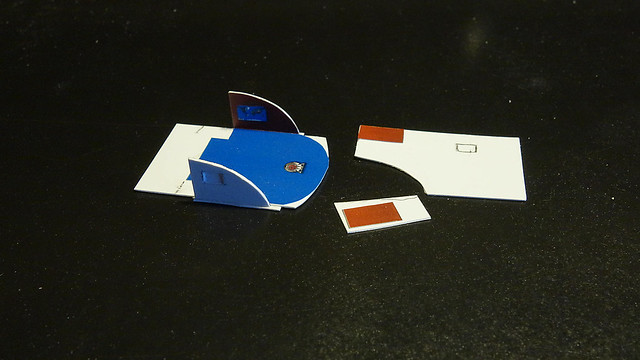
Below: It is complete. It still looks crude but I think that it's better than before.
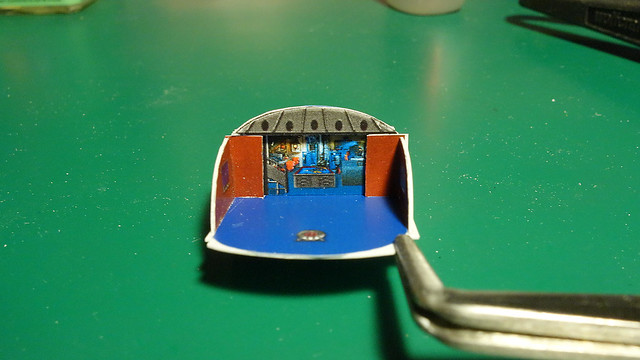
Below: You can see how light shines through the graphics. It is too bad that the quality of the graphic isn't better, but I suppose at this scale, who will notice.
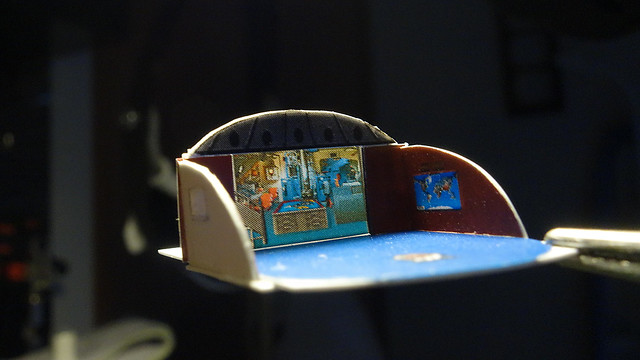
I have two more things that I want to try before I will call this assembly done. I will attempt to add some beams that will curve along the edge of the side pieces. I will also try to fabricate one that will travel back from the middle section of the window. Secondly, I might add a few chairs.
Below: Here is a screenshot of how the beams look. This image is from the movie version, the TV series is somewhat different. I am not too concerned about this. My goal is to get something that resembles a beam.
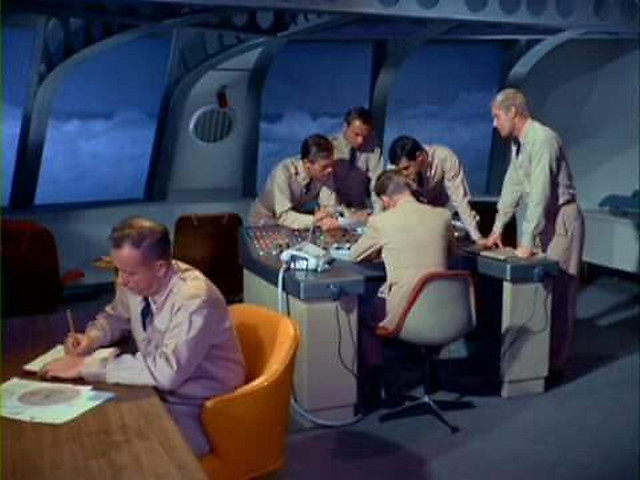
Below:
Captain!
Look!
There is a man peering into the observation windows!
Look out! He has a sanding stick!!!
